NBR Synthetic Rubber: Properties and Applications
19/01/2024
Nitrile Butadiene Rubber (NBR) is a synthetic rubber that is widely used in various industrial applications due to its unique properties. NBR is a copolymer of acrylonitrile and butadiene, which makes it resistant to oil, fuel, and other chemicals. This rubber is also known as Buna-N, Perbunan, Nipol, Krynac, and Europrene.
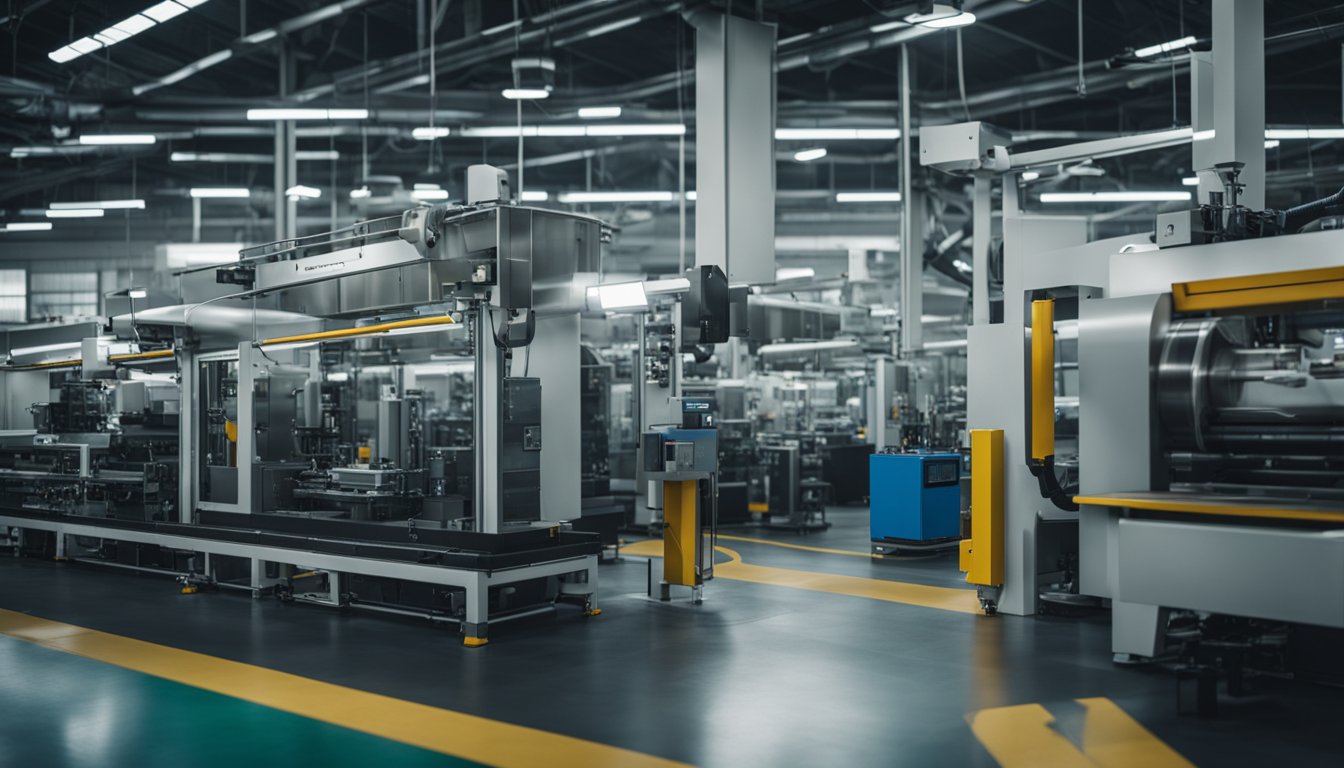
NBR has a high resistance to heat and abrasion, making it ideal for use in automotive and industrial applications. It is commonly used in the production of fuel hoses, gaskets, rollers, and other products that require oil resistance. Moreover, NBR is also used in the production of seals, o-rings, and other components that require resistance to chemicals and solvents.
NBR is a versatile rubber that finds its application in various industries such as automotive, aerospace, and oil and gas. Its unique properties make it an ideal choice for applications that require resistance to oil, fuel, and chemicals. In the following sections, we will explore the properties, applications, and uses of NBR in detail.
Overview of NBR Synthetic Rubber
NBR synthetic rubber, also known as nitrile rubber, is a type of synthetic elastomer with excellent resistance to oil, fuel, and chemicals. It is a copolymer of acrylonitrile and butadiene, and is produced by emulsifying the two monomers in water and then polymerizing them. The resulting polymer has a high level of oil resistance due to its polar nitrile groups, which interact with nonpolar substances like oil.
