MBTs in Rubber Compounding: Understanding Their Role and Benefits
19/01/2024
Rubber compounding is a complex process that involves the use of various chemicals to achieve desired properties in the final product. One important aspect of this process is the use of MBTs, or mercaptobenzothiazoles, which are commonly used as accelerators in rubber compounding. MBTs are a class of organic compounds that contain sulfur and nitrogen atoms, and are known for their ability to promote the vulcanization of rubber.
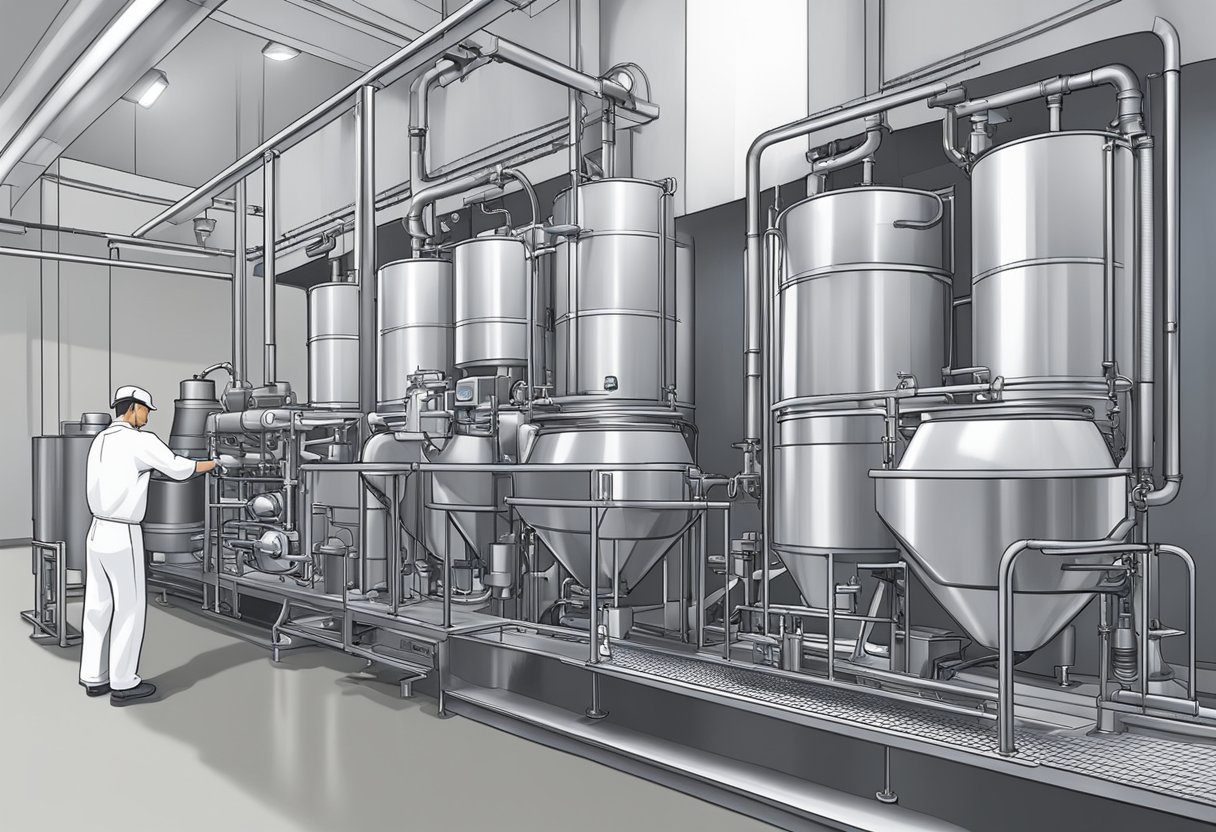
MBTs have been widely used in rubber compounding for several decades, and have proven to be effective accelerators for a wide range of rubber formulations. They are particularly useful in the production of tire compounds, where they help to improve the curing rate and physical properties of the final product. However, the use of MBTs in rubber compounding is not without its challenges, and there are several factors that must be considered in order to achieve optimal results.
