Isobutylene Rubber: Properties, Applications, and Advantages
19/01/2024
Isobutylene rubber, also known as butyl rubber, is a synthetic elastomer that has become increasingly popular in recent years due to its unique properties. It is a copolymer of isobutylene and isoprene, and is known for its excellent air retention and impermeability to gases. These properties have led to its use in a wide range of applications, from tire inner tubes to pharmaceutical packaging.
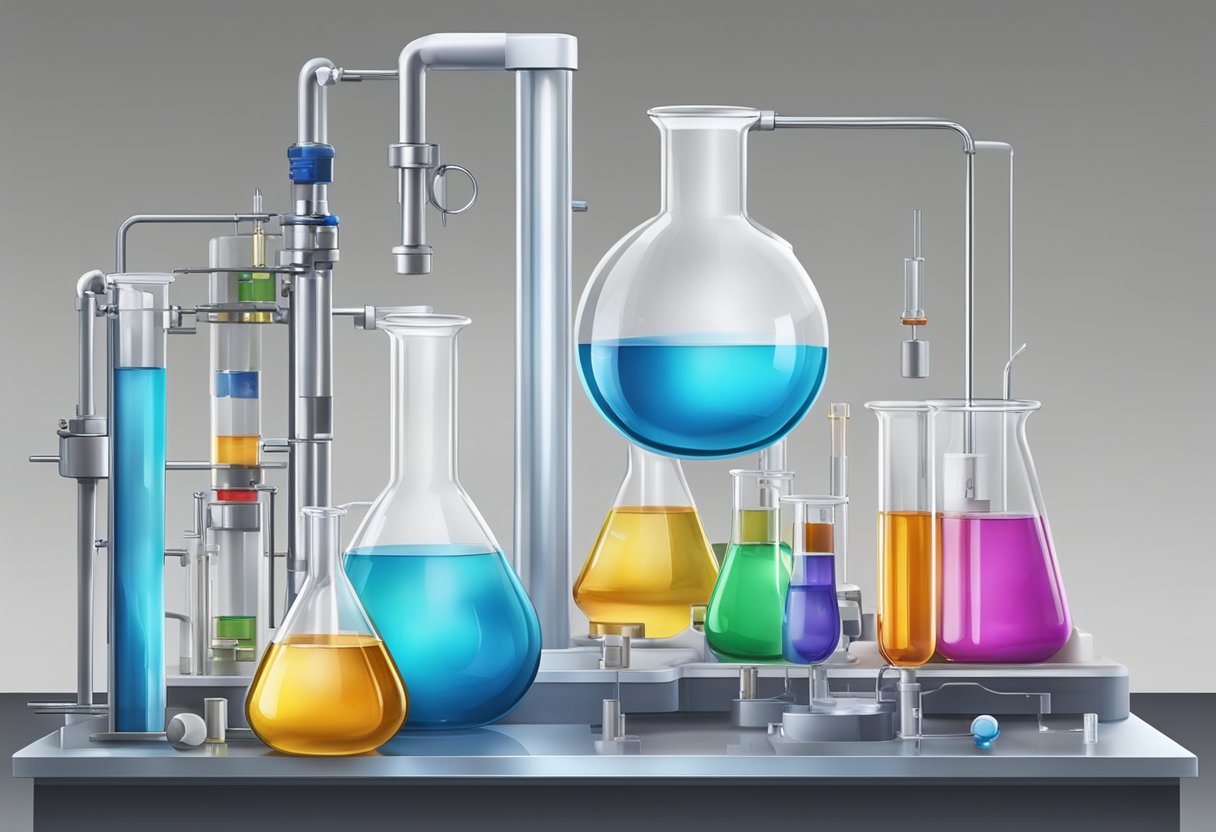
One of the key advantages of isobutylene rubber is its resistance to air and gas permeation. This makes it an ideal material for use in applications where airtight seals are required, such as in tire inner tubes and pharmaceutical packaging. Additionally, it has excellent resistance to water and chemicals, making it suitable for use in harsh environments. Its low gas permeability also makes it an excellent choice for use in fuel systems, where it is used to prevent the evaporation of gasoline and other fuels.