NBR is commonly used in the automotive, aerospace, and industrial sectors due to its excellent resistance to oil and fuel. It is often used to make seals, gaskets, hoses, and other components that require good resistance to oil and fuel. In addition, NBR is resistant to a wide range of chemicals, including acids, bases, and solvents, making it suitable for use in harsh chemical environments.
NBR is available in a range of grades with varying levels of acrylonitrile content, which affects its physical properties. Higher acrylonitrile content leads to higher oil resistance, but lower low-temperature flexibility. NBR with low acrylonitrile content is more flexible at low temperatures, but has lower oil resistance.
NBR can also be blended with other elastomers to achieve a balance of properties. For example, blending NBR with hydrogenated nitrile rubber (HNBR) can improve its resistance to heat and ozone.
Overall, NBR synthetic rubber is a versatile material with excellent resistance to oil, fuel, and chemicals. Its properties can be tailored to suit specific applications, making it a popular choice in many industries.
Production Process of NBR
Nitrile Butadiene Rubber (NBR) is a synthetic rubber derived from the copolymerization of acrylonitrile (ACN) and butadiene (BD). It is a type of elastomer that is known for its excellent resistance to oil, fuel, and other chemicals. The production of NBR involves several steps, including polymerization, catalysts and control chemicals, and post-polymerization processing.
Polymerization Methods
NBR is produced through emulsion, solution, and hot rubber methods. The emulsion polymerization method is the most commonly used method for producing NBR. In this method, ACN and BD are dispersed in water with the help of an emulsifier. The emulsifier forms micelles around the monomers, which allows them to be evenly dispersed in the water. Radical initiators are then added to the mixture to start the polymerization process. The polymerization reaction takes place in a reactor vessel at a controlled temperature and pressure.
Catalysts and Control Chemicals
Catalysts and control chemicals are added to the polymerization mixture to control the molecular weight and properties of the resulting polymer. The most commonly used catalysts for NBR production are organic peroxides, which initiate the polymerization reaction. Control chemicals are added to regulate the reaction rate, prevent premature termination, and control the molecular weight of the polymer. The most commonly used control chemicals for NBR production are mercaptans, which act as chain transfer agents.
Post-Polymerization Processing
After the polymerization reaction is complete, the resulting NBR latex is coagulated to separate the rubber from the water. The coagulated rubber is washed, dried, and then compounded with various additives to improve its properties. The compounding process involves mixing the NBR rubber with fillers, plasticizers, curing agents, and other additives to achieve the desired properties. The resulting NBR compound can then be molded or extruded into various shapes and forms.
In summary, the production process of NBR involves emulsion polymerization, the use of organic peroxides as catalysts, and the addition of mercaptans as control chemicals. The resulting NBR latex is coagulated, washed, dried, and compounded with various additives to improve its properties. The resulting NBR compound can be molded or extruded into various shapes and forms.
Properties of NBR
Physical Properties
Nitrile rubber (NBR) is a synthetic rubber derived from acrylonitrile (ACN) and butadiene. It is a copolymer of these two monomers. NBR has excellent physical properties, including high tensile strength, good resistance to abrasion, and low compression set. It is also resistant to oil, fuel, and other chemicals, making it suitable for use in a wide range of applications.
NBR is a highly elastic material, and it can be easily molded into different shapes and sizes. It has a low glass transition temperature, which means that it remains flexible and resilient even at low temperatures. This property makes it an ideal material for use in seals, gaskets, and other applications that require good low-temperature performance.
Chemical Resistance
NBR is resistant to a wide range of chemicals, including oils, fuels, and solvents. It is also resistant to acids, alkalis, and other chemicals, making it suitable for use in harsh environments. NBR is particularly well-suited for use in applications that involve contact with hydrocarbons, such as oil and gas production.
Thermal Stability
NBR has good thermal stability, and it can withstand temperatures ranging from -40°C to 120°C. It is also resistant to oxidation and ozone, which makes it suitable for use in outdoor applications. NBR is an excellent choice for use in applications that require good thermal stability and resistance to environmental factors.
In summary, NBR is a versatile synthetic rubber with excellent physical properties, chemical resistance, and thermal stability. It is widely used in a variety of applications, including seals, gaskets, hoses, and other products that require good resistance to oil, fuel, and other chemicals.
Applications of NBR
Nitrile Butadiene Rubber (NBR) is a synthetic rubber that has a wide range of applications across various industries. Its unique properties, such as oil resistance, chemical resistance, and high-temperature stability, make it a popular choice for many applications. In this section, we will explore some of the most common applications of NBR.
Automotive Industry
NBR is widely used in the automotive industry for various applications due to its excellent oil resistance. It is used in the production of gaskets, o-rings, seals, hoses, and other parts that come into contact with oil and fuel. NBR’s ability to withstand high temperatures and harsh chemicals makes it an ideal material for use in automotive manufacturing.
