Exploring Versatility of Oil Resistant Synthetic Rubber in Industries
16/07/2024
Oil resistant synthetic rubber is a specialized elastomer engineered to withstand exposure to oils, fuels, and chemicals without compromising its mechanical integrity. It is formulated through precise polymerization processes that combine various monomers to achieve specific properties such as resilience, flexibility, and durability in challenging industrial environments.
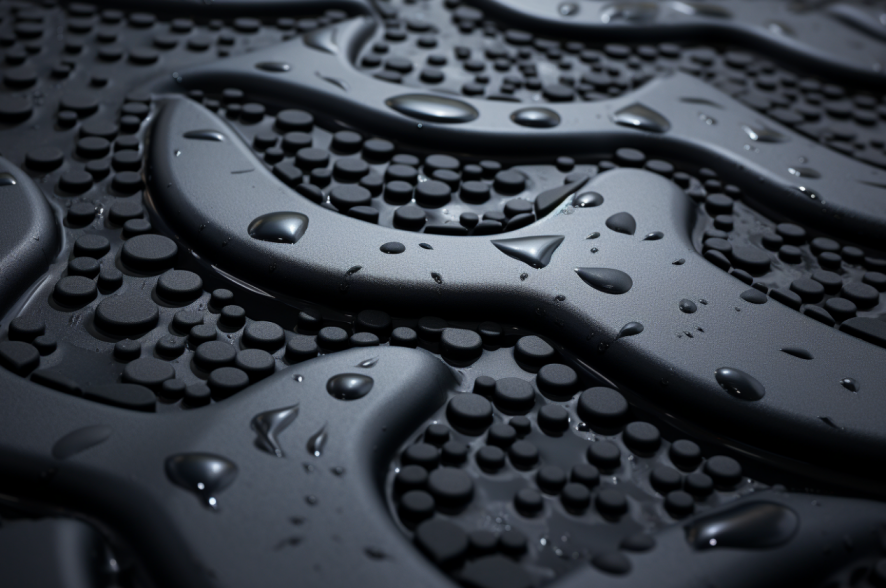
This synthetic material plays a crucial role in applications across automotive, manufacturing, aerospace, and consumer goods sectors where resistance to oil degradation is essential for prolonged operational reliability and performance. As industries continue to demand materials that can withstand harsh conditions and environmental stresses, the development and application of oil-resistant synthetic rubber remain pivotal in advancing technological solutions and ensuring product longevity.
What is Oil Resistant Synthetic Rubber
Oil resistant synthetic rubber refers to a specialized type of synthetic elastomer designed to withstand exposure to oils, fuels, and greases without deteriorating. This unique property makes it invaluable in a wide range of industrial applications where contact with oils is common. From the automotive to manufacturing sectors, oil-resistant synthetic rubber plays a crucial role in enhancing product durability and performance.
Importance and Applications in Various Industries
The significance of oil resistant synthetic rubber lies in its ability to maintain elasticity and mechanical strength when exposed to oils and other hydrocarbons. This characteristic makes it ideal for applications such as seals, gaskets, hoses, and various components where resistance to oil degradation is critical. Industries such as automotive, aerospace, oil and gas, and manufacturing heavily rely on these materials to ensure operational efficiency and longevity of their products.
Types and Composition
Oil resistant synthetic rubber comes in several types, each tailored to specific applications and environmental conditions:
Nitrile Rubber (NBR) Nitrile rubber is a copolymer of butadiene and acrylonitrile, renowned for its excellent resistance to oils, fuels, and chemicals. It exhibits good mechanical properties and flexibility over a wide temperature range, making it suitable for seals and fuel hoses in automotive and aerospace industries.
Neoprene (CR) Neoprene is a versatile synthetic rubber known for its resistance to oil, ozone, heat, and weathering. It is commonly used in gaskets, conveyor belts, and automotive components where moderate oil resistance combined with durability is required.
Ethylene Propylene Diene Monomer (EPDM) EPDM rubber offers excellent resistance to weathering, ozone, and aging, in addition to good oil resistance. It finds applications in automotive weather seals, roofing membranes, and electrical insulation where exposure to oils is prevalent alongside other environmental factors.