Fundamentals of MBTS in Rubber Compounding
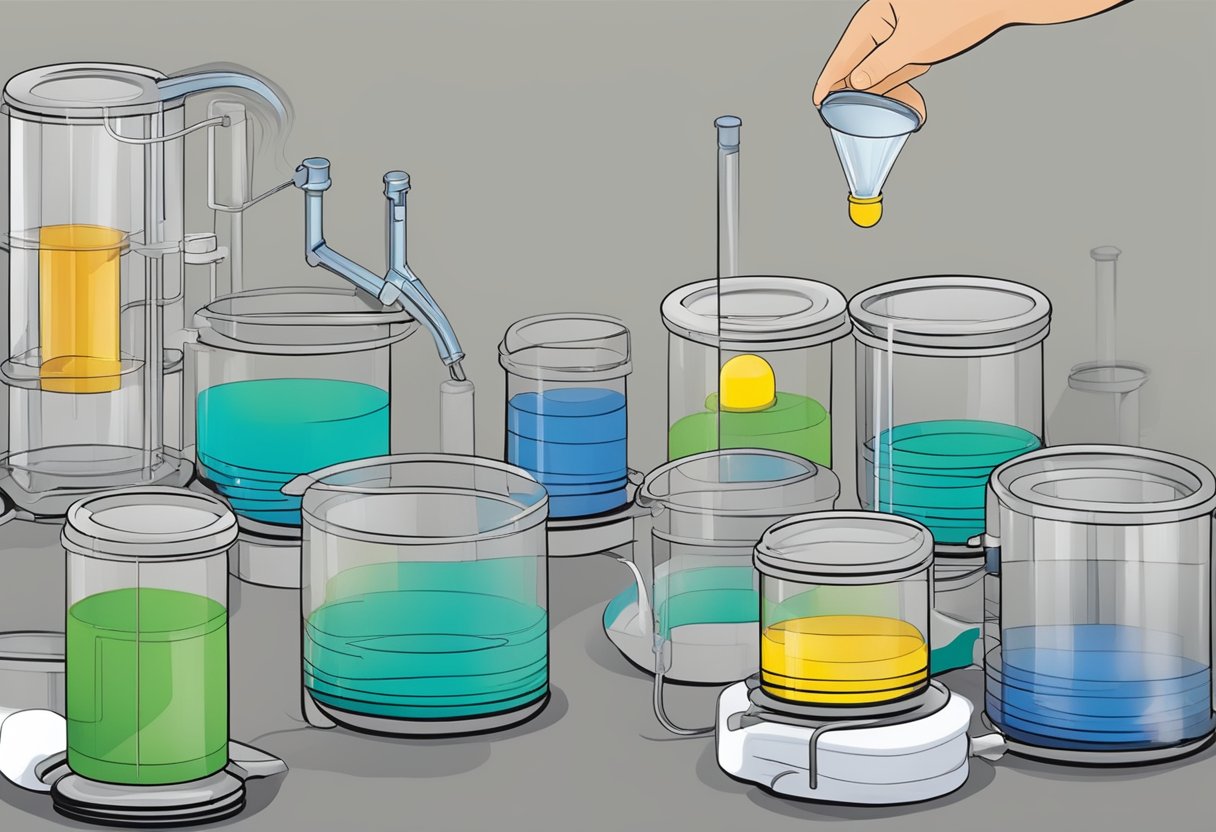
MBTS (2,2′-Dithiobis(benzothiazole)) is a commonly used accelerator in rubber compounding. It belongs to the family of thiazole accelerators and is known for its ability to promote vulcanization at lower temperatures.
MBTS works by reacting with the sulfur in the rubber compound to form a cross-link, which strengthens the rubber and improves its mechanical properties. It is particularly effective in promoting the curing of natural rubber, styrene-butadiene rubber (SBR), and nitrile rubber (NBR).
One of the advantages of using MBTS is its fast curing rate, which allows for shorter processing times and higher production rates. However, excessive use of MBTS can lead to scorching, which is the premature vulcanization of the rubber compound. To avoid scorching, it is recommended to use MBTS in combination with other accelerators such as CBS (N-cyclohexyl-2-benzothiazole sulfenamide) or TBBS (N-tert-butyl-2-benzothiazolesulfenamide).
In addition to its use as an accelerator, MBTS also has anti-aging properties, which help to extend the life of the rubber product. It achieves this by inhibiting the oxidation of the rubber, which can lead to cracking and degradation.
Overall, MBTS is a versatile accelerator that is widely used in the rubber industry. Its ability to promote vulcanization at lower temperatures and fast curing rate make it a valuable addition to rubber compounds. However, care must be taken to avoid excessive use, which can lead to scorching.
Chemical Properties of MBTS
Accelerator Activity
MBTS, also known as 2,2′-dibenzothiazyl disulfide, is a widely used accelerator in rubber compounding. It is known for its fast curing speed and high efficiency in promoting vulcanization. MBTS is often used in combination with other accelerators, such as CBS and TMTD, to achieve optimal curing properties.
