What Makes MBS Rubber Accelerators a Game-Changer in Tire Manufacturing?
19/04/2024
MBS rubber accelerators offer a balance between performance and eco-friendliness in the rubber industry. Manufacturers like CHEMBROAD are committed to developing innovative and sustainable accelerator solutions that meet the evolving needs of customers and regulatory requirements. By prioritizing safety, environmental sustainability, and regulatory compliance, companies can ensure the responsible use of MBS accelerators and contribute to a greener and safer future for the rubber industry.
Understanding the Role of MBS Rubber Accelerators in Tire Manufacturing
1.1 Introduction to MBS Rubber Accelerators
MBS rubber accelerators are vital components in the tire manufacturing process. These additives play a crucial role in expediting the vulcanization process, which transforms raw rubber into the durable and resilient material essential for tire production. Among the leading manufacturers of MBS rubber accelerators is CHEMBROAD, renowned for its commitment to quality and innovation in rubber chemicals.
1.2 Importance of Accelerators in Tire Production
Accelerators are indispensable in tire production due to their ability to hasten the vulcanization process. Vulcanization involves cross-linking rubber molecules to enhance strength, elasticity, and durability. Without accelerators, this process would be prohibitively slow, hindering mass production and compromising tire quality.
1.3 Chemical Composition and Functionality of MBS Accelerators
MBS accelerators typically contain sulfur and various organic compounds. These compounds facilitate the cross-linking of rubber molecules by promoting the formation of sulfur bridges. Additionally, MBS accelerators often incorporate a co-agent, such as zinc oxide, to enhance vulcanization efficiency and impart specific properties to the finished product.
Impact of MBS Accelerators on Tire Performance
2.1 Mechanisms of Acceleration in Rubber Vulcanization
MBS accelerators operate by activating the sulfur atoms present in the rubber compound, thereby initiating the cross-linking process. This activation lowers the activation energy required for sulfur vulcanization, significantly accelerating the reaction kinetics. As a result, tires produced with MBS accelerators exhibit superior mechanical properties, such as enhanced tensile strength, tear resistance, and abrasion resistance.
2.2 Comparative Analysis with Other Accelerator Types
While MBS accelerators are widely used in tire manufacturing, they are just one type among several accelerator families. Comparative studies have shown that MBS accelerators offer distinct advantages over alternative accelerators, such as sulfenamides and thiurams, in terms of processing safety, vulcanization efficiency, and tire performance.
2.3 Applications Beyond Rubber Vulcanization
Beyond tire manufacturing, MBS accelerators find applications in various rubber products, including conveyor belts, seals, gaskets, and automotive components. Their versatility and efficacy make them indispensable in industries reliant on high-performance elastomers.
Environmental Sustainability and MBS Rubber Accelerators: Balancing Performance and Eco-Friendliness
3.1 Introduction to Sustainable Rubber Manufacturing
In recent years, the rubber industry has increasingly focused on adopting sustainable practices to mitigate its environmental footprint. Sustainable rubber manufacturing encompasses various strategies aimed at reducing resource consumption, minimizing waste generation, and enhancing overall eco-friendliness throughout the production process.
3.2 Environmental Impact of Traditional Accelerators
Traditional rubber accelerators, while essential for facilitating the vulcanization process, can pose environmental risks due to their chemical composition and manufacturing processes. These accelerators may contain hazardous substances that can persist in the environment and contribute to pollution, posing risks to ecosystems and human health if not managed properly.
3.3 Eco-Friendly Attributes of MBS Accelerators
MBS rubber accelerators, manufactured by leading companies like CHEMBROAD, offer a more sustainable alternative to traditional accelerators. These accelerators are designed to minimize environmental impact while maintaining high performance standards. With their carefully formulated chemical compositions and manufacturing processes, MBS accelerators exhibit eco-friendly attributes that align with the principles of sustainable rubber manufacturing.
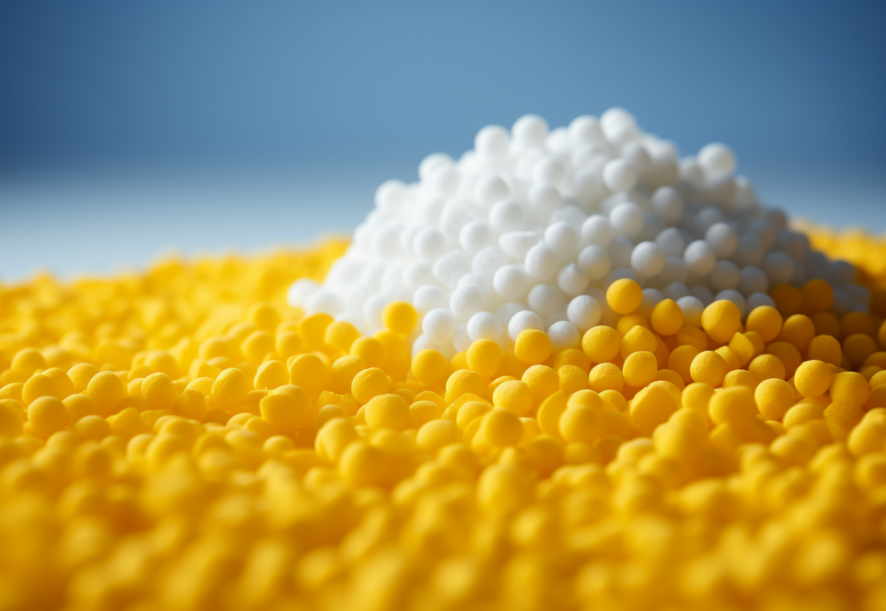
Regulatory Landscape and Compliance
4.1 Innovations Towards Greener Accelerator Solutions
Recognizing the need for greener accelerator solutions, regulatory bodies worldwide have implemented stringent standards and regulations to promote environmental sustainability in the rubber industry. Manufacturers like CHEMBROAD are at the forefront of innovation, continuously developing new formulations and technologies to meet regulatory requirements and exceed environmental standards.
