Optimal Heat Stabilizer for Plastisol Solutions
20/01/2024
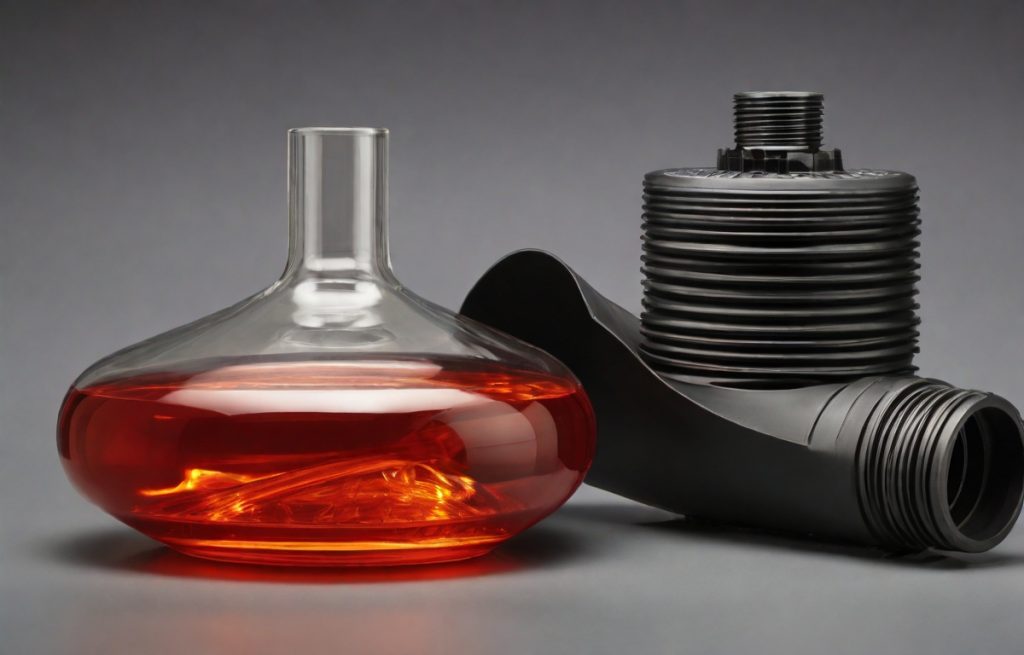
Plastisol, a commonly used ink in the textile and screen printing industries, offers many advantages, including versatility and durability. However, exposure to high temperatures can cause significant challenges for plastisol formulations, such as color fading and loss of print definition. That’s where a heat stabilizer for plastisol comes into play. In this article, we will discuss the importance of using an optimal heat stabilizer for plastisol formulations to enhance PVC formulations and ensure long-lasting print stability and quality. We will explore the different types of heat stabilizers available for plastisol, and provide guidance on selecting the right stabilizer for your needs. We’ll also cover best practices for incorporating heat stabilizers into plastisol ink formulations and discuss the latest advancements and innovations in this field. So, let’s get started to learn everything you need to know about heat stabilizers for plastisol.
Understanding Plastisol and its Challenges
Plastisol is a highly popular type of ink used in textile and screen printing industries due to its versatility and durability. It is a suspension of PVC particles in a liquid plasticizer, which turns solid when exposed to heat. However, this heat exposure can pose significant challenges to plastisol formulations, such as color fading and loss of print definition.
Reducing the effects of heat on plastisol is essential, and heat stabilizers for plastisol are the best solution to overcome these common issues. These stabilizers have unique properties that enhance PVC formulations while ensuring long-lasting print stability and quality, suitable for any plastisol formulation.
Role of Heat Stabilizers in Plastisol Print Stability
Heat stabilizers play a crucial role in maintaining the print stability of plastisol formulations. When plastisol inks are exposed to high temperatures, they can undergo degradation, leading to a loss of print definition and color fading.
Heat stabilizers work by preventing the degradation process and ensuring the ink remains stable under heat. They achieve this by neutralizing the free radicals that cause the degradation process, thereby protecting the ink from the negative effects of high temperatures.
Heat stabilizers also help to enhance the durability of printed designs and maintain the quality of the finished product. They do this by ensuring the ink remains intact and stable over time, even when subjected to harsh washing or environmental conditions.
Overall, incorporating an appropriate heat stabilizer into plastisol formulations can significantly enhance the performance and quality of the ink, leading to greater customer satisfaction and reduced product defects.
