Streamlining Production: TBBS Rubber Accelerator for Industrial Scale
31/10/2024
In the rapidly evolving realm of industrial rubber production, the essence of efficiency cannot be overstated. Have you ever considered that selecting the appropriate rubber accelerator can drastically shorten processing durations while simultaneously enhancing the overall performance of the final product? Among the various accelerators available, TBBS (N-tert-butyl-2-benzothiazolesulfenamide) emerges as a pivotal element in the rubber vulcanization process. This article delves into the transformative impact of TBBS on the industry, highlighting its ability to streamline production, address prevalent challenges, and optimize output.
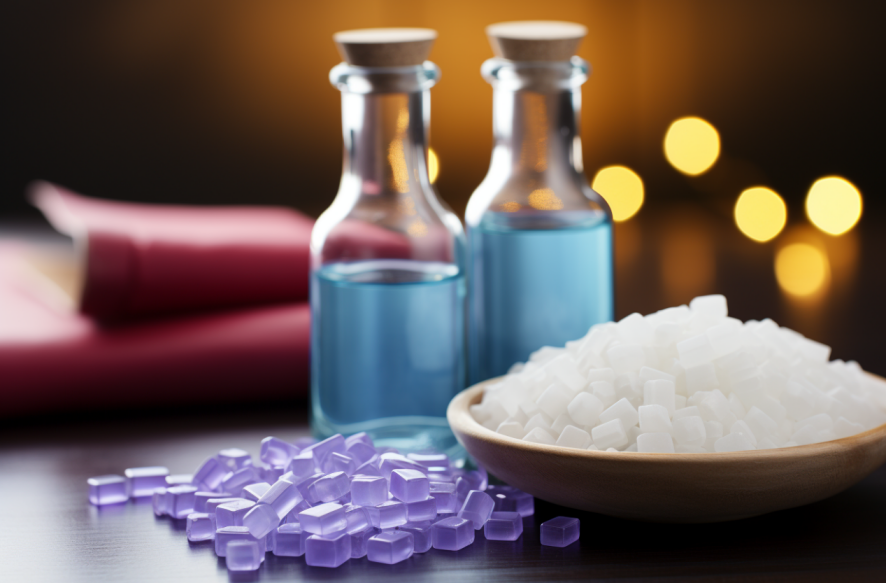
Navigating the Challenges of Industrial Rubber Production with TBBS
Addressing Common Production Issues
Manufacturers in the industrial rubber sector frequently encounter numerous challenges, including prolonged curing times, inconsistent quality of products, and complications in processing diverse rubber compounds. The TBBS rubber accelerator serves as a solution to alleviate these difficulties by expediting the vulcanization process, thereby facilitating swifter production cycles. This advantage is particularly critical in high-demand sectors, such as automotive and construction, where the prompt delivery of products is of utmost importance.
Enhancing Quality Control
With the integration of TBBS, manufacturers can achieve a more consistent vulcanization process, which directly correlates with the uniformity of the rubber’s mechanical properties. Such consistency leads to improved durability, resistance to abrasion, and an overall enhancement in the performance of the final product. Consequently, industries dependent on rubber components—such as tires, seals, and gaskets—can anticipate elevated quality standards, ultimately reducing defect rates and minimizing product returns.
Overcoming Compatibility Challenges
TBBS exhibits compatibility with a broad spectrum of rubber compounds, including SBR (styrene-butadiene rubber) and butyl rubber. This remarkable versatility enables manufacturers to customize their formulations according to specific application demands, ranging from automotive tires to industrial seals. By incorporating TBBS into their manufacturing processes, companies can navigate the complexities associated with employing multiple accelerators, thereby simplifying their supply chain and enhancing production efficiency.
Maximizing Output: The Efficiency of TBBS in Industrial Applications
Accelerated Curing Times
A significant advantage of utilizing TBBS lies in its capacity to markedly decrease curing times. Conventional rubber accelerators often result in extended processing periods, potentially leading to production bottlenecks. In contrast, TBBS facilitates a rapid transition from raw materials to finished products, enabling manufacturers to boost output without sacrificing quality. This heightened efficiency translates into greater profitability and improved management of resources.
