Styrene Butadiene Thermoplastic Elastomer Guide
20/01/2024
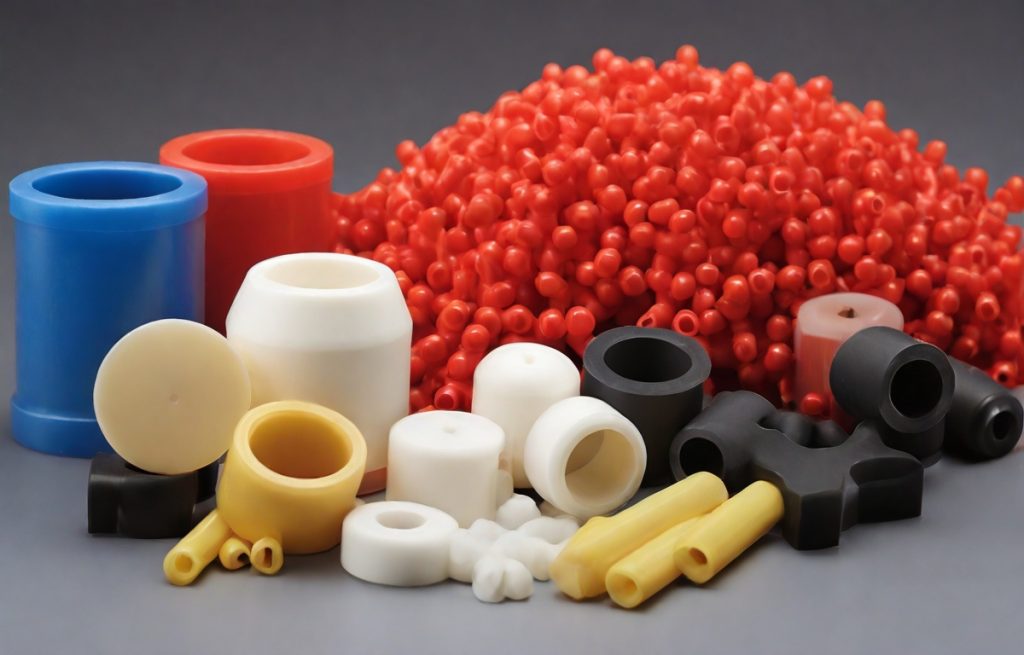
Welcome to our comprehensive guide on styrene butadiene thermoplastic elastomer (SBS TPE), also known as synthetic rubber. This unique material offers a versatile range of properties that make it suitable for various industrial applications. In this guide, we will explore the composition, properties, applications, and benefits of SBS TPE, along with techniques for processing and molding it effectively.
SBS TPE stands out for its excellent processability, durability, and resistance to chemical and weathering effects among other properties. It has a unique molecular structure that makes it different from other elastomers and polymers. This guide will put you on the right path to understanding SBS TPE and how you can leverage its advantages for your business.
Read on to learn more about this invaluable synthetic rubber.
Understanding Styrene Butadiene Thermoplastic Elastomer
Styrene butadiene thermoplastic elastomer, commonly abbreviated as SBS TPE, is a type of synthetic rubber with unique properties that make it suitable for a wide range of industrial applications. To fully appreciate the advantages of SBS TPE, it is important to understand its composition and properties.
SBS Polymer
SBS polymer is composed of styrene and butadiene monomers that are combined through a process called block copolymerization. The polymer structure consists of polystyrene hard blocks and polybutadiene rubbery blocks. This results in a material that is both rigid and elastic, with excellent mechanical properties.
Thermoplastic Elastomer Properties
As a thermoplastic elastomer (TPE), SBS TPE exhibits the properties of both thermoplastics and elastomers. This means that it can be molded and shaped like a plastic at high temperatures, yet retains the flexibility and elasticity of rubber at ambient temperatures. Additionally, SBS TPE has good chemical resistance, UV stability, and weathering resistance, making it an ideal material for outdoor applications.
In summary, SBS TPE is a versatile synthetic rubber with a unique combination of properties that make it suitable for various applications. Understanding its composition and thermoplastic elastomer properties is crucial for harnessing the full potential of this material.