Types of Heat Stabilizers for Plastisol
Heat stabilizers are essential additives for enhancing the heat stability and durability of plastisol inks. There are various types of heat stabilizers available, each with unique properties and applications.
Lead-based Stabilizers
Lead-based stabilizers are a commonly used heat stabilizer for plastisol and PVC applications. They provide excellent heat stability performance, particularly in applications with high heat exposure. However, they are known to have environmental and health concerns, which has led to a decline in their usage over the years.
Tin-based Stabilizers
Tin-based stabilizers are an alternative to lead-based stabilizers, offering comparable heat stability performance but with lower environmental and health risks. They are also more cost-effective than lead-based stabilizers and have a wider compatibility range. Tin-based stabilizers are commonly used in applications that require high heat stability, such as automotive upholstery and industrial fabrics.
Cadmium-based Stabilizers
Cadmium-based stabilizers are another type of heat stabilizer suitable for plastic and PVC formulations. They offer excellent heat stability and durability but have become less popular due to environmental concerns, particularly related to cadmium toxicity. They are still used in applications where high-temperature exposure is a significant factor.
Zinc-based Stabilizers
Zinc-based stabilizers are an eco-friendly alternative to traditional stabilizers, providing excellent heat stability while reducing environmental and health risks. They are widely used in flexible PVC formulations, such as cables, wires, and medical devices, and offer long-term stability and durability while maintaining compatibility with other additives.
Calcium-based Stabilizers
Calcium-based stabilizers are primarily used in PVC applications and offer excellent thermal stability while being cost-effective and low-toxicity. They are ideal for wire and cable coatings, siding, and extruded profiles, where consistent heat stability and durability are essential.
When selecting a heat stabilizer for plastisol, consider the specific requirements of the application and the regulatory compliance criteria. Each heat stabilizer offers unique properties and benefits, and choosing the right one is crucial in ensuring long-lasting print stability and quality.
Factors to Consider When Choosing a Heat Stabilizer for Plastisol
When selecting a heat stabilizer for your plastisol ink formulation, several crucial factors need to be considered to ensure optimal print performance and longevity.
Compatibility with PVC and Other Additives
Ensure that the heat stabilizer is compatible with PVC and other additives present in the formulation to prevent adverse interactions that could affect print quality and stability.
Cost-Effectiveness
Select a heat stabilizer that balances cost-effectiveness and performance. Consider factors such as the amount of stabilizer required in the formulation and the overall production cost to make an informed decision.
Regulatory Compliance
Choose a heat stabilizer that is compliant with industry regulations and standards, such as REACH and RoHS, to ensure the safety and sustainability of your product.
Heat Stability Performance
Ensure that the heat stabilizer has optimal performance under high-temperature conditions, reducing the risk of print degradation, color fade, and other stability issues. Consider additional factors such as lightfastness and weatherability when selecting a heat stabilizer for outdoor applications.
By considering these key factors and selecting an appropriate heat stabilizer for your plastisol ink formulation, you can ensure that your prints maintain their quality, stability, and longevity, enhancing your customers’ satisfaction and growing your business.