Chemical Composition and Properties of Each Type
Each type of oil-resistant synthetic rubber possesses distinct chemical compositions that contribute to its specific properties. For example, Nitrile rubber’s resistance to oils stems from its high acrylonitrile content, which reduces swell and degradation in oil environments. Neoprene derives its oil resistance from its saturated polymer backbone, providing stability against hydrocarbon exposure. EPDM’s resistance to oils and environmental factors arises from its ethylene and propylene monomer units, imparting durability and flexibility.
Manufacturing Process
The manufacturing process of oil-resistant synthetic rubber involves several key steps to achieve the desired chemical composition and physical properties:
Polymerization The process begins with the polymerization of monomers such as butadiene, acrylonitrile, chloroprene, ethylene, and propylene. These monomers undergo chemical reactions to form the polymer chains that constitute the base material of synthetic rubber.
Compounding Compounding involves mixing the polymer with various additives such as fillers, plasticizers, curing agents, and antioxidants. These additives enhance specific properties like oil resistance, elasticity, and heat resistance according to the intended application.
Processing The compounded rubber is then processed using techniques such as extrusion, calendering, or molding to form the desired shapes and dimensions. This step ensures uniformity and consistency in the final product’s physical properties.
Applications and Industries
Oil-resistant synthetic rubber manufactured by CHEMBROAD finds extensive applications across various industries due to its durability and resilience in oil-rich environments.
Automotive Industry In the automotive sector, oil-resistant synthetic rubber plays a critical role in seals, gaskets, and O-rings. These components are exposed to engine oils, transmission fluids, and fuels. By maintaining elasticity and sealing integrity over prolonged use, synthetic rubber helps enhance engine efficiency and reliability. Moreover, it contributes to reducing maintenance costs by minimizing leaks and ensuring consistent performance.
Manufacturing Sector Within manufacturing, oil-resistant synthetic rubber is utilized in the production of hoses and belts. These components are essential for conveying fluids and materials in industrial machinery. The rubber’s resistance to oils and chemicals ensures longevity and operational reliability, making it suitable for applications where exposure to lubricants and hydraulic fluids is frequent.
Other Industries Beyond automotive and manufacturing, synthetic rubber finds applications in marine environments, construction materials, and consumer goods. Its ability to withstand oil exposure makes it suitable for seals in marine engines, waterproofing membranes in construction, and various consumer products requiring durability and flexibility in oil-prone settings.
Benefits of Using Oil-Resistant Synthetic Rubber
The adoption of oil-resistant synthetic rubber offers several advantages across different sectors:
Enhanced Durability: Synthetic rubber has better resistance to oil, chemicals and environmental factors than natural rubber. Thereby extending the service life of the product.
Improved Performance: Components made from synthetic rubber maintain their integrity and functionality even under challenging conditions, ensuring reliable operation and reduced downtime.
Cost Efficiency: By minimizing maintenance requirements and replacement cycles. Synthetic rubber contributes to long-term cost savings, making it an affordable choice for industrial applications.
Advantages and Challenges
Oil-resistant synthetic rubber offers distinct advantages over natural rubber and other materials:
Superior Oil Resistance: Synthetic rubber formulations can be tailored to achieve specific levels of oil resistance, surpassing the capabilities of natural rubber.
Wide Temperature Range: Synthetic rubber maintains flexibility and performance across a broader temperature spectrum compared to many other elastomers.
Challenges: Despite its benefits, challenges such as higher manufacturing costs, environmental impact during production, and disposal issues remain. Addressing these challenges requires ongoing research into sustainable manufacturing practices and recyclable materials.
Future Trends and Innovations
Innovations in the development of oil-resistant synthetic rubber are shaping future trends in the industry:
Advanced Formulations: Research focuses on developing new formulations with enhanced properties. These include greater oil resistance, better sustainability and compatibility with modern manufacturing processes.
Bio-Based Materials: Exploration of bio-based feedstocks and renewable resources for synthetic rubber production aims to reduce dependence on petrochemicals and mitigate environmental impacts.
Smart Materials: Integrate smart technologies such as self-healing and sensor functions into synthetic rubber products. To enhance performance monitoring and durability in real-time applications.
Conclusion
Oil resistant synthetic rubber, exemplified by types like Nitrile rubber, Neoprene, and EPDM, plays a vital role in modern industrial applications where resilience against oils and chemicals is essential. Through careful formulation and precise manufacturing processes. These materials provide durability, reliability and performance to the automotive, manufacturing, aerospace and other industries. As the industry continues to develop, innovation in synthetic rubber technology will continue to advance. Ensuring increased durability and performance in challenging operating environments.