Environmental Impact: Is Alkyl Phenol Formaldehyde Resin Eco-Friendly?
25/09/2024
Alkyl phenol formaldehyde resin (APF resin) represents a highly adaptable synthetic material that finds extensive use across a wide range of industrial sectors, primarily due to its exceptional adhesive qualities, robust chemical stability, and impressive resistance to high temperatures. However, despite these significant functional advantages, the environmental ramifications of both its production and utilization have increasingly become subjects of considerable concern. This article delves deeply into the eco-friendliness of alkyl phenol formaldehyde resin by scrutinizing the associated sustainability issues, production methodologies, and potential future trends within the resin industry.
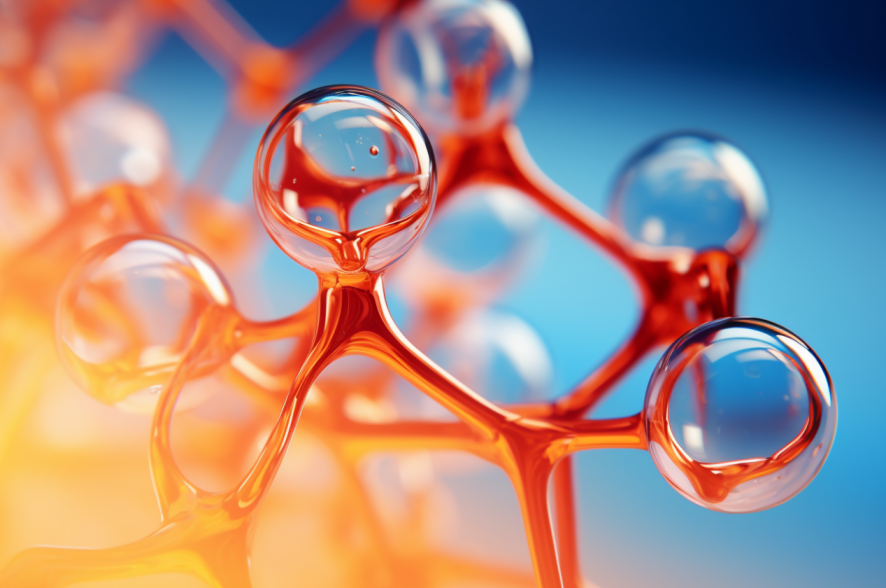
What is Alkyl Phenol Formaldehyde Resin?
Alkyl phenol formaldehyde resin is categorized as a synthetic polymer that results from a chemical reaction known as condensation, which occurs between alkyl phenols and formaldehyde. This class of resin is specifically engineered for use in applications that demand superior chemical resilience, exceptional thermal stability, and long-lasting durability. Industries such as automotive manufacturing, electronics production, rubber processing, and surface coatings heavily depend on the unique properties of APF resins for their ability to facilitate strong bonding between materials, enhance surface characteristics, and boost overall product performance.
Characteristics and Composition
When exploring the key characteristics of alkyl phenol formaldehyde resin, one quickly realizes that the material is distinguished by its high mechanical strength. This particular attribute makes it an ideal candidate for use in structural adhesives that are subjected to significant mechanical stresses. Furthermore, the material’s resistance to both moisture and harsh chemicals enhances its suitability for use in industrial environments where exposure to severe conditions is commonplace. These intrinsic properties are especially critical within the automotive and electronics industries, where APF resins contribute directly to the longevity, resilience, and safety of products ranging from vehicle tires to printed circuit boards and protective surface coatings.
The Role of Chemical Structure in Performance
In terms of its molecular architecture, the phenolic group within the resin’s structure contributes a fundamental element of stability, while the attached alkyl chains offer increased flexibility. This combination of structural rigidity alongside adaptability is what gives alkyl phenol formaldehyde resins their distinct performance profile. Nonetheless, the inclusion of formaldehyde—a volatile organic compound (VOC)—in the production process is a cause for environmental concern. The release of formaldehyde, both during production and usage, has sparked significant debate regarding the long-term environmental impact of these materials.
Industrial Applications and Their Environmental Costs
Alkyl phenol formaldehyde resins serve as integral components across an array of industrial applications. One notable use is in rubber compounding, where they play an essential role in improving the adhesion between rubber and steel, particularly in the manufacturing of tires. In the electronics sector, APF resins are critical in the fabrication of printed circuit boards (PCBs), where their ability to withstand high temperatures is indispensable. Additionally, the resin’s ability to improve the performance of surface coatings and adhesives has solidified its position as a mainstay in both construction and automotive industries. However, while the functional benefits of these applications are well-documented, it is equally important to weigh the environmental costs when assessing the overall eco-friendliness of these resins.
Sustainability Concerns in Alkyl Phenol Formaldehyde Resin Production
Despite the numerous industrial advantages offered by APF resins, their production brings with it several significant sustainability challenges. These issues primarily arise from the inclusion of formaldehyde in the manufacturing process, as well as the broader environmental impact of resin waste once it reaches the end of its useful life.