Aging Resistance
MBTS has good aging resistance properties, which makes it suitable for use in rubber products that are exposed to heat and light for extended periods. It helps to prevent the degradation of rubber materials and maintains their physical properties over time.
Vulcanization Characteristics
MBTS is a sulfur-based accelerator that promotes cross-linking between rubber molecules during vulcanization. It works by reacting with the sulfur atoms in the rubber chain, forming a three-dimensional network that gives the rubber its strength and elasticity. MBTS is particularly effective in promoting the vulcanization of natural rubber and SBR.
Overall, MBTS is a versatile accelerator that offers a range of benefits in rubber compounding. Its fast curing speed, high efficiency, and good aging resistance make it a popular choice among rubber manufacturers.
MBTS Incorporation Methods
MBTS (2,2′-dibenzothiazyl disulfide) is a widely used accelerator in rubber compounding due to its high efficiency and fast curing rates. There are several methods for incorporating MBTS into rubber compounds, each with its own advantages and disadvantages.
Mechanical Mixing
Mechanical mixing is a common method for incorporating MBTS into rubber compounds. This method involves mixing the MBTS with the rubber and other ingredients using a mechanical mixer. The mixing time and temperature are critical factors in ensuring proper incorporation of MBTS into the rubber. Over-mixing can lead to degradation of the rubber, while under-mixing can result in poor dispersion of MBTS, leading to uneven curing rates.
Latex Compounding
Latex compounding is another method for incorporating MBTS into rubber compounds. This method involves adding MBTS to a latex solution, which is then mixed with the rubber and other ingredients. Latex compounding offers several advantages, such as improved dispersion of MBTS and reduced mixing time. However, this method requires specialized equipment and is not suitable for all types of rubber compounds.
Solution Blending
Solution blending is a method for incorporating MBTS into rubber compounds that involves dissolving MBTS in a solvent and then blending the solution with the rubber and other ingredients. This method offers several advantages, such as improved dispersion of MBTS and reduced mixing time. However, it requires specialized equipment and can be more expensive than other methods.
Overall, the choice of MBTS incorporation method depends on several factors, including the type of rubber compound, the desired curing rate, and the available equipment. Rubber compounders should carefully evaluate each method to determine the most appropriate method for their specific application.
Effects of MBTS on Rubber Properties
MBTS, or 2,2′-dibenzothiazole disulfide, is a widely used accelerator in rubber compounding. It is known to have a significant impact on the properties of the rubber, particularly in terms of elasticity, strength, abrasion resistance, and compression set.
Elasticity and Strength
MBTS is highly effective in improving the elasticity and strength of rubber compounds. It acts by promoting the cross-linking of rubber molecules, which results in an increase in the number of cross-links and a reduction in the free chains. This, in turn, leads to improved tensile strength, tear resistance, and elongation at break.
Abrasion Resistance
MBTS is also known to improve the abrasion resistance of rubber compounds. This is due to the fact that the cross-linking promoted by MBTS results in a tighter network of rubber molecules, which makes the rubber more resistant to wear and tear.
Compression Set
MBTS can also have an impact on the compression set of rubber compounds. Compression set is a measure of the ability of rubber to recover its original shape after being compressed. MBTS can help to improve the compression set of rubber compounds by promoting the cross-linking of rubber molecules, which results in a more stable and resilient rubber network.
In conclusion, MBTS is a highly effective accelerator in rubber compounding, with a significant impact on the properties of the rubber. It can improve the elasticity, strength, abrasion resistance, and compression set of rubber compounds, making it an essential component in many rubber formulations.
MBTS and Compound Formulation
Filler Interaction
MBTS is commonly used as a primary accelerator in rubber compounding due to its ability to improve the curing process. However, the interaction between MBTS and fillers used in the compound can affect the curing characteristics of the rubber. The presence of certain fillers can significantly reduce the effectiveness of MBTS, leading to slower curing rates and weaker mechanical properties.
To optimize the use of MBTS in rubber compounds, it is important to consider the type and amount of filler used in the formulation. Careful selection of fillers and their respective loading levels can help improve the interaction between MBTS and the fillers, leading to better curing characteristics and improved overall performance of the rubber compound.
Plasticizer Compatibility
MBTS can also interact with plasticizers used in rubber compounding, affecting the curing characteristics and mechanical properties of the rubber. Some plasticizers can inhibit the curing process, leading to slower curing rates and weaker mechanical properties.
To optimize the use of MBTS in rubber compounds, it is important to consider the type and amount of plasticizer used in the formulation. Careful selection of plasticizers and their respective loading levels can help improve the interaction between MBTS and the plasticizers, leading to better curing characteristics and improved overall performance of the rubber compound.