Styrene Butadiene Rubber vs. Styrene Butadiene Thermoplastic Elastomer
Although similar in composition, styrene butadiene rubber (SBR) and styrene butadiene thermoplastic elastomer (SBS TPE) exhibit diverse characteristics and function differently in industrial applications. While SBR is a true elastomer, SBS TPE is a thermoplastic elastomer with both elastomeric and thermoplastic properties.
SBR is extensively used in the manufacture of tires, shoe soles, and conveyor belts, whereas SBS TPE finds use in a wider range of applications, including automotive parts, medical devices, and consumer products. Unlike SBR, SBS TPE can be processed faster, reducing production time and costs.
Another significant difference between SBR and SBS TPE is their resistance to chemicals and weathering. SBR is known for its high resistance to oil, but it may deteriorate when exposed to UV light and ozone. On the other hand, SBS TPE maintains its physical properties even when exposed to harsh weather conditions and chemicals.
In summary, while SBR remains a popular elastomeric material, SBS TPE offers greater versatility and durability. The unique properties of SBS TPE make it a valuable alternative in various industrial applications, proving to be an excellent solution for companies seeking cost-effective solutions without compromising quality.
Applications of Styrene Butadiene Thermoplastic Elastomer
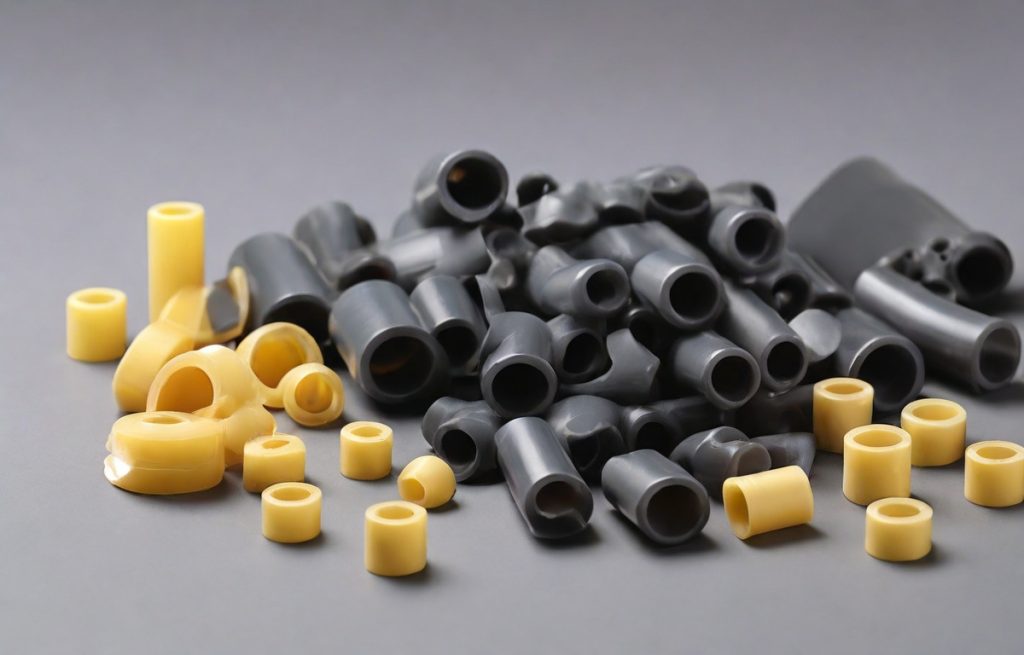
Styrene Butadiene Thermoplastic Elastomer (SBS TPE) is a versatile synthetic rubber that finds extensive use across various industries. One of its key advantages is its wide range of applications, including in footwear, adhesives, roofing, and electrical components.
Footwear
SBS TPE is a popular material for footwear due to its excellent flexibility, slip resistance, and durability. It is commonly used to make shoe soles and can withstand high levels of wear and tear, making shoes more comfortable and long-lasting.
Adhesives
Thanks to its excellent bonding properties, SBS TPE is a popular material for adhesives. It can bind to a wide range of surfaces, making it suitable for use in construction adhesives, automotive adhesives, and medical adhesives.