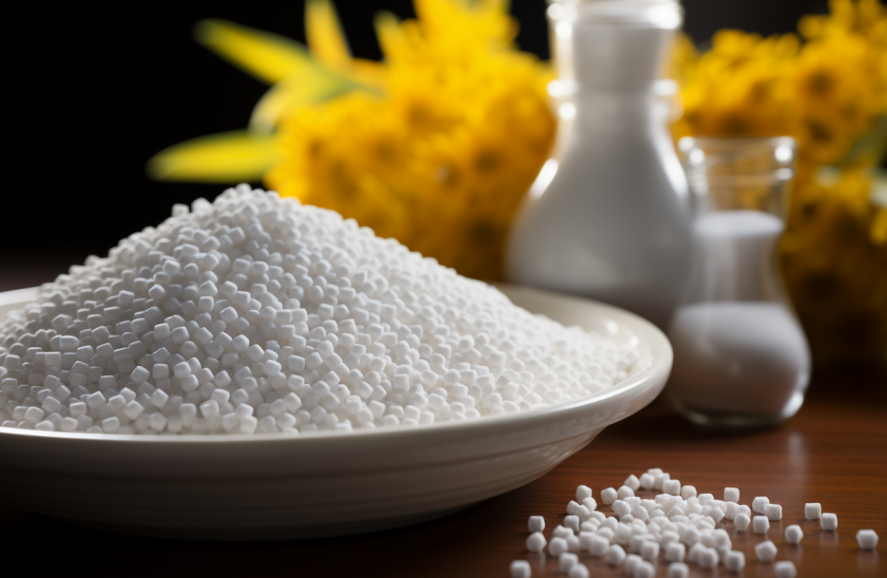
Improved Product Performance
Beyond the aspect of speed, TBBS contributes to the superior performance of rubber products. This accelerator fosters stronger cross-linking during the vulcanization process, yielding rubber that is not only more resilient but also capable of enduring extreme conditions. Industries such as automotive and aerospace greatly benefit from these enhanced properties, as they rely on high-performance materials to ensure safety and reliability.
Cost-Effectiveness
Incorporating TBBS into production methodologies can lead to considerable cost reductions. By enhancing curing efficiency and product quality, manufacturers can diminish waste and lower expenses related to reworking or discarding defective products. Furthermore, the adaptability of TBBS allows its application across numerous uses, optimizing material costs and reducing the need for surplus inventory.
Future Trends: The Role of TBBS in Industrial Rubber Development
Advancements in Rubber Technology
As the rubber industry continues to progress, the necessity for innovative materials and processes escalates. The TBBS rubber accelerator is at the forefront of this evolution, paving the way for novel applications and improved formulations. Collaborative efforts among researchers and manufacturers are underway to explore advanced composites and sustainable rubber solutions, harnessing the properties of TBBS to develop state-of-the-art products.
Sustainability and Environmental Considerations
Amid rising awareness of environmental concerns, the rubber industry is actively pursuing sustainable alternatives. TBBS is integral to this movement, as it contributes to more efficient production processes that minimize energy consumption and waste generation. By optimizing rubber formulations and extending product lifespans, TBBS bolsters the industry’s transition towards more sustainable practices.
Customization and Specialized Applications
As industries increasingly demand specialized rubber products, the versatility of TBBS allows for customized solutions. Manufacturers can collaborate closely with suppliers, such as Shanghai Chembroad New Materials Co., Ltd., to create tailored TBBS formulations that fulfill specific performance requirements. This degree of customization empowers businesses to tackle unique challenges while enhancing their competitive positioning in the market.
Optimal Solutions for Various Applications
A Diverse Range of Technical Products
Central to effective rubber production is a thorough comprehension of material properties and their applications. The TBBS rubber accelerator assumes a critical role across diverse industries, from tire manufacturing to medical supplies. Its adaptability permits manufacturers to investigate a wide array of applications, ensuring optimal performance irrespective of the end product.