4.2 Adopting Sustainable Practices in the Rubber Industry
As the demand for sustainable rubber products continues to grow, industry stakeholders are increasingly embracing sustainable practices throughout the supply chain. From raw material sourcing to product distribution, companies are exploring ways to reduce energy consumption, minimize waste generation, and implement eco-friendly manufacturing processes. By prioritizing sustainability, the rubber industry can minimize its environmental footprint while meeting the needs of consumers and regulatory authorities.
Advancements in MBS Rubber Accelerators: Unveiling Cutting-Edge Technologies
5.1 Evolution of MBS Accelerators: Past to Present
The development of MBS rubber accelerators has evolved significantly over time, driven by advancements in chemical engineering, materials science, and process optimization. From their humble beginnings to their current state-of-the-art formulations, MBS accelerators have undergone continuous refinement to meet the ever-changing demands of the rubber industry.
5.2 Recent Innovations in MBS Accelerator Chemistry
Recent innovations in MBS accelerator chemistry have focused on enhancing performance, sustainability, and safety. New formulations incorporate novel ingredients and manufacturing techniques to improve acceleration efficiency, reduce environmental impact, and comply with regulatory standards. These innovations represent a significant step forward in the quest for greener and more sustainable accelerator solutions.
5.3 Advantages and Limitations of New Technologies
While advancements in MBS accelerator technology offer numerous advantages, it’s essential to acknowledge their limitations and challenges. Balancing performance, eco-friendliness, and cost-effectiveness remains a constant endeavor for manufacturers and researchers alike. Additionally, regulatory compliance and market acceptance play pivotal roles in determining the success and adoption of new technologies in the rubber industry.
Potential Disruption in Rubber Industry
6.1 Industry Adoption and Market Trends
The adoption of cutting-edge MBS accelerator technologies has the potential to disrupt the rubber industry landscape significantly. Companies that embrace innovation and sustainability stand to gain a competitive edge in the market, attracting environmentally conscious consumers and securing partnerships with forward-thinking businesses. Market trends indicate a growing preference for sustainable rubber products, driving demand for eco-friendly accelerator solutions.
6.2 Future Prospects and Emerging Research Areas
Looking ahead, the future of MBS rubber accelerators is promising, with emerging research areas focusing on enhancing performance, improving sustainability, and addressing regulatory requirements. Collaborative efforts between academia, industry, and regulatory agencies will drive innovation and shape the direction of accelerator technology in the years to come. By prioritizing environmental sustainability and embracing technological advancements, the rubber industry can navigate challenges and seize opportunities for growth and prosperity.
Safety and Handling of MBS Rubber Accelerators: Best Practices and Guidelines
7.1 Understanding Safety Hazards Associated with MBS Accelerators
While MBS rubber accelerators offer numerous benefits, it’s essential to understand and mitigate associated safety hazards. These accelerators may pose risks to human health and the environment if not handled, stored, and disposed of properly. Understanding the chemical properties and potential hazards of MBS accelerators is the first step in ensuring safe handling practices.