Another advantage of isobutylene rubber is its ability to maintain its properties over a wide range of temperatures. It remains flexible even at low temperatures, making it suitable for use in cold climates. At the same time, it retains its strength and elasticity at high temperatures, making it suitable for use in hot environments. This versatility has led to its use in a wide range of applications, from automotive components to roofing membranes.
Chemical Structure of Isobutylene Rubber
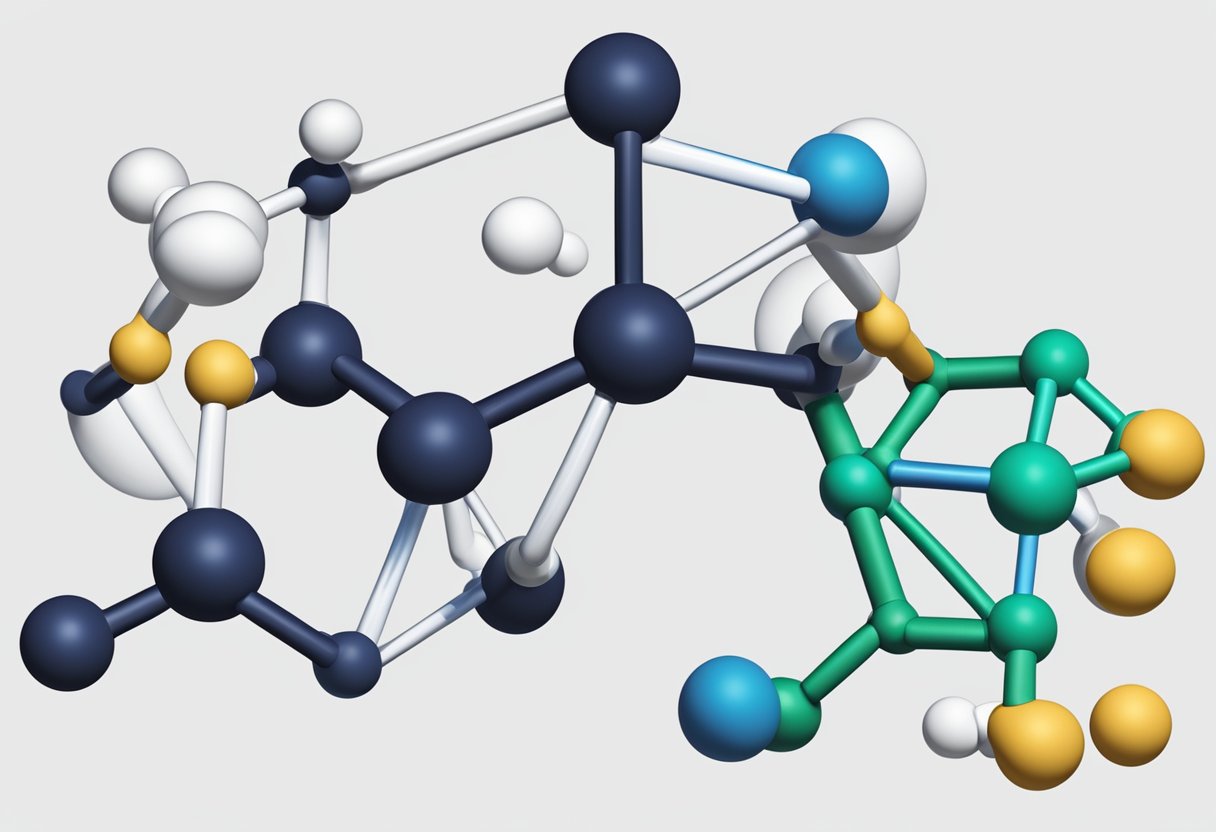
Isobutylene rubber, also known as polyisobutylene, is a synthetic elastomer made from the polymerization of isobutylene. Its chemical structure consists of a long chain of repeating isobutylene units, with a small amount of isoprene units added to improve its elasticity.