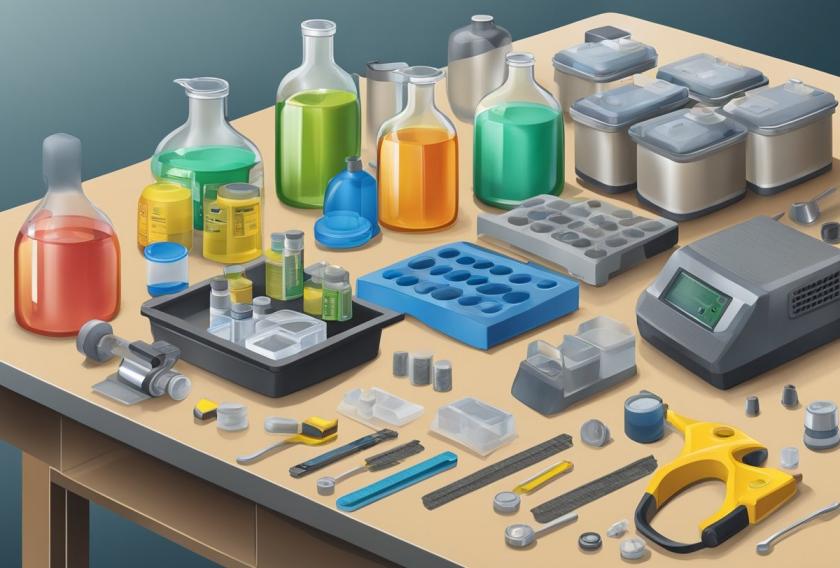
SBR Rubber: Properties, Applications, and Uses
SBR rubber is renowned for its cost-effectiveness and resistance to abrasion. Developed initially in the 1930s, SBR has become a cornerstone in the automotive industry. When combined with TBBS, SBR can achieve enhanced curing times and improved performance characteristics, making it a preferred choice for tires and other high-wear applications.
Butyl Rubber: Advanced Solutions for Diverse Applications
Celebrated for its impermeability and resilience, butyl rubber plays a crucial role in sectors such as medical devices and adhesives. The incorporation of TBBS enhances the curing process, enabling the production of high-quality butyl rubber products that comply with rigorous industry standards. This combination not only boosts performance but also supports sustainability initiatives within manufacturing.
Understanding Rubber Vulcanization and Its Processes
The Importance of Vulcanization
Vulcanization represents a vital process in rubber manufacturing, transforming raw elastomers into robust and elastic materials. By introducing cross-links through accelerators like TBBS, manufacturers can substantially elevate the mechanical and chemical properties of rubber. This transformation is essential for producing high-performance products that can withstand diverse environmental conditions.
The Role of TBBS in the Vulcanization Process
TBBS accelerates the vulcanization process by promoting efficient cross-linking, resulting in rubber with superior tensile strength and elasticity. The meticulous formulation of TBBS guarantees that manufacturers can achieve optimal curing conditions, culminating in end products that align with customer expectations.
Future of Rubber Vulcanization
As technology advances, the methods and materials utilized in rubber vulcanization are set to evolve continuously. Ongoing research and development concerning accelerators like TBBS will play a crucial role in enhancing the efficiency and sustainability of rubber manufacturing processes. By remaining attuned to industry trends, manufacturers can ensure that their products meet future demands effectively.
Conclusion: The Value of TBBS in Industrial Rubber Production
In summary, the TBBS rubber accelerator stands as an indispensable component for industrial rubber manufacturers seeking to refine their production processes. By streamlining operations, enhancing product quality, and promoting sustainability, TBBS asserts its significance within the rubber industry. As companies such as Shanghai Chembroad New Materials Co., Ltd. persist in their innovation efforts and provide customized solutions, the outlook for rubber production appears promising, with TBBS spearheading advancements toward increased efficiency and superior performance.