Cure System Optimization
MBTS is often used in combination with other accelerators and sulfur in rubber compounding to form a cure system. The effectiveness of the cure system depends on the type and amount of accelerators and sulfur used, as well as their respective ratios.
Optimizing the cure system is crucial to achieving the desired curing characteristics and mechanical properties of the rubber compound. The use of MBTS in combination with other accelerators and sulfur can improve the curing process and lead to better mechanical properties. However, careful consideration of the type and amount of accelerators and sulfur used, as well as their respective ratios, is necessary to achieve optimal results.
Processing Techniques for MBTS Compounds
Milling
Milling is a common processing technique used for MBTS compounds. The process involves the use of a two-roll mill or an internal mixer to mix the ingredients. During the milling process, the MBTS is added to the rubber compound and mixed thoroughly. The milling process helps to disperse the MBTS evenly throughout the compound, which improves the curing process and the overall performance of the compound.
Extrusion
Extrusion is another processing technique used for MBTS compounds. The process involves the use of an extruder to mix the ingredients. During the extrusion process, the MBTS is added to the rubber compound and mixed thoroughly. The extrusion process helps to disperse the MBTS evenly throughout the compound, which improves the curing process and the overall performance of the compound.
Molding
Molding is a common processing technique used for MBTS compounds. The process involves the use of a mold to shape the compound into the desired shape. During the molding process, the MBTS is added to the rubber compound and mixed thoroughly. The molding process helps to disperse the MBTS evenly throughout the compound, which improves the curing process and the overall performance of the compound.
In conclusion, MBTS is an important ingredient in rubber compounding that helps to improve the curing process and the overall performance of the compound. The processing techniques discussed above are commonly used to mix MBTS into rubber compounds and ensure that it is evenly dispersed throughout the compound. By using these techniques, manufacturers can produce high-quality rubber products with consistent performance.
Environmental and Safety Considerations
Handling and Storage
When handling MBTs in rubber compounding, it is important to take proper safety precautions. MBTs are known to be toxic and can cause skin and eye irritation, as well as respiratory issues if inhaled. Therefore, it is recommended to wear protective clothing, gloves, and eye protection when handling MBTs.
In addition, it is important to store MBTs in a cool, dry place away from direct sunlight and sources of heat. This will help to prevent the MBTs from degrading and potentially releasing harmful fumes.
Disposal and Recycling
MBTs are not biodegradable, and improper disposal can lead to environmental contamination. Therefore, it is important to dispose of MBTs in accordance with local regulations and guidelines. This may include recycling, incineration, or other methods of safe disposal.
Recycling is a preferred method of disposal for MBTs, as it can help to reduce waste and conserve resources. However, it is important to ensure that the recycling process is done in a safe and environmentally responsible manner.
Overall, proper handling, storage, and disposal of MBTs in rubber compounding is crucial for both environmental and safety considerations. By taking these precautions, the risks associated with MBTs can be minimized, and the benefits of using these compounds can be maximized.
Case Studies and Applications
Automotive Industry
In the automotive industry, MBTs (mercaptobenzothiazoles) are widely used in rubber compounding due to their excellent vulcanization properties. They are commonly used as accelerators in the production of tires, hoses, and other rubber components. MBTs play a crucial role in improving the physical properties of rubber, such as tensile strength, elongation, and abrasion resistance.
One of the case studies involving MBTs in the automotive industry is the use of 2-MBT (2-mercaptobenzothiazole) in tire production. The addition of 2-MBT to the rubber compound improves the curing rate of the rubber, resulting in better processing and faster production times. Additionally, 2-MBT also enhances the tire’s durability and resistance to heat and wear, leading to an extended lifespan.
Consumer Products
MBTs are also commonly used in the production of consumer products such as footwear, toys, and sporting goods. The addition of MBTs to rubber compounds improves the physical properties of these products, making them more durable and long-lasting.
One of the case studies involving MBTs in consumer products is the use of ZMBT (zinc 2-mercaptobenzothiazole) in the production of rubber soles for footwear. ZMBT improves the curing rate of the rubber, resulting in faster production times. Additionally, ZMBT enhances the rubber’s adhesion to various surfaces, making it more slip-resistant and providing better traction.
In conclusion, MBTs are essential components in rubber compounding, providing excellent vulcanization properties and improving the physical properties of rubber products. The use of MBTs in the automotive industry and consumer products has proven to be effective, resulting in better processing times, extended lifespan, and improved durability.