Roofing
SBS TPE’s resistance to weathering and UV rays makes it an ideal material for roofing applications. It is commonly used in roofing membranes, which offer excellent waterproofing and insulation properties.
Electrical Components
Another key application of SBS TPE is in electrical components such as cables and wires. It offers excellent insulation properties, making it suitable for use in high-temperature environments and providing enhanced safety.
Overall, SBS TPE’s diverse range of applications makes it a valuable material in numerous industrial settings. Its ability to provide improved performance, durability, and safety makes it a popular choice across various sectors.
The Benefits of Styrene Butadiene Thermoplastic Elastomer
Styrene butadiene thermoplastic elastomer (SBS TPE) is widely used because of its numerous benefits. One of the most outstanding properties of SBS TPE is its excellent processability. Its ability to melt and reflow when heated grants manufacturers greater flexibility in creating complex parts and components. Moreover, this thermoplastic elastomer boasts of exceptional durability and resilience. Even under harsh conditions, SBS TPE can maintain its form, shape, and mechanical properties, making it perfect for harsh environments and heavy-duty applications.
SBS TPE is also highly resistant to weathering and chemical agents, making it ideal for use in outdoor applications, such as roofing materials and other building components. Its excellent adhesion to various substrates further expands its range of applications, including use as an adhesive or sealant.
Thanks to its versatility, SBS TPE finds its way into a multitude of industrial applications, including consumer electronics, medical equipment, and even toys. Its ability to adhere to other materials also means that it can frequently replace traditional fastening methods, which improves production efficiency. Whether a business needs a soft, flexible material for a medical device or a durable compound for automotive parts, SBS TPE’s unique properties make it a valuable synthetic rubber.
Processing and Molding Styrene Butadiene Thermoplastic Elastomer
Processing SBS TPE involves several techniques that are crucial to achieve optimal results. Extrusion is the most common method used to process SBS TPE into pellets, which can then be molded into various shapes. Compression molding and injection molding are other techniques that are suitable for SBS TPE.
When molding SBS TPE, it is important to consider the molding temperature, pressure, and duration to ensure the final product has the desired properties. SBS TPE can be molded using a variety of techniques, including overmolding and insert molding, which are suitable for manufacturing intricate shapes and parts.
The processing and molding techniques for SBS TPE are advantageous due to its excellent flow properties, as it can flow into intricate mold shapes without experiencing degradation. The ability to modify the hardness of SBS TPE by varying the ratios of styrene and butadiene monomers also makes it a versatile and convenient elastomeric material for manufacturers.
Styrene Butadiene Thermoplastic Elastomer in the Automotive Industry
Styrene Butadiene Thermoplastic Elastomer (SBS TPE) has emerged as a go-to material for the automotive industry due to its impressive performance and properties. It is widely used in automotive components such as interior and exterior trims, seals, and gaskets, owing to its high elasticity, flexibility, and resistance to wear and tear.
Some specific applications of SBS TPE include dashboard components, door handles, window seals, and intake manifolds. The use of SBS TPE in these parts has contributed to improved safety, comfort, and enhanced driving experience for automobile users.
Aside from its superior performance, SBS TPE’s recyclability and sustainability also align with industry efforts to reduce environmental impact. As manufacturers increasingly prioritize sustainability, SBS TPE is poised to command a larger market share in the automotive industry.
Environmental Considerations and Recycling of Styrene Butadiene Thermoplastic Elastomer
As the push for sustainability gains momentum, it’s becoming increasingly vital to recycle elastomeric materials like SBS TPE. The thermoplastic elastomer properties of SBS TPE make it a viable option for recycling, but there are important environmental considerations to keep in mind.
When recycled, SBS TPE can be turned into various products, including playground surfaces, sports flooring, and waterproof membranes. However, the recycling process does produce waste and emissions that need to be managed appropriately.
One approach to minimizing waste is mechanical recycling, which involves shredding, grinding, and melting the waste material. Chemical recycling is another method that involves breaking down the polymer chains of SBS TPE and re-purifying them for use. Both methods have their advantages and disadvantages and should be evaluated based on the specific needs of each application.
