TMTD Rubber Accelerator: Optimizing Rubber Curing
16/08/2024
What is TMTD Rubber Accelerator? TMTD (Tetramethylthiuram Disulfide) rubber accelerator is a crucial chemical in the rubber industry. It is primarily used to speed up the vulcanization process of rubber, significantly enhancing production efficiency and improving the final product’s quality. Vulcanization is a chemical process for converting rubber into more durable materials by forming cross-links between individual polymer chains.
TMTD is widely recognized for its effectiveness in both natural and synthetic rubber, providing excellent cure efficiency and a high degree of cross-linking. This accelerator is particularly valued for its ability to function at lower temperatures and its compatibility with various other accelerators, making it a versatile and essential component in rubber manufacturing.
Introduction to TMTD Rubber Accelerator
Chemical Composition and Properties
TMTD is characterized by its chemical formula C6H12N2S4. It appears as a white or light yellow powder and has a melting point of around 142-146°C. Its molecular structure allows it to act as a primary accelerator, providing rapid vulcanization, or as a secondary accelerator to enhance the activity of other accelerators.
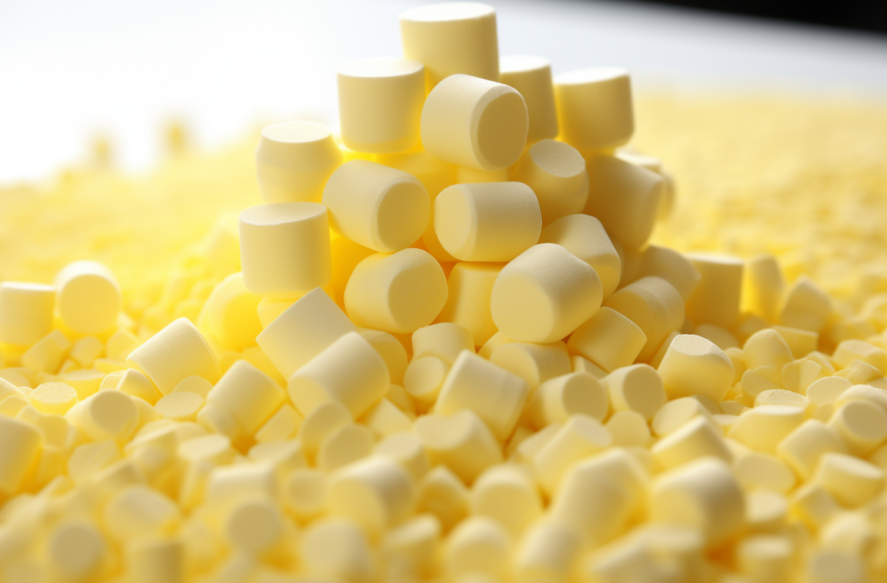
This accelerator is known for its high solubility in rubber, which ensures uniform distribution and consistent curing. Additionally, TMTD exhibits excellent scorch safety, meaning it does not cause premature vulcanization during processing, thus providing manufacturers with greater control over the curing process.
Applications in the Rubber Industry
TMTD is used in various rubber products, including tires, hoses, belts, and molded goods. Its ability to provide a fast cure makes it ideal for high-speed production processes. Moreover, TMTD is utilized in the production of latex products, where it helps achieve the desired elasticity and resilience.
In tire manufacturing, TMTD contributes to the durability and performance of tires by enhancing their resistance to heat and mechanical stress. In industrial applications, TMTD ensures that rubber components maintain their integrity and functionality under harsh conditions, thus extending the lifespan of products such as conveyor belts and automotive parts.
Mechanism of TMTD Rubber Accelerator
Vulcanization Process Enhancement
The primary role of TMTD in rubber processing is to accelerate the vulcanization process. During vulcanization, sulfur atoms form cross-links between polymer chains, transforming the rubber from a sticky, pliable material into a strong, elastic one. TMTD facilitates this cross-linking by decomposing into reactive intermediates that interact with sulfur and rubber molecules.