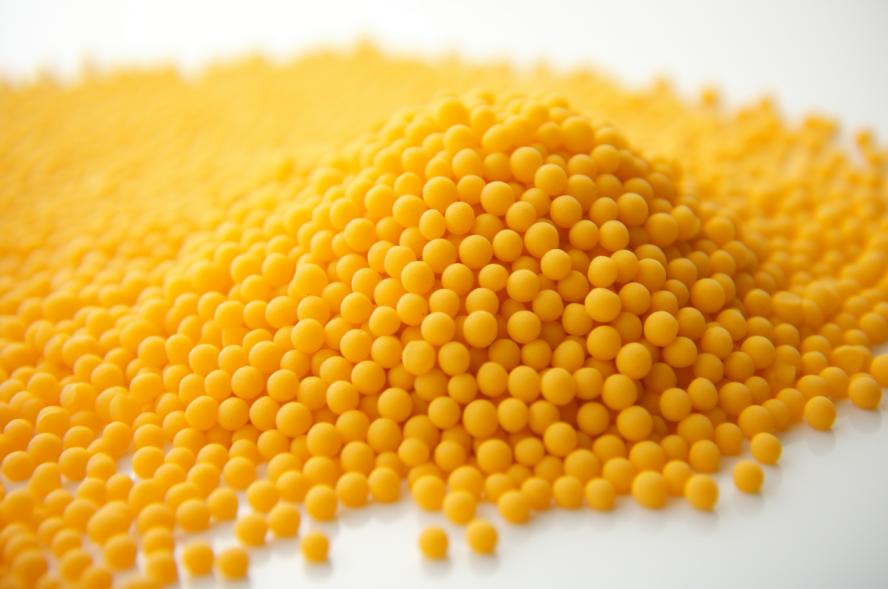
7.2 Proper Handling and Storage Procedures
Proper handling and storage procedures are critical for minimizing the risk of accidents and exposure to MBS accelerators. Companies like CHEMBROAD prioritize employee safety by implementing stringent protocols for handling, transporting, and storing accelerator products. This includes using appropriate containers, labeling materials correctly, and segregating incompatible substances to prevent chemical reactions and spills.
7.3 Personal Protective Equipment (PPE) Requirements
Personal protective equipment (PPE) plays a vital role in safeguarding workers from potential hazards associated with MBS accelerators. Employees handling these chemicals must wear appropriate PPE, including gloves, goggles, respirators, and protective clothing, to prevent skin contact, inhalation, and ingestion. Regular training and monitoring ensure that workers understand and adhere to PPE requirements at all times.
7.4 Emergency Response and Spill Management
Despite rigorous safety measures, accidents involving MBS accelerators can still occur. In such instances, prompt and effective emergency response is crucial for minimizing the impact on human health and the environment. Companies must have comprehensive spill response plans in place, including procedures for containment, cleanup, and disposal of spilled materials. Regular drills and training exercises help ensure that employees are prepared to respond to emergencies effectively.
7.5 Regulatory Compliance and Safety Standards
Compliance with regulatory requirements and safety standards is non-negotiable when handling MBS accelerators and other chemical substances. Regulatory agencies, such as the Occupational Safety and Health Administration (OSHA) and the Environmental Protection Agency (EPA), establish guidelines and regulations to protect workers and the environment from potential hazards. Companies must stay informed about relevant regulations and ensure full compliance to avoid penalties and legal liabilities.
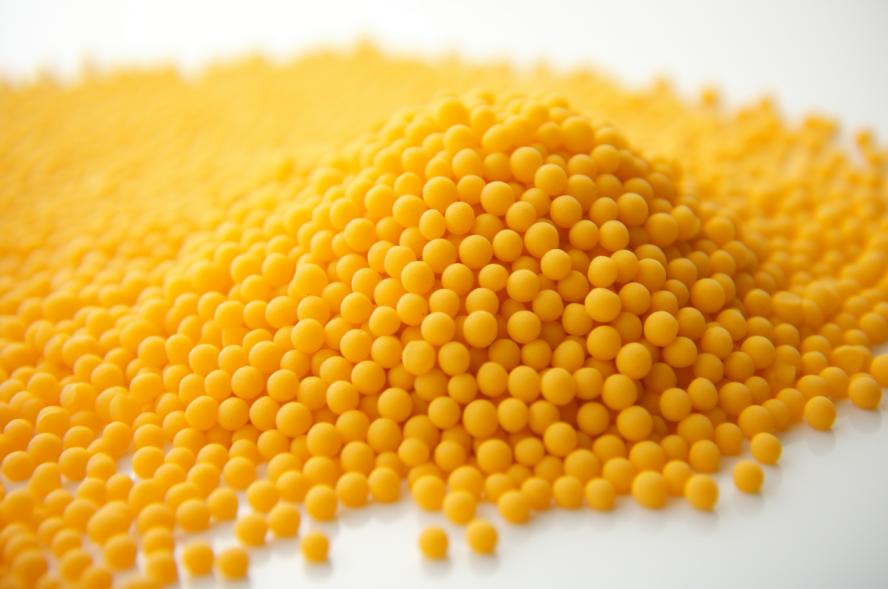
7.6 Training and Education for Safe Handling of Accelerators
Training and education are essential components of a comprehensive safety program for handling MBS accelerators. Companies must provide employees with thorough training on the safe handling, storage, and disposal of accelerator products, as well as emergency response procedures. Ongoing education and communication initiatives help reinforce safety protocols and promote a culture of safety throughout the organization.
Conclusion
In conclusion, MBS rubber accelerators play a pivotal role in tire manufacturing, facilitating the vulcanization process and enhancing tire performance. Manufacturers like CHEMBROAD continue to drive innovation in accelerator technology, prioritizing quality, safety, and sustainability. With ongoing advancements and adherence to best practices, MBS accelerators will remain indispensable in the production of high-quality rubber products for years to come.