Formaldehyde Emissions and VOCs
One of the most pressing environmental concerns related to the production of alkyl phenol formaldehyde resins is the emission of formaldehyde, a well-known VOC and hazardous air pollutant. Formaldehyde is integral to the resin synthesis process, yet its release during both production and subsequent use raises alarm bells in terms of health risks and environmental degradation. Prolonged exposure to formaldehyde has been associated with respiratory problems and it has been classified as a carcinogen by multiple health authorities. Furthermore, the emission of VOCs contributes to broader air pollution, exacerbating problems like smog formation and negatively impacting the environment.
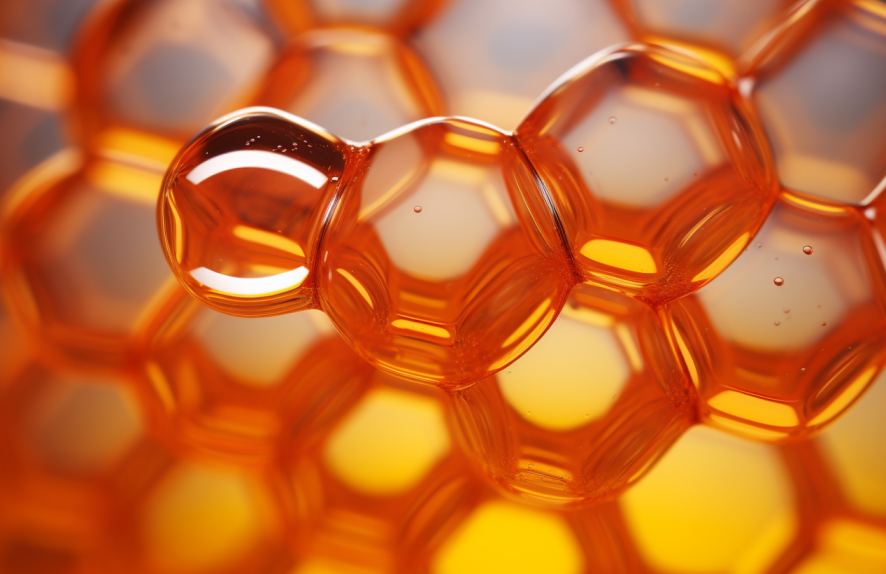
Resin producers like CHEMBROAD, a leading global supplier of alkyl phenol formaldehyde resin, are acutely aware of these challenges. Many are actively pursuing advanced production technologies designed to minimize VOC emissions, though achieving the total elimination of formaldehyde from the synthesis process remains a formidable task for the industry.
Waste Management and the Challenges of Disposal
A further sustainability concern involves the end-of-life disposal of APF resins. Since these resins are not biodegradable, they tend to persist in the environment over prolonged periods, posing long-term pollution risks. When improperly disposed of, resin waste can contribute to the formation of microplastics in both terrestrial and marine ecosystems, which in turn negatively affects wildlife and could potentially lead to bioaccumulation within the food chain, ultimately impacting human health as well.
The cross-linked structure of APF resins complicates efforts to recycle these materials. Unlike thermoplastics, which can be easily melted down and reshaped, thermosetting resins like APF are notoriously difficult to break down for reuse. As a result, there has been a growing focus on the development of recycling technologies specifically geared toward reducing the environmental impact of resin waste.
The Environmental Toll of Resource Consumption
The production process for alkyl phenol formaldehyde resins necessitates the consumption of considerable amounts of raw materials, energy, and water. For instance, the manufacture of phenols often relies on the extraction of non-renewable fossil fuels, which contributes to the overall carbon footprint of resin production. Additionally, the energy-intensive nature of the manufacturing process leads to significant greenhouse gas emissions, further exacerbating environmental sustainability concerns.
Some industry players are striving to enhance resource efficiency by exploring the use of renewable raw materials and renewable energy sources in the production process. However, these efforts remain in their infancy, and achieving widespread industry adoption will likely require substantial investment in research, development, and technological innovation.
The Future of Alkyl Phenol Formaldehyde Resins: Trends and Market Growth
Although the production and disposal of APF resins present considerable environmental challenges, demand for these materials continues to grow steadily across numerous industrial sectors. This continued growth is largely driven by the need for high-performance adhesives, coatings, and rubber compounds, especially in rapidly industrializing economies. However, the future trajectory of the alkyl phenol formaldehyde resin market will be shaped by the industry’s ability to address environmental sustainability concerns and adapt to increasingly stringent regulatory standards.
Innovations in Environmentally Friendly Resin Production
A notable trend within the APF resin market is the industry’s movement toward the development of more sustainable and eco-friendly production methods. Manufacturers are increasingly dedicating resources to researching alternative ingredients that are less harmful to the environment and can potentially replace formaldehyde in resin synthesis. While the complete eradication of formaldehyde may not be immediately attainable, significant reductions in its use and the mitigation of harmful emissions are realistic goals in the near future.
