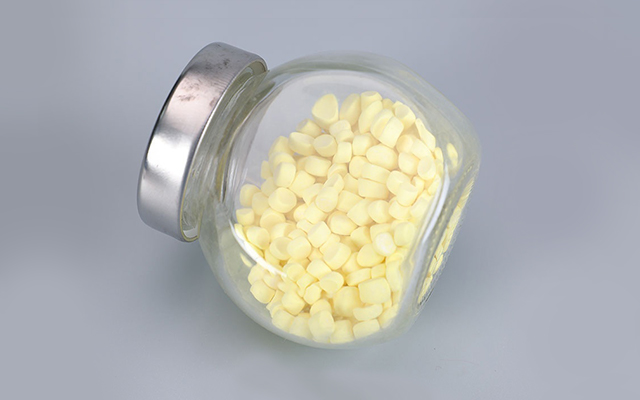
Background
Rubber vulcanization is a crucial process that transforms elastomers, initially possessing weak thermoplastic properties, into a robust, elastic, and durable substance with enhanced properties. This transformation involves introducing a network of cross-links into the elastomers, thereby significantly improving their mechanical and chemical characteristics. It’s important to note that the tensile strength of the vulcanized rubber is at its maximum when cured optimally.
The vulcanization process involves subjecting rubber to heat and pressure, which initiates a chemical reaction. This reaction forms cross-links between the polymer chains, enhancing the rubber’s strength and resilience. However, it’s crucial to achieve the optimum cure, as excessive vulcanization can result in overcured rubber. Overcured rubber becomes stiffer and harder but, paradoxically, weaker and less extensible.
Solutions

Techniques of Vulcanization
Several techniques are employed for rubber vulcanization, catering to different manufacturing needs and preferences:
1、Compression Moulding:
Description: This is the most commonly used method in the industry. The process involves placing the rubber blank in a two-piece mould, one part of which is movable and the other stationary.
Procedure: After placing the blank, the mould is closed, and heat and pressure are applied. This causes the material to flow and fill the mould. A slight excess of material is often used to ensure complete mould filling.
2、Transfer Moulding:
Description: A variation of compression moulding, this technique involves placing the rubber blank in a separate chamber (pot) preheated to a temperature below the cure temperature. The blank is then transferred into the heated mould for the vulcanization process.
Advantages: Although the moulds are more expensive, the process has a shorter cure time due to the use of higher temperatures, and there is better heat transfer.
3、Injection Moulding:
Description: While injection moulding is more commonly associated with plastics, it can also be used for rubber articles. The polymer is preheated in a cylindrical chamber to a flowable temperature and then forced into a closed mould cavity under high pressure.
Advantages: This technique offers a significant advantage in terms of speed, as articles can be produced in seconds. While more commonly used for plastics, it finds application in rubber molding as well.
Understanding and implementing these vulcanization techniques are essential for achieving the desired material properties and ensuring the efficient production of high-quality rubber products.
Related Products To Complete Your Project
In Needs of Rubber Vulcanization Accelerators Solution?
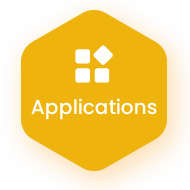
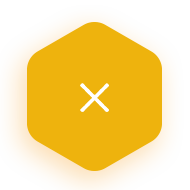