Oil and Gas Industry
NBR is also commonly used in the oil and gas industry due to its excellent resistance to oil and other hydrocarbons. It is used in the production of seals, gaskets, and hoses that come into contact with oil and fuel. NBR’s resistance to chemicals and high temperatures makes it a reliable choice for use in the oil and gas industry.
Consumer Goods
NBR is also used in the production of consumer goods such as gloves, footwear, and other products that require resistance to oil and chemicals. It is also used in the production of adhesives, coatings, and other materials that require high-temperature stability.
In conclusion, NBR is a versatile synthetic rubber with a wide range of applications across various industries. Its unique properties make it a reliable choice for use in automotive, oil and gas, and consumer goods manufacturing.
Market Trends and Demand
Nitrile Butadiene Rubber (NBR) is a synthetic rubber that is widely used in various industries such as automotive, construction, and oil & gas. The global NBR market is expected to grow at a CAGR of 3.82% during the forecast period (2024-2029) and reach a volume of 1.37 million tons by 2029 [1]. The significant factors driving the market include the growing usage in the transportation industry and increasing industrial activities.
The automotive industry is the largest consumer of NBR, accounting for around 50% of the global demand. NBR is used in the production of various automotive parts such as hoses, seals, gaskets, and O-rings due to its excellent oil resistance, high tensile strength, and good abrasion resistance. The increasing demand for automobiles in emerging economies such as China and India is expected to boost the demand for NBR in the automotive industry [1].
Apart from the automotive industry, the construction industry is another major consumer of NBR. NBR is used in the production of various construction materials such as roofing membranes, sealants, and adhesives due to its excellent weather resistance, durability, and flexibility. The increasing demand for construction materials in developing countries such as Brazil and South Africa is expected to drive the demand for NBR in the construction industry [2].
Furthermore, the oil & gas industry is also a significant consumer of NBR. NBR is used in the production of various oilfield equipment such as seals, gaskets, and hoses due to its excellent oil and chemical resistance. The increasing exploration and production activities in the oil & gas industry are expected to boost the demand for NBR in the coming years [3].
Overall, the NBR market is expected to witness steady growth in the coming years due to the increasing demand from various end-use industries.
Environmental Impact and Sustainability
Recycling and Waste Management
Nitrile Butadiene Rubber (NBR) is a synthetic rubber that has become increasingly popular in recent years due to its excellent resistance to oils, chemicals, and abrasion. However, the production of NBR rubber has a significant environmental impact due to the use of petrochemicals and the release of greenhouse gases during manufacturing.
One way to mitigate the environmental impact of NBR rubber is through recycling and waste management. NBR rubber can be recycled and used in a variety of applications such as playground surfaces, athletic tracks, and industrial flooring. Recycling NBR rubber helps to reduce the amount of waste sent to landfills and conserves natural resources.
Regulations and Compliance
In recent years, there has been an increased focus on the environmental impact of synthetic rubber production. Governments and regulatory bodies around the world have implemented regulations and compliance measures to reduce the environmental impact of NBR rubber production.
For instance, the European Union has implemented the Registration, Evaluation, Authorization, and Restriction of Chemicals (REACH) regulation, which aims to protect human health and the environment from the risks posed by chemicals. The REACH regulation requires manufacturers to register their products and provide information on the chemicals used in the production process.
Similarly, the United States Environmental Protection Agency (EPA) has implemented regulations to reduce the environmental impact of synthetic rubber production. The EPA requires manufacturers to report their greenhouse gas emissions and implement measures to reduce their environmental impact.
Overall, recycling and waste management, as well as regulations and compliance measures, can help to reduce the environmental impact of NBR rubber production.
Future Developments in NBR Technology
Nitrile butadiene rubber (NBR) is a synthetic rubber that has been used in various applications for over 40 years. It is known for its excellent resistance to oils, greases, and liquid fuels, making it a popular choice for industries such as automotive, aerospace, and oil and gas. However, as technology advances and demands change, the future of NBR technology is also evolving.
One of the future developments in NBR technology is the use of new raw materials. Researchers are exploring the use of bio-based raw materials, such as vegetable oils, to produce NBR. This approach not only reduces the dependence on petroleum-based raw materials but also improves the sustainability of the NBR production process.
Another area of development is the improvement of NBR properties. Researchers are working on developing NBR grades with improved low-temperature flexibility, higher-temperature resistance, and better mechanical properties. These properties will make NBR more versatile and enable its use in a wider range of applications.
In addition to improving NBR properties, researchers are also exploring the use of NBR in new applications. For example, NBR is being tested as a material for fuel cell membranes due to its excellent resistance to fuel and high-temperature stability. Its use in this application could significantly improve the performance and durability of fuel cells.
Overall, the future of NBR technology is promising. With the development of new raw materials, improved properties, and new applications, NBR will continue to be a vital material in various industries.