Phenolic resin
Phenolic resin plays a crucial role as a reinforcing agent in the formulation of rubber compounds, enhancing the properties of both natural and synthetic rubbers. It is particularly compatible with rubbers such as butylbenzene, butyronitrile, chloroprene, butyl, and ethylene propylene diene. During processing, the resin exhibits excellent plasticity, facilitating effective dispersion of fillers within the rubber matrix.
One notable advantage of phenolic resin is its ability to undergo plasticization before vulcanization. Following vulcanization, it contributes to improvements in hardness, tear resistance, wear resistance, strength, and elongation of the rubber compound. Additionally, it slightly reduces the compound’s elongation, prolongs scorch time, and lowers Mooney viscosity. This makes phenolic resin a valuable component in the production of various rubber products, including tires, heels, soles, and conveyor belts.
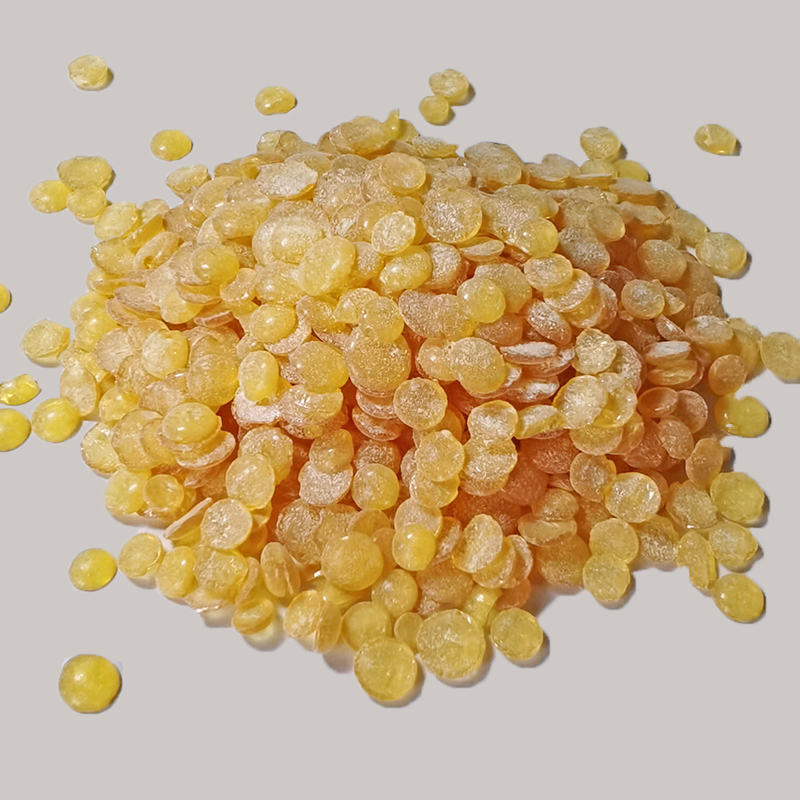
Functions and Characteristics
Softening point / °C | 92-100 |
Ash/% | ≤1.0 |
Free phenol/% | ≤1.0 |
- Softening Point (92-100°C): The softening point indicates the temperature range at which the resin becomes pliable. This property is crucial during processing, ensuring good plasticity for effective dispersion of fillers and other additives.
- Ash Content (≤1.0%): The low ash content suggests that the resin leaves minimal residue upon combustion, which is desirable for maintaining the purity of the rubber compound.
- Free Phenol Content (≤1.0%): A low free phenol content is important as excessive free phenols could adversely affect the properties of the rubber compound and its processing characteristics.
- Reinforcing Agent: The resin serves as a reinforcing agent for both natural rubber and various synthetic rubbers. This reinforcement enhances the hardness, tear resistance, wear resistance, strength, and elongation of the rubber compound.
- Plasticity during Processing: The resin exhibits good plasticity during processing, aiding in the dispersion of fillers within the rubber matrix. This is advantageous for achieving a uniform and well-dispersed mixture.
- Plasticization before Vulcanization: The resin can be plasticized before vulcanization, contributing to the overall processing characteristics of the rubber compound.
- Post-Vulcanization Improvement: After vulcanization, the resin continues to enhance the hardness, tear resistance, wear resistance, strength, and elongation of the rubber compound. It also slightly reduces elongation, prolongs scorch time, and reduces Mooney viscosity.
- Applications: The resin finds applications in the production of various rubber products, including tires, heels, soles, and conveyor belts. Its versatile characteristics make it suitable for a range of rubber formulations.
Major Applications
Industrial Rubber Parts:
Applied in the manufacturing of various industrial rubber components such as seals, gaskets, and other molded parts.
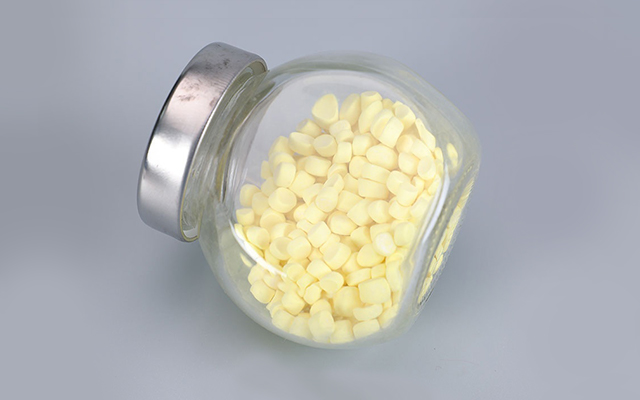
Automotive Components:
Used in the production of rubber components for automotive applications, where enhanced mechanical properties are required.
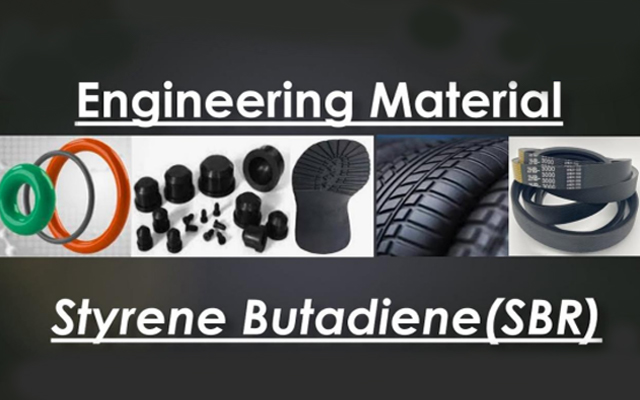
-
Package
Packed in a kraft paper composite bag lined with plastic bags, each net weight is 25kg.
-
Storage
Store indoors, dry and ventilated, anti-high temperature, fireproof, storage period is one year. Exceeding the storage period, it can still be used after passing the inspection.
In Needs of Rubber Vulcanization Accelerators Solution?
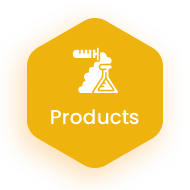
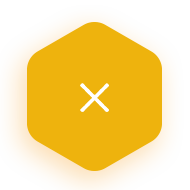