The molecular weight of isobutylene pbt rsan rubber can vary depending on the manufacturing process, but it typically ranges from 40,000 to 200,000 g/mol. The high molecular weight contributes to its excellent resistance to heat, ozone, and chemicals.
Isobutylene rubber has a low glass transition temperature, which means it remains flexible and elastic even at low temperatures. This makes it ideal for use in applications such as sealants, adhesives, and fuel hoses.
Overall, the chemical structure of isobutylene rubber gives it unique properties that make it a valuable material in a variety of industries.
Production Process of Isobutylene Rubber
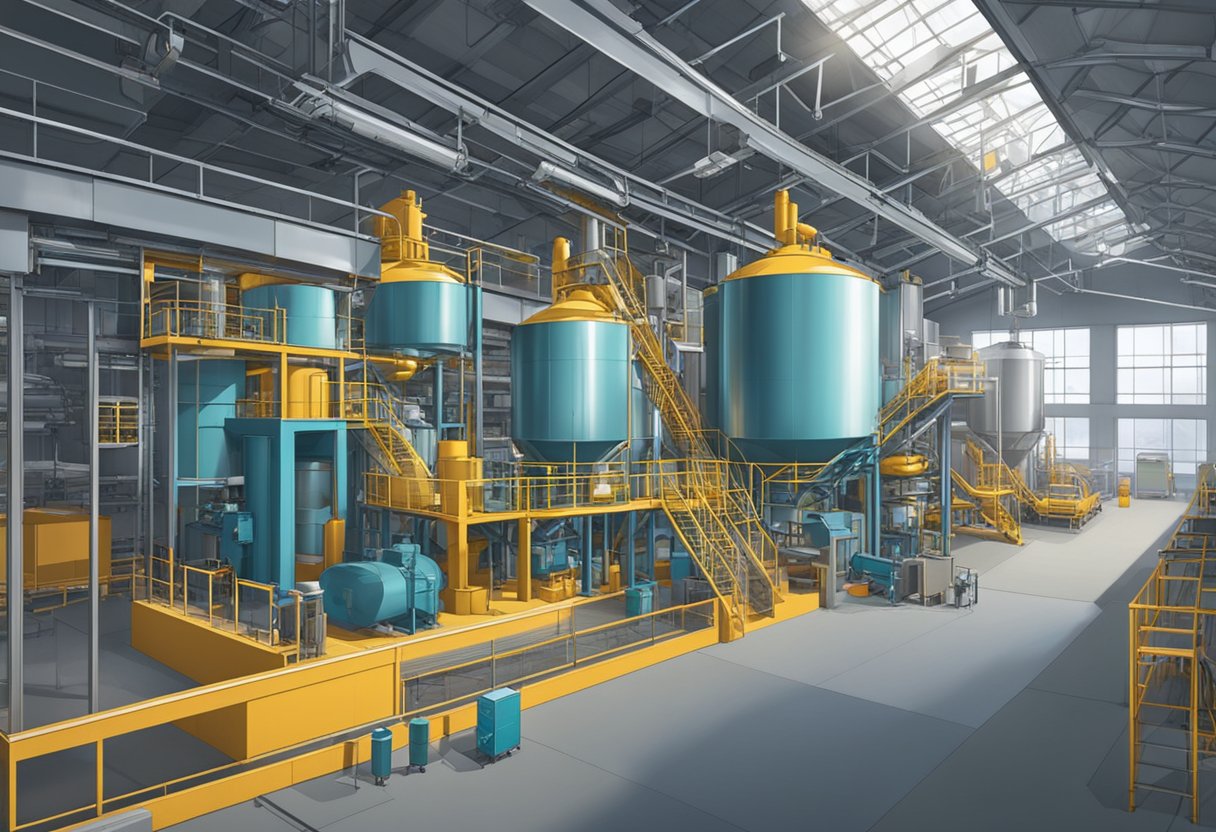
Raw Material Acquisition
The production process of isobutylene rubber starts with the acquisition of raw materials. The primary raw materials required for the production of isobutylene rubber include isobutylene, a hydrocarbon gas, and a small amount of a diene monomer. Isobutylene is typically obtained as a by-product from the production of ethylene and propylene. The diene monomer is usually sourced from petrochemical feedstocks.
