6 Troubleshooting Common Issues with Butyl Synthetic Rubber
31/10/2024
Have you ever pondered what ensures your car tires remain secure on diverse road surfaces or how certain sealants sustain their robustness over prolonged durations? The answer, in many cases, is rooted in butyl synthetic rubber, an extraordinary material celebrated for its distinctive qualities. Characterized by its versatility, butyl synthetic rubber finds extensive utilization across numerous industries, ranging from the automotive sector to medical equipment manufacturing. Despite its impressive array of advantages, this synthetic rubber is not without its unique set of challenges, necessitating a strategic approach to troubleshooting. In this blog, we delve into six prevalent issues related to butyl synthetic rubber and outline effective strategies to resolve them.
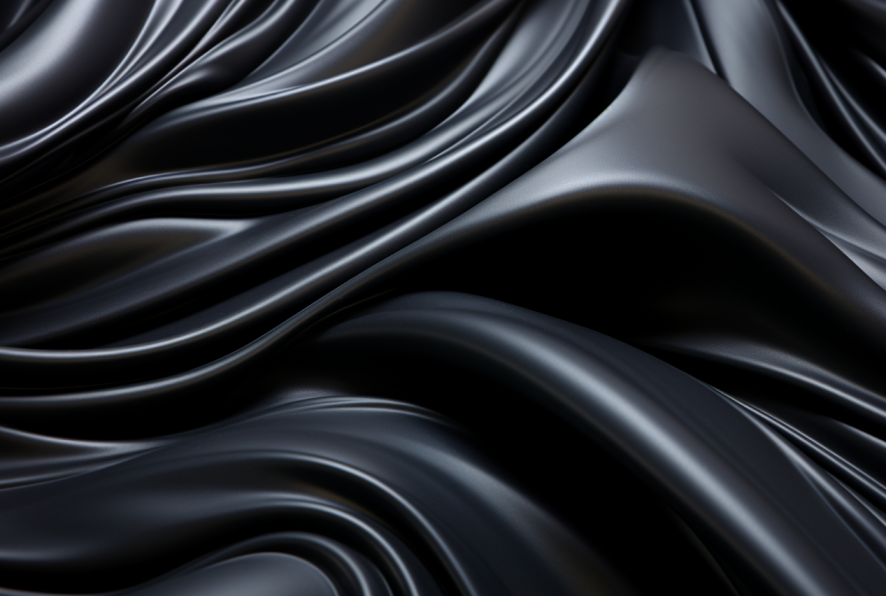
Issue 1: Inadequate Adhesion in Bonding Applications
Understanding the Complexity of Adhesion Problems
A frequently observed issue in the application of butyl synthetic rubber is suboptimal adhesion, particularly in bonding contexts. This inadequacy can result in the breakdown of seals and joints, which are indispensable components in products like vehicle tires and rubber tubing. While the chemical structure of butyl rubber offers substantial benefits for many applications, it can also pose obstacles to adhesion if not carefully managed.
Analyzing the Contributing Factors Behind Adhesion Failures
Multiple factors may contribute to insufficient adhesion, including the presence of contaminants such as dust, oils, or moisture on the surface. The use of an inappropriate adhesive type or non-compliance with recommended application procedures may also yield unsatisfactory results. Furthermore, as butyl rubber ages, its surface energy can change, complicating the bonding process and leading to more adhesion issues.
Strategies to Enhance Adhesion Effectiveness
Addressing this problem necessitates meticulous surface preparation, ensuring all contaminants are removed through methods like abrasion or primer application. Utilizing adhesives specifically formulated for compatibility with butyl synthetic rubber can greatly enhance bonding outcomes. Implementing routine testing and monitoring of adhesive performance over time is vital to maintaining the long-term integrity of the bonded surfaces.
Issue 2: Environmental Degradation and Its Impact on Performance
Recognizing Early Signs of Environmental Wear
Exposure to environmental elements such as UV radiation, ozone, and extreme temperature variations can result in the gradual degradation of butyl synthetic rubber. This deterioration often presents as surface cracking, loss of flexibility, and diminished performance characteristics, potentially jeopardizing the safety and functionality of the affected products.