This interaction speeds up the formation of cross-links, reducing the time required for vulcanization and increasing the efficiency of the process. As a result, manufacturers can achieve higher production rates and better control over the physical properties of the final product.
Synergistic Effects with Other Accelerators
TMTD is often used in combination with other accelerators to achieve optimal curing results. When used as a secondary accelerator, TMTD enhances the activity of primary accelerators, such as MBT (Mercaptobenzothiazole) or CBS (Cyclohexylbenzothiazole Sulfenamide). This synergistic effect allows for a more efficient and balanced vulcanization process, leading to improved mechanical properties and overall performance of the rubber.
By adjusting the ratio of TMTD to other accelerators, manufacturers can fine-tune the curing characteristics to meet specific requirements, such as hardness, elasticity, and resistance to aging and environmental factors. This flexibility is particularly valuable in producing specialized rubber products with tailored properties.
Impact on Product Quality and Performance
The use of TMTD as a rubber accelerator directly influences the quality and performance of the final product. Accelerated vulcanization with TMTD results in rubber with enhanced tensile strength, elasticity, and resistance to wear and tear. These properties are crucial for applications where durability and reliability are paramount, such as in automotive tires and industrial rubber components.
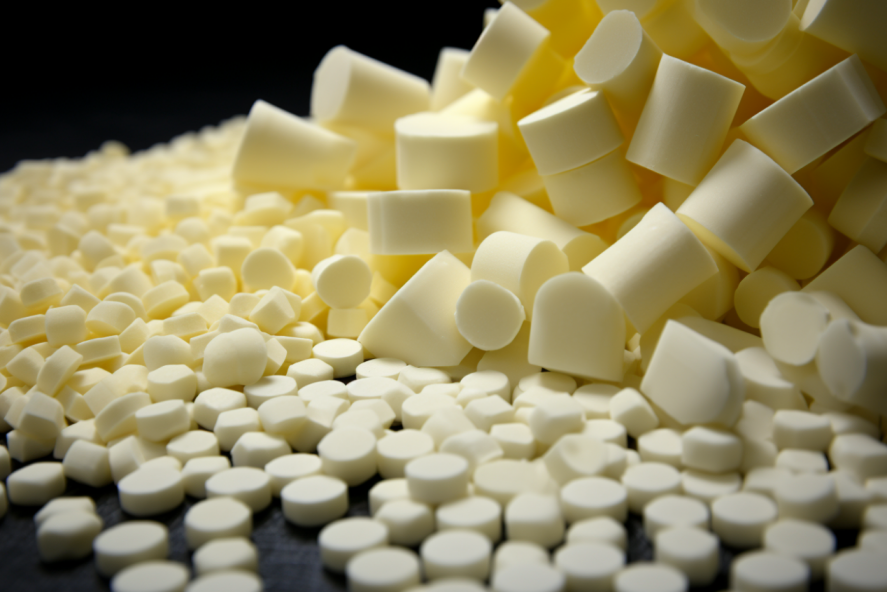
Furthermore, TMTD-accelerated rubber exhibits improved resistance to thermal and oxidative degradation, ensuring that products maintain their performance over extended periods and under varying environmental conditions. This longevity translates to cost savings for manufacturers and end-users, as products require less frequent replacement and maintenance.
Industry Dynamics and Market Trends
Market Growth and Projections
According to statistics and forecasts, the global market for rubber processing additives, including TMTD accelerators, reached a sales value of $2.195 billion in 2023. It is projected to grow to $2.97 billion by 2030, with a compound annual growth rate (CAGR) of 4.5% from 2024 to 2030. This growth is driven by the increasing demand for rubber products across various industries, including automotive, construction, and consumer goods.
The rising need for high-performance rubber materials, coupled with advancements in rubber processing technologies, is expected to fuel the demand for TMTD accelerators. Additionally, the growing focus on sustainable and eco-friendly manufacturing practices is likely to spur the development and adoption of new formulations and alternatives that reduce the environmental impact of rubber production.