Polymerization Methods
The polymerization of isobutylene and the diene monomer is carried out through two primary methods: cationic polymerization and anionic polymerization. Cationic polymerization is typically used for the production of low molecular weight isobutylene rubber, while anionic polymerization is used for the production of high molecular weight isobutylene rubber.
In cationic polymerization, a cationic initiator is used to initiate the polymerization reaction. The monomers are then added to the reaction vessel, and the polymerization reaction is carried out under controlled conditions of temperature and pressure. The resulting low molecular weight isobutylene rubber is then purified and processed further.
In anionic polymerization, an anionic initiator is used to initiate the polymerization reaction. The monomers are then added to the reaction vessel, and the polymerization reaction is carried out under controlled conditions of temperature and pressure. The resulting high molecular weight isobutylene rubber is then purified and processed further.
Post-Polymerization Processing
After the polymerization process, the isobutylene rubber is subjected to post-polymerization processing. This includes compounding, vulcanization, and shaping. Compounding involves the addition of various additives, such as fillers, plasticizers, and stabilizers, to improve the properties of the isobutylene rubber. Vulcanization involves the cross-linking of the polymer chains to improve the strength and durability of the rubber. Shaping involves the molding of the rubber into the desired shape.
Overall, the production process of isobutylene rubber is a complex and highly controlled process that requires careful attention to detail at every stage. The resulting rubber has a wide range of applications, including in the automotive, construction, and industrial sectors.
Properties of Isobutylene Rubber
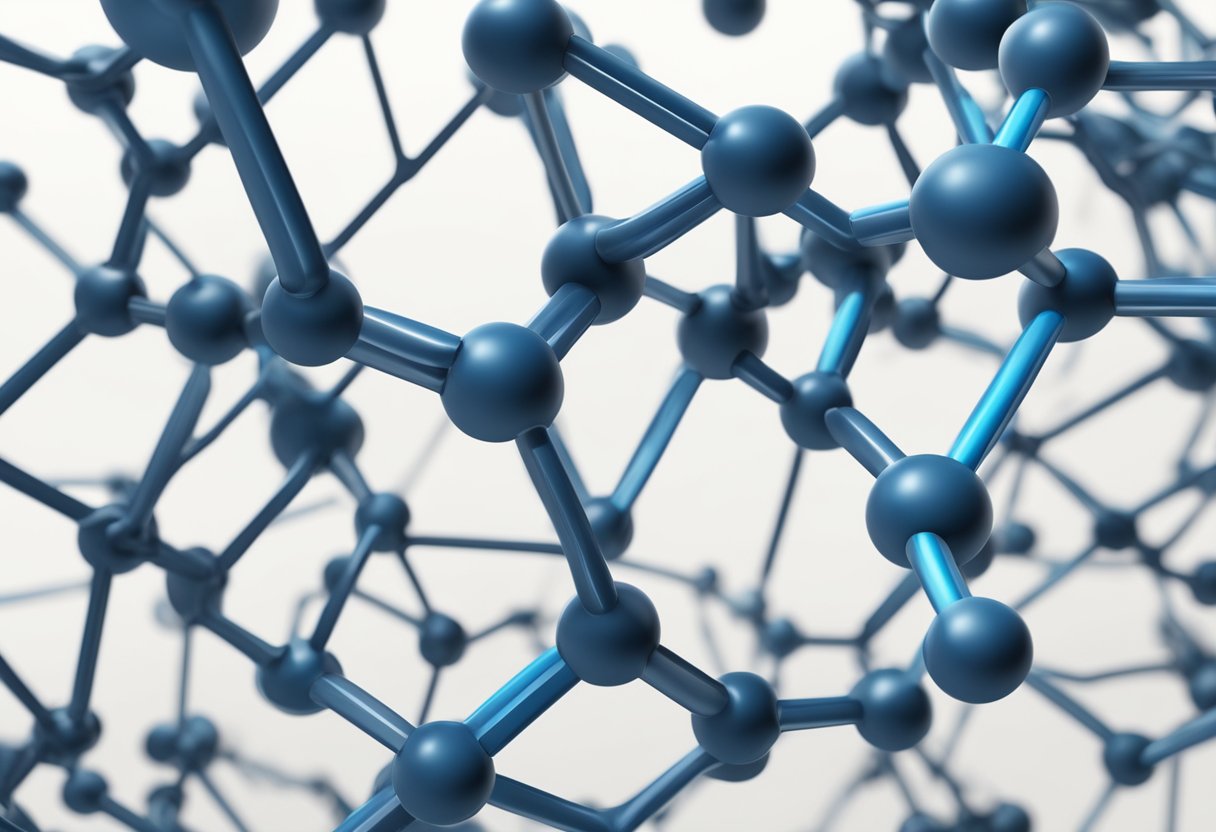
Physical Properties
Isobutylene rubber, also known as polyisobutylene, is a synthetic rubber that is known for its excellent air retention properties. It has a low permeability to gases, making it an ideal material for use in tire inner tubes and other applications where air retention is important. The rubber is also highly resistant to abrasion, making it a popular choice for use in seals and gaskets.
Isobutylene rubber has a high molecular weight, which gives it a high tensile strength and good resistance to tearing. It is also highly elastic, allowing it to stretch and return to its original shape without losing its properties.
Chemical Resistance
Isobutylene rubber has excellent resistance to a wide range of chemicals, including acids, alkalis, and polar solvents. It is also highly resistant to ozone and UV light, making it suitable for use in outdoor applications.