Best Practices for Incorporating Heat Stabilizers in Plastisol Formulations
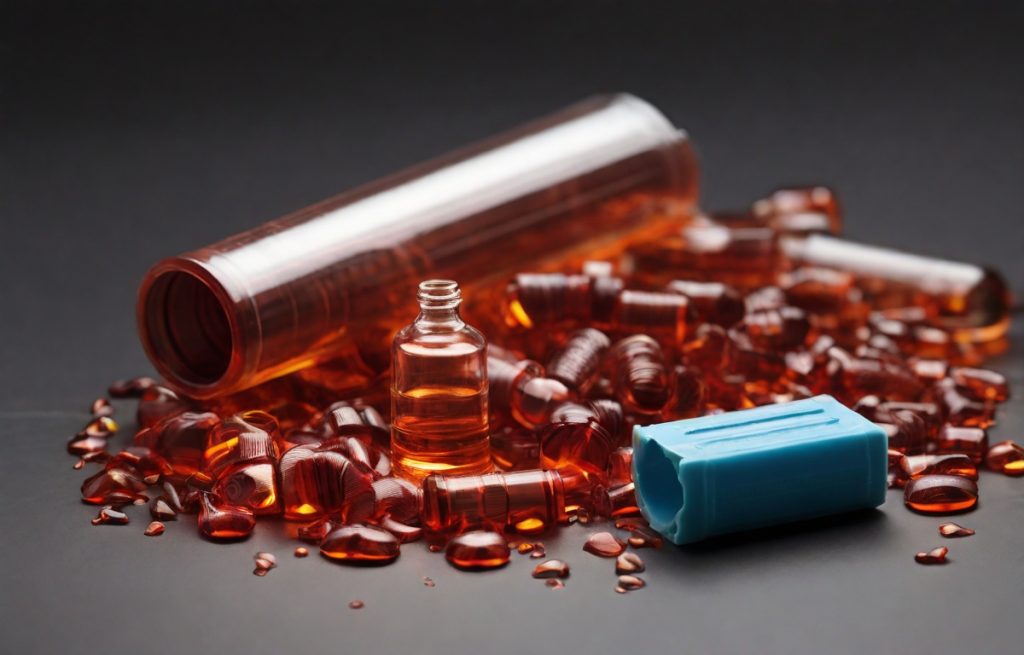
When incorporating heat stabilizers into plastisol ink formulations, it is essential to follow best practices to ensure optimal results. Here are some tips and recommendations:
Dosage Levels
Dosage levels of heat stabilizers should be carefully controlled to avoid over- or under-dosing. Over-dosing may impair the ink’s performance, while under-dosing may compromise its heat stability. Typically, the recommended dosage level is between 0.2 and 1.5 parts per hundred of resin (phr), depending on the type of stabilizer and the application requirements. It is advisable to refer to the manufacturer’s technical data sheet for specific dosage recommendations.
Mixing Techniques
The mixing technique used to incorporate the heat stabilizer into the plastisol solution is also critical for achieving optimal results. Typically, the heat stabilizer should be added to the resin before adding the plasticizer and other additives. This allows for proper dispersion and mixing of the heat stabilizer in the solution, ensuring uniformity and stability. Vigorous mixing and homogenization are recommended to ensure proper dispersion of the heat stabilizer throughout the formulation.
Compatibility Considerations
When selecting a heat stabilizer for use in plastisol formulations, it is crucial to consider its compatibility with other additives in the ink formulation. It is advisable to perform compatibility tests to assess whether the heat stabilizer interacts with other additives, such as pigments, plasticizers, or surfactants. Incompatibility may lead to precipitation, flocculation, or other unwanted effects that compromise the ink’s performance.
By following these best practices, printers can optimize the performance of heat-stabilized plastisol inks, resulting in long-lasting, high-quality prints that meet their clients’ expectations.
Testing and Quality Control for Heat Stabilized Plastisol
Testing and quality control are essential to ensure the effectiveness of heat stabilized plastisol formulations. Heat aging and color fastness evaluations are commonly used methods to validate the stability and durability of plastisol prints.
Heat aging tests simulate prolonged exposure to high temperatures and evaluate the impact on the plastisol ink. Through this testing method, manufacturers can determine the optimal dosage of heat stabilizer needed to ensure proper stability under various conditions.
Color fastness evaluations assess the ability of plastisol prints to retain their color and quality after multiple washings. This test helps manufacturers to confirm that the heat stabilizer used does not negatively impact the print quality or colorfastness.
Quality control measures should be implemented during each step of the production process to ensure that the final product meets the desired level of quality and performance. Regular monitoring and testing should be conducted to verify that the heat stabilized plastisol maintains stability and durability over time.
In summary, thorough testing and quality control measures ensure the effectiveness of heat stabilized plastisol formulations and guarantee long-lasting print stability and quality.
Advancements and Innovations in Heat Stabilizers for Plastisol
The demand for more sustainable and high-performing heat stabilizers for plastisol has led to various technological advancements in the field. Among the latest innovations are heat stabilizers that not only enhance print quality and color retention but also improve the durability and economic efficiency of plastisol formulations.
New Technologies for Enhanced Heat Stability
One of the recent developments is the use of advanced metal soaps, specifically calcium-based and zinc-based stabilizers. These new technologies offer excellent heat stability and UV resistance, making them ideal for outdoor applications. Innovative formulations also incorporate additives that enhance viscosity and adhesion, further improving print definition and durability.