Growth Drivers
Several factors contribute to the growth of the TMTD rubber accelerator market. One of the primary drivers is the expanding automotive industry, which demands high-quality rubber components for tires, belts, and seals. The increasing production of electric vehicles, which require specialized rubber parts with enhanced performance characteristics, further boosts the demand for TMTD accelerators.
Another significant driver is the construction industry’s growth, which relies on rubber materials for insulation, sealing, and vibration dampening. The rising infrastructure development activities worldwide create a substantial market for rubber products, thereby increasing the demand for accelerators like TMTD.
Moreover, the growing consumer preference for durable and high-performance goods drives the demand for advanced rubber materials in various applications, from footwear to sporting goods. This trend, coupled with the continuous innovation in rubber processing technologies, is expected to sustain the market growth for TMTD accelerators.
Development Opportunities
The TMTD rubber accelerator market presents numerous opportunities for development and innovation. One key area is the formulation of eco-friendly accelerators that minimize the environmental impact of rubber production. Manufacturers are increasingly focusing on developing non-toxic, biodegradable alternatives to traditional accelerators, addressing the regulatory and consumer demands for sustainable products.
Advancements in nanotechnology and material science also offer promising opportunities for enhancing the performance of TMTD accelerators. By incorporating nanomaterials and optimizing the molecular structure of accelerators, researchers aim to achieve faster curing times, improved mechanical properties, and greater resistance to environmental factors.
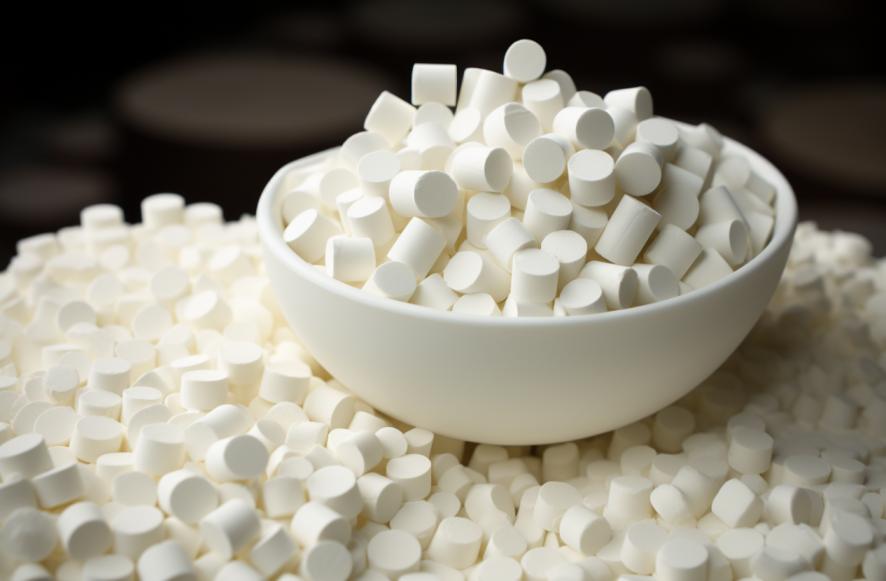
Furthermore, the growing emphasis on circular economy practices encourages the recycling and reuse of rubber materials. Innovations in rubber recycling technologies, coupled with the development of accelerators that facilitate the recycling process, present significant growth opportunities for the TMTD market.
Favorable Factors
Several favorable factors support the growth and adoption of TMTD rubber accelerators. Firstly, the well-established manufacturing infrastructure and expertise in the rubber industry provide a strong foundation for the production and application of TMTD accelerators. The availability of skilled labor, advanced machinery, and extensive research capabilities enables manufacturers to meet the growing demand for high-performance rubber materials.
Secondly, the continuous advancements in rubber processing technologies and the increasing automation of production processes enhance the efficiency and consistency of TMTD-accelerated rubber products. These technological improvements reduce production costs, improve product quality, and enable manufacturers to respond quickly to market demands.