The rubber is not compatible with hydrocarbons, however, and can be damaged by exposure to oils and fuels. It is also not recommended for use in applications where it will come into contact with strong oxidizing agents.
Thermal Stability
Isobutylene rubber has good thermal stability, with a high resistance to heat and cold. It can withstand temperatures ranging from -40°C to 150°C, making it suitable for use in a wide range of applications.
The rubber is also resistant to aging and degradation, and has a long service life when properly stored and maintained.
Applications of Isobutylene Rubber
Isobutylene rubber, also known as butyl rubber, is a synthetic rubber that has excellent air retention properties and is resistant to gas permeation. Due to these properties, it finds a wide range of applications in various industries.
Automotive Industry
Isobutylene rubber is extensively used in the automotive industry for the production of inner tubes of tires. It provides excellent air retention properties, which helps in maintaining the pressure of the tire for a longer duration. Additionally, it also provides good resistance to heat and chemicals, making it an ideal material for use in the production of automotive belts, hoses, and gaskets.
Medical Devices
Isobutylene rubber is also used in the production of medical devices such as stoppers for vials and syringes. Its excellent gas permeation resistance properties make it an ideal material for use in such applications. It is also used in the production of catheters and other medical tubing due to its biocompatibility and resistance to sterilization.
Consumer Goods
Isobutylene rubber is used in various consumer goods such as adhesives, sealants, and chewing gum. Its excellent air retention and gas permeation resistance properties make it an ideal material for use in the production of adhesives and sealants. Additionally, its low gas permeability makes it an ideal material for use in the production of chewing gum, as it helps in maintaining the flavor and freshness of the gum for a longer duration.
Overall, isobutylene rubber is a versatile material that finds a wide range of applications in various industries due to its excellent air retention and gas permeation resistance properties.
Market Overview of Isobutylene Rubber
Global Demand
Isobutylene rubber, also known as butyl rubber, is a synthetic elastomer that has excellent air retention properties, making it ideal for use in tire inner tubes, pharmaceutical stoppers, and other applications where air and gas impermeability are required. The global demand for isobutylene rubber is expected to grow steadily in the coming years, driven by the increasing demand for high-performance tires, as well as the growing demand for pharmaceutical packaging.