As industries continue to prioritize sustainability, finding ways to recycle materials like SBS TPE will be essential. With proper management and recycling techniques, SBS TPE can contribute to a circular economy and reduce the environmental impact of industrial processes.
Conclusion
In conclusion, styrene butadiene thermoplastic elastomer (SBS TPE) is a highly versatile and durable synthetic rubber that offers unique properties beneficial to various industries. Its composition and thermoplastic elastomer properties make it an excellent choice for a wide range of applications.
By understanding the differences between SBS TPE and other elastomeric materials like styrene butadiene rubber (SBR), businesses can leverage SBS TPE to its full potential. Its extensive use across industries, particularly in the automotive sector, and its contributions to improved safety and comfort highlight its significant role in modern manufacturing.
Furthermore, SBS TPE’s excellent processability and resistance to chemical and weathering effects make it an ideal choice for those seeking a sustainable solution. By prioritizing environmental considerations and exploring recycling options, businesses can incorporate SBS TPE in their manufacturing process while minimizing environmental impact.
Overall, SBS TPE is a valuable synthetic rubber with enormous potential in various applications. As industries continue to innovate and explore sustainable solutions, SBS TPE will undoubtedly play a significant role in shaping the future of manufacturing.
FAQ
What is styrene butadiene thermoplastic elastomer (SBS TPE)?
Styrene butadiene thermoplastic elastomer (SBS TPE) is a synthetic rubber that offers unique properties combining the characteristics of rubber and plastic. It exhibits both elastomeric and thermoplastic behavior, making it highly versatile and suitable for a wide range of industrial applications.
What are the key properties of SBS TPE?
SBS TPE possesses excellent flexibility, resilience, and impact resistance. It has good heat resistance, low-temperature flexibility, and abrasion resistance, making it ideal for applications that require durability and strength. SBS TPE also offers good compatibility with other materials, making it easy to process and mold.
How is SBS TPE different from styrene butadiene rubber (SBR)?
While SBS TPE and styrene butadiene rubber (SBR) share similarities in composition, they have distinct characteristics and applications. SBR is a thermosetting elastomer, meaning it cannot be melted and reshaped like SBS TPE. SBS TPE, on the other hand, is a thermoplastic elastomer that can be melted and reprocessed multiple times.
What are the applications of SBS TPE?
SBS TPE finds extensive use in various industries, including automotive, construction, electronics, footwear, and consumer goods. It is commonly used to produce seals, gaskets, hoses, grips, handles, adhesives, and soft-touch components. SBS TPE’s properties make it particularly suitable for applications that require flexibility, impact resistance, and weathering resistance.
What are the benefits of using SBS TPE?
SBS TPE offers numerous advantages, including excellent processability, easy recycling, and good resistance to chemicals, UV rays, and weathering effects. It provides a wide operating temperature range, maintaining its flexibility even in extreme conditions. SBS TPE also contributes to reduced production costs and increased product lifespan.
What are the processing and molding techniques for SBS TPE?
SBS TPE can be processed using various techniques, including injection molding, extrusion, blow molding, and compression molding. The specific technique depends on the desired shape and properties of the final product. Different molding methods, such as overmolding and insert molding, can also be applied to incorporate SBS TPE into complex designs.
How is SBS TPE used in the automotive industry?
SBS TPE has gained significant popularity in the automotive industry due to its excellent performance and versatility. It is used to manufacture automotive components such as seals, gaskets, interior trims, bumper fascia, and air ducts. SBS TPE’s flexibility, impact resistance, and weathering resistance make it ideal for enhancing safety, comfort, and durability in vehicles.
Can SBS TPE be recycled?
Yes, SBS TPE is recyclable. Proper recycling processes ensure that SBS TPE waste is collected, sorted, and processed into new products or materials. Recycling SBS TPE not only helps reduce waste and conserve resources but also contributes to a more sustainable approach to elastomeric materials.
How can businesses benefit from using SBS TPE?
Businesses that incorporate SBS TPE can enjoy the advantages of a highly versatile and durable material. By utilizing SBS TPE in their products, companies can enhance product performance, increase flexibility in design, improve manufacturing efficiency, and contribute to a more sustainable manufacturing process.