Examining the Root Causes of Environmental Degradation
Although butyl rubber is known for its resistance to weathering and chemical exposure, it is not entirely impervious to damage. Extended exposure to ozone and ultraviolet light can initiate surface-level cracking, while high temperatures can accelerate the aging process and contribute to material breakdown. These issues are especially prevalent in applications involving continuous heat exposure, such as automotive components.
Preventative Measures and Mitigation Approaches
To counteract these adverse effects, manufacturers should consider integrating additives that bolster the material’s resistance to environmental factors. The inclusion of antioxidants and UV stabilizers can significantly prolong the durability of butyl synthetic rubber. Additionally, adhering to best practices for storage and usage can further extend the lifespan and performance of butyl rubber-based products.
Issue 3: Variability in Quality and Performance
Identifying Inconsistencies in Product Quality
Disparities in the quality and performance of butyl synthetic rubber products can lead to consumer dissatisfaction and, in some cases, pose safety concerns. Batch-to-batch variability and inconsistencies in the production process can result in products that do not meet expected standards.
Exploring the Underlying Causes of Quality Variations
These quality fluctuations typically stem from manufacturing processes, where variations in raw material sourcing, suboptimal mixing procedures, or temperature deviations during production can contribute to the issue. The absence of stringent quality control measures can exacerbate these inconsistencies, making it difficult to ensure consistent mechanical properties across different production runs.
Solutions for Consistent Product Quality
To mitigate these challenges, partnering with a trusted supplier such as Shanghai Chembroad New Materials Co., Ltd. is crucial. With their adherence to ISO9001 certification standards, they implement rigorous quality control practices throughout their production processes. By establishing standardized testing protocols and closely monitoring production variables, manufacturers can achieve greater consistency and reliability in their butyl synthetic rubber products.
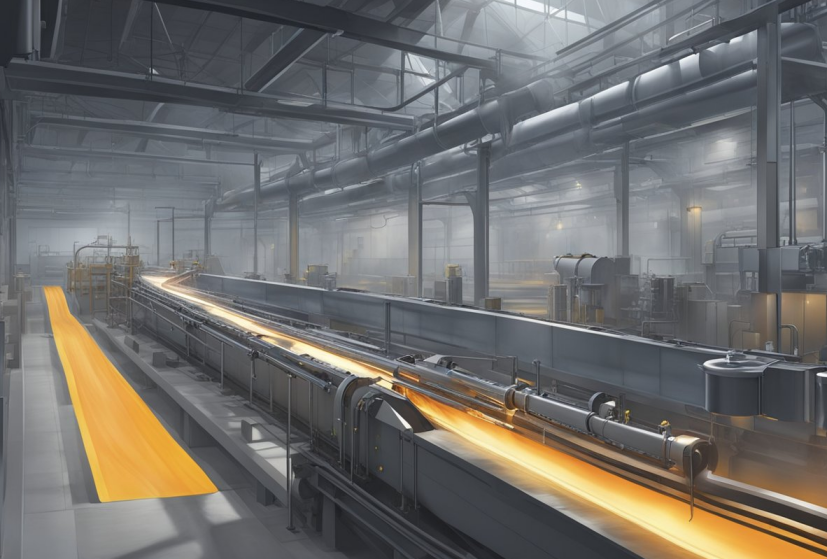
Issue 4: Processing Challenges in Manufacturing
Addressing Processing Complexities
The processing of butyl synthetic rubber can present several challenges, particularly in operations like extrusion and molding. Common difficulties include sticking to machinery surfaces, irregular flow patterns, and maintaining consistent product uniformity, all of which can negatively impact production efficiency and final product quality.
Factors Influencing Processing Difficulties
These processing issues are often influenced by the material’s inherent viscosity, the incorporation of fillers, and the temperatures employed during processing. Insufficient lubrication can cause adhesion to machinery, while inappropriate temperature settings can disrupt flow dynamics during extrusion or molding. Additionally, slight deviations in the rubber’s formulation can alter its behavior during processing.
Optimizing Processing Conditions for Improved Results
Overcoming these hurdles requires fine-tuning processing parameters based on the specific properties of the butyl synthetic rubber formulation in use. Using suitable lubricants and conducting regular maintenance of machinery can also help mitigate these challenges. Collaboration with experienced suppliers who can offer expert guidance and recommendations is essential for refining processing techniques.