Increased Sustainability through Bio-Based Additives
In response to the growing demand for eco-friendly alternatives, the market now offers heat stabilizers made from renewable and sustainable sources, such as soybean oil and other bio-based additives. These solutions provide excellent stabilization performance and reduce the carbon footprint of plastisol formulations.
Improved Cost-Effectiveness through Customized Formulations
To optimize the performance and economic efficiency of plastisol formulations, some manufacturers now offer customized heat stabilizer solutions that are tailored to meet specific requirements. These include stabilizer blends that balance heat stability performance, compatibility, and cost, resulting in more efficient and cost-effective formulations.
Summary
As the market for heat stabilizers for plastisol continues to expand, it is important to stay updated on the latest innovations and advancements. With new technologies, sustainable additives, and customized formulations, manufacturers can now achieve improved print quality, durability, and economic efficiency with their plastisol solutions.
Conclusion
In conclusion, the use of an optimal heat stabilizer for plastisol is crucial for achieving print stability and durability. Without proper stabilization, plastisol ink formulations can experience color fading and loss of print definition, leading to unsatisfactory results.
By incorporating a high-quality plastisol stabilizer for printing, you can ensure that your PVC formulations remain stable when exposed to high temperatures, maintaining the quality and longevity of your prints. When selecting a heat stabilizer for plastisol, it is essential to consider factors such as compatibility, cost-effectiveness, regulatory compliance, and performance.
Lastly, advancements and innovations in the field of heat stabilizers for plastisol are continually evolving, offering improved stability, enhanced print quality, and increased sustainability. By staying up-to-date with the latest developments, you can ensure that your plastisol formulations remain competitive and effective in the ever-changing printing industry.
FAQ
What is a heat stabilizer for plastisol?
A heat stabilizer for plastisol is an additive that is used to enhance the heat stability of PVC-based plastisol formulations. It helps to prevent degradation and maintain the integrity and quality of the prints when exposed to high temperatures during the curing process.
Why is a heat stabilizer important for PVC and plastic printing?
Heat stabilizers are crucial for PVC and plastic printing because they help to prevent color fading, loss of print definition, and other forms of degradation that can occur when plastisol formulations are exposed to elevated temperatures. They ensure the durability and longevity of prints on various substrates.
How does a heat stabilizer work in plastisol ink?
A heat stabilizer works in plastisol ink by providing thermal stability to the formulation. It forms a protective shield around the PVC resin particles, preventing them from undergoing chemical reactions that can lead to degradation under heat. This ensures that the ink maintains its color vibrancy and print definition during the curing process.
What are the different types of heat stabilizers for plastisol?
There are various types of heat stabilizers available for plastisol formulations, including metal soaps, organotin compounds, and mixed metal stabilizers. Each type has its unique properties and benefits, and the choice depends on the specific application, regulatory compliance requirements, and performance expectations.
What factors should be considered when selecting a heat stabilizer for plastisol?
When choosing a heat stabilizer for plastisol, important factors to consider include compatibility with PVC and other additives, cost-effectiveness, regulatory compliance, heat stability performance, and desired print quality. It is crucial to select a stabilizer that meets the specific needs of the application while ensuring long-term stability.
What are the best practices for incorporating heat stabilizers in plastisol ink formulations?
To effectively incorporate heat stabilizers in plastisol ink formulations, it is essential to consider factors such as the appropriate dosage levels, mixing techniques, and compatibility with other additives. It is recommended to follow the manufacturer’s guidelines and conduct compatibility tests to ensure optimal performance and print stability.
How can the quality of heat stabilized plastisol prints be ensured?
To ensure the quality of heat stabilized plastisol prints, it is essential to conduct thorough testing and quality control. Methods such as heat aging tests and color fastness evaluations can be used to assess the stability and durability of the prints. Regular quality control checks help maintain consistent and long-lasting print performance.
What are the advancements and innovations in heat stabilizers for plastisol?
The field of heat stabilizers for plastisol is constantly evolving, with advancements and innovations aimed at improving heat stability, print quality, and sustainability. New technologies and formulations are being developed to enhance the performance of heat stabilizers, ensuring more efficient and eco-friendly plastisol printing.
Why is it important to use a plastisol stabilizer for printing?
Using a plastisol stabilizer for printing is crucial because it ensures the longevity and durability of prints. Plastisol stabilizers help to maintain print stability, prevent color fading and degradation, and increase the resistance of the prints to various environmental factors. They contribute to achieving high-quality and long-lasting results.