Key Manufacturers
The isobutylene rubber market is dominated by a few key manufacturers, including ExxonMobil Chemical, Lanxess, and PJSC Nizhnekamskneftekhim. These companies have a significant market share and are constantly investing in research and development to improve the performance and properties of their products.
Market Trends
One of the major trends in the isobutylene rubber market is the increasing demand for halobutyl rubber, a type of isobutylene rubber that has been halogenated to improve its properties. Halobutyl rubber is widely used in the production of inner tubes for tires, pharmaceutical stoppers, and other applications where air and gas impermeability are required.
Another trend in the market is the growing demand for isobutylene rubber in the Asia-Pacific region, particularly in China and India. This is attributed to the increasing demand for high-performance tires in these countries, as well as the growing demand for pharmaceutical packaging.
Overall, the isobutylene rubber market is expected to grow steadily in the coming years, driven by the increasing demand for high-performance tires and the growing demand for pharmaceutical packaging. With the key manufacturers investing in research and development to improve the performance and properties of their products, the market is expected to remain competitive and innovative.
Environmental Impact and Sustainability
Recycling and Disposal
Isobutylene rubber, also known as butyl rubber, has a high level of durability and can last for a long time, making it a good choice for products that require long-term use. However, when it comes to disposal, isobutylene rubber can pose some challenges.
One of the main issues with isobutylene rubber is that it is not biodegradable, which means that it cannot be broken down naturally by microorganisms. This means that if it is not disposed of properly, it can end up in landfills and take up space for a long time.
On the other hand, isobutylene rubber can be recycled and reused. It can be shredded and turned into granules, which can then be used to make new products. This process is known as mechanical recycling and is a more sustainable option than disposal.
Regulations and Standards
There are several regulations and standards in place to ensure that isobutylene rubber is produced and used in a way that is safe and environmentally responsible. For example, the European Union’s REACH regulation requires that all chemicals, including isobutylene rubber, are tested for their potential impact on human health and the environment before they can be sold in the EU.
In addition, the International Organization for Standardization (ISO) has developed standards for the production and use of isobutylene rubber, including ISO 9001 and ISO 14001. These standards cover quality management and environmental management, respectively, and help to ensure that isobutylene rubber is produced and used in a way that is safe and sustainable.
Overall, while there are some challenges associated with the disposal of isobutylene rubber, it can be recycled and reused, and there are regulations and standards in place to ensure that it is produced and used in a way that is safe and sustainable.
Innovation and Future Developments
Research Directions
Isobutylene rubber has been widely used in various industries due to its excellent properties such as high temperature resistance, chemical stability, and gas impermeability. In recent years, researchers have been exploring new ways to improve the properties of isobutylene rubber and expand its applications.
One of the research directions is to enhance the mechanical properties of isobutylene rubber. By introducing reinforcing fillers such as nanocellulose, graphene, and carbon nanotubes, the tensile strength and modulus of isobutylene rubber can be significantly improved. Moreover, researchers are also investigating the effects of different crosslinking agents and curing methods on the mechanical properties of isobutylene rubbers.
Another research direction is to develop new types of isobutylene rubber with novel properties. For example, isobutylene rubbers with self-healing ability has been developed by incorporating microcapsules containing healing agents. This type of rubber can automatically repair the damage caused by external forces, which can greatly improve the durability and reliability of rubber products.
Technological Advancements
With the advancement of technology, new manufacturing processes for isobutylene rubber have emerged. For instance, the continuous polymerization process has been widely used to produce high-quality isobutylene rubbers with low impurity levels. This process can significantly reduce the production cost and improve the production efficiency of isobutylene rubbers.
Moreover, new processing techniques such as extrusion, injection molding, and 3D printing have also been developed for isobutylene rubbers. These techniques can not only improve the processing efficiency but also expand the application range of isobutylene rubbers.