Issue 5: Odor Emissions in Butyl Synthetic Rubber Products
Understanding the Sources of Odor Problems
Odor concerns in butyl synthetic rubber products are particularly problematic in consumer-facing applications such as footwear or automotive interiors. Unpleasant odors can lead to negative perceptions and a decrease in product desirability.
Investigating the Origins of Odor Development
The release of odors often originates from the presence of volatile organic compounds (VOCs) within the rubber, or the breakdown of specific additives over time. Additionally, improper curing or subpar processing practices can intensify odor issues, leading to prolonged emission of unpleasant smells.
Strategies to Mitigate Odor Emissions
To minimize odor problems, manufacturers should opt for high-quality raw materials with minimal VOC content and implement optimized curing processes. Testing for odor emissions during product development phases can help identify and address potential odor issues before the products reach the consumer market.
Issue 6: Limitations in Temperature Resistance
Assessing Temperature Resistance Challenges
Although butyl synthetic rubber is renowned for its resistance to numerous environmental factors, its performance under extreme temperatures can be limited. This poses a risk in applications exposed to high or low temperatures, potentially leading to product malfunctions.
Factors Impacting Temperature Stability
The rubber’s intrinsic properties provide a degree of temperature stability, but prolonged exposure to excessive heat can cause the material to soften, while extreme cold can induce brittleness. The formulation, including the types and quantities of fillers, significantly influences the rubber’s temperature performance.
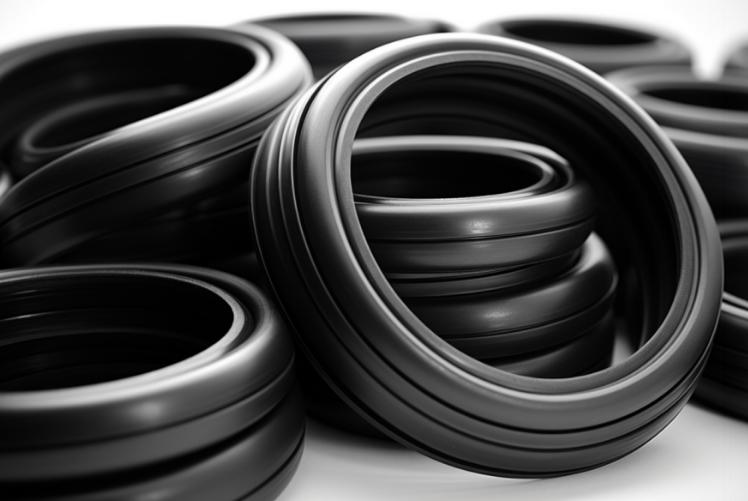
Enhancing Temperature Resistance for Broader Applications
To improve temperature resistance, manufacturers may explore the use of modified formulations with heat stabilizers or reinforced structures. Thorough testing under extreme temperature conditions during product development is essential to ensure the material’s reliability in various operating environments.
Why Partner with Shanghai Chembroad New Materials Co., Ltd.
A Premier Supplier for Butyl Synthetic Rubber Solutions
Selecting a dependable supplier is pivotal when sourcing butyl synthetic rubber, and Shanghai Chembroad New Materials Co., Ltd. is distinguished as a high-tech enterprise specializing in synthetic rubber and other advanced materials. With a robust commitment to quality and environmental sustainability, they have established themselves as a leading player in China’s rubber and plastic chemical industry.
Upholding Stringent Quality and Sustainability Standards
As an ISO9001-certified company, Shanghai Chembroad maintains rigorous standards in manufacturing and management. Their dedication to harmonizing industrial processes with environmental considerations is evident in their ongoing efforts to enhance production methods for sustainable growth. This approach not only fosters environmental preservation but also guarantees that customers receive top-tier products.
Expansive Application Spectrum and Industry Expertise
Shanghai Chembroad’s comprehensive product portfolio serves a wide array of industries, including tire manufacturing, waterproofing materials, and medical supplies. Their extensive knowledge and experience in the field make them an invaluable partner for businesses seeking reliable and high-performance butyl synthetic rubber solutions.
Conclusion
In summary, although butyl synthetic rubber is an exceptional material, it is not devoid of complexities. By understanding these common issues and partnering with a reputable supplier like Shanghai Chembroad New Materials Co., Ltd., businesses can maximize the potential of this versatile rubber in their specific applications.