Challenges and Obstacles
Despite the positive growth outlook, the TMTD rubber accelerator market faces several challenges and obstacles. One significant challenge is the stringent regulatory environment governing the use of chemical additives in rubber processing. Increasingly stringent regulations on the use of hazardous substances and the need for compliance with environmental and safety standards necessitate the development of safer and more sustainable alternatives to traditional accelerators.
Additionally, the volatility in raw material prices and the fluctuations in global supply chains pose challenges to the cost-effective production of TMTD accelerators. Manufacturers must navigate these uncertainties by optimizing their supply chain management and exploring alternative sourcing strategies.
Moreover, the growing competition from alternative rubber accelerators and the emergence of new technologies present challenges to the market position of TMTD. To remain competitive, manufacturers must continuously innovate and improve their products’ performance and environmental profile.
Supplier Spotlight: CHEMBROAD
Overview of CHEMBROAD
CHEMBROAD is a leading supplier of TMTD rubber accelerators, known for its commitment to quality, innovation, and customer satisfaction. With extensive experience in the chemical industry, CHEMBROAD has established itself as a reliable partner for rubber manufacturers worldwide.
The company’s product portfolio includes a wide range of rubber accelerators, antioxidants, and other processing aids, designed to meet the diverse needs of the rubber industry. CHEMBROAD’s TMTD accelerators are renowned for their high purity, consistent quality, and excellent performance, making them a preferred choice for manufacturers seeking reliable and efficient vulcanization solutions.
Commitment to Quality and Sustainability
CHEMBROAD places a strong emphasis on quality control and sustainability. The company’s state-of-the-art production facilities adhere to stringent quality standards, ensuring that every batch of TMTD accelerator meets the highest performance and safety requirements. Rigorous testing and quality assurance processes guarantee the consistent quality and reliability of CHEMBROAD’s products.
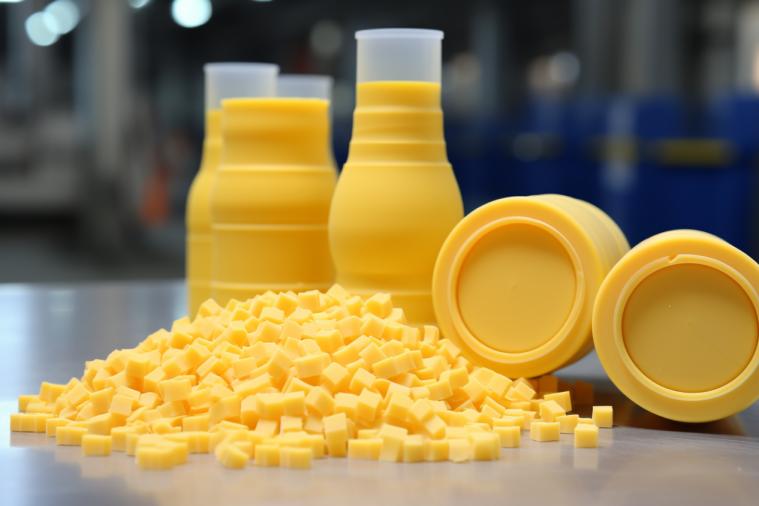
In line with the growing demand for eco-friendly solutions, CHEMBROAD is actively engaged in developing sustainable alternatives to traditional accelerators. The company’s research and development efforts focus on creating non-toxic, biodegradable accelerators that reduce the environmental impact of rubber production while maintaining superior performance characteristics.
Customer-Centric Approach
CHEMBROAD’s customer-centric approach sets it apart in the competitive landscape. The company works closely with its clients to understand their specific requirements and provide tailored solutions that meet their unique needs. Comprehensive technical support, responsive customer service, and timely delivery are hallmarks of CHEMBROAD’s commitment to customer satisfaction.
Conclusion
By continuously investing in research and development, CHEMBROAD ensures that its products remain at the forefront of technological advancements in the rubber industry. The company’s dedication to innovation, quality, and sustainability positions it as a trusted partner for rubber manufacturers seeking high.