In conclusion, with the continuous efforts of researchers and the advancement of technology, isobutylene rubber is expected to have more promising applications in various fields in the future.
Quality Control and Testing
Standard Test Methods
Isobutylene rubber undergoes rigorous testing to ensure its quality and integrity. The standard test methods used for isobutylene rubbers include measuring the physical properties such as tensile strength, elongation, and hardness. The testing is done to ensure that the rubber meets the required specifications and is suitable for its intended use.
In addition to physical testing, other standard test methods include chemical analysis to determine the composition of the rubber and ensure that it is free from any impurities or contaminants. The tests are conducted in accordance with ASTM standards to ensure consistency and accuracy in the results.
Quality Assurance Protocols
Quality assurance protocols are in place to ensure that isobutylene rubbers meets the required standards. The protocols include regular inspections of the manufacturing process, from raw material selection to the final product. The inspections are conducted to identify any deviations from the required specifications and ensure that corrective actions are taken.
Quality assurance protocols also include testing of the final product to ensure that it meets the required specifications. This testing is done using standard test methods to ensure consistency and accuracy in the results. Any non-conforming product is identified and appropriate corrective actions are taken.
Overall, the quality control and testing of isobutylene rubbers is a critical aspect of ensuring its performance and suitability for its intended use. The use of standard test methods and quality assurance protocols ensures consistency and accuracy in the results, providing confidence to manufacturers and end-users alike.
Trade and Distribution
Supply Chain Dynamics
The production of isobutylene rubbers involves a complex supply chain that starts with the sourcing of raw materials such as butyl rubber and isobutylenes. The butyl rubber is obtained from the polymerization of isoprene and isobutylene, while the isobutylene is typically derived from the processing of petroleum or natural gas.
Once the raw materials are obtained, they are transported to the manufacturing facilities where they undergo a series of chemical reactions to produce isobutylene rubbers. The finished product is then packaged and shipped to various distributors and end-users.
The supply chain for isobutylene rubber is heavily influenced by the availability and cost of raw materials, as well as the demand for the finished product. As a result, fluctuations in the price of crude oil and natural gas can have a significant impact on the supply chain dynamics of isobutylene rubbers.
Distribution Channels
Isobutylene rubber is distributed through a variety of channels, including direct sales to end-users, as well as through intermediaries such as distributors and wholesalers.
Direct sales are typically made to large manufacturers who use isobutylene rubbers as a key component in their products. These manufacturers often have long-term contracts with isobutylene rubbers producers to ensure a reliable supply of the material.
Distributors and wholesalers play an important role in the distribution of isobutylene rubbers to smaller manufacturers and end-users. These intermediaries often maintain large inventories of isobutylene rubbers and other related products to ensure timely delivery to their customers.
Overall, the trade and distribution of isobutylene rubber is influenced by a variety of factors, including the availability and cost of raw materials, the demand for the finished product, and the competitive landscape of the industry.
Challenges and Limitations
Material Limitations
Isobutylene rubbers, also known as butyl rubber, has excellent air retention properties, making it an ideal material for inner tubes and tire liners. However, it has some limitations when it comes to other applications. For example, it has poor resistance to oil and solvents, which limits its use in certain industrial applications. Additionally, it has a relatively low tensile strength and tear resistance compared to other elastomers, which makes it unsuitable for high-stress applications.
Economic Constraints
Another limitation of isobutylene rubber is its relatively high cost compared to other elastomers. This is due to the complex manufacturing process and the limited availability of raw materials. As a result, it is often used in niche applications where its unique properties justify the higher cost.
Despite these limitations, isobutylene rubbers remains an important material in various industries, including automotive, construction, and healthcare. Its excellent air retention properties make it an ideal material for inner tubes and tire liners, while its impermeability to gases and liquids makes it suitable for sealing applications. With ongoing research and development, it is possible that new formulations of isobutylene rubbers will be developed that overcome some of its current limitations, making it an even more versatile material.