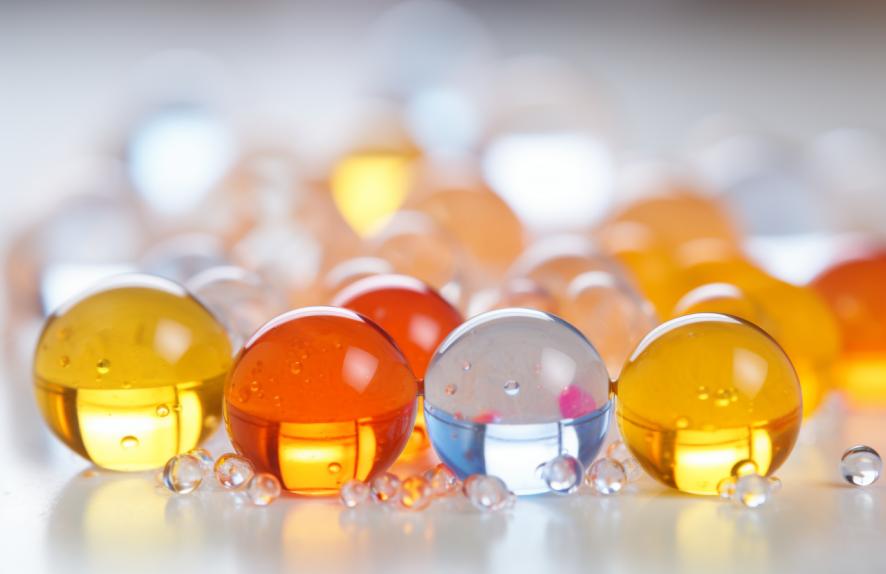
In parallel, advancements in catalytic processes and cleaner production technologies are being explored as a means of reducing both waste and energy consumption. Companies like CHEMBROAD are leading the charge in adopting more sustainable manufacturing practices, such as implementing closed-loop systems that recycle by-products and minimize overall environmental impact.
Regulatory Pressures and the Industry’s Response
With environmental regulations growing increasingly stringent, the APF resin industry is under mounting pressure to conform to new sustainability standards. Governments around the globe are tightening restrictions on VOC emissions and the use of hazardous materials, resulting in a heightened demand for low-emission, environmentally friendly resins.
In response to these regulatory shifts, manufacturers like CHEMBROAD are working diligently to develop new resin formulations that meet or exceed environmental standards while maintaining the high performance characteristics that industries expect. This ongoing effort is critical to ensuring the industry’s long-term competitiveness and relevance in a world that is increasingly prioritizing sustainability.
Market Growth Prospects and Outlook
The global market for alkyl phenol formaldehyde resins is expected to continue its upward trajectory, particularly in regions experiencing rapid industrialization. The automotive, construction, and electronics sectors will remain key drivers of demand. However, the long-term growth and success of the market will be heavily influenced by the industry’s ability to innovate and embrace sustainable practices.
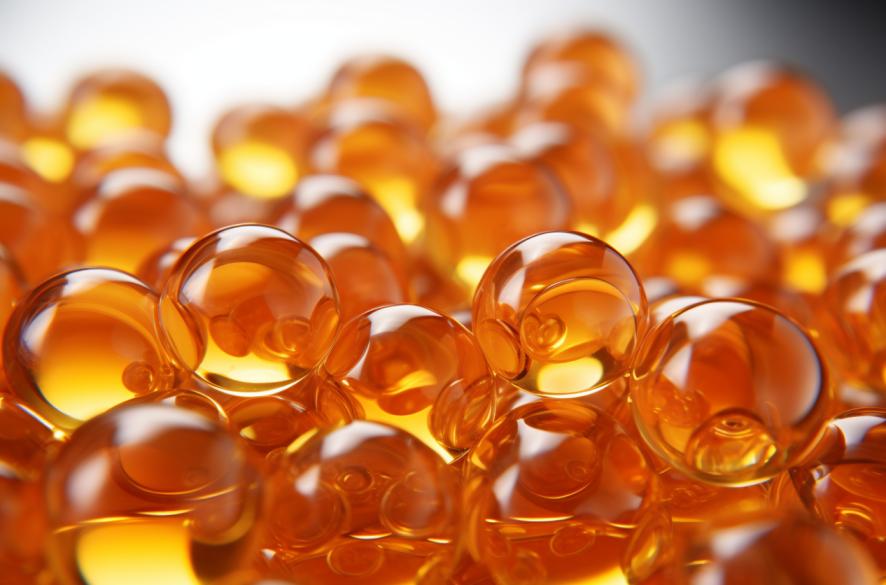
As both consumers and governments place greater emphasis on environmentally friendly products, the demand for greener alternatives to traditional resins is expected to rise. Manufacturers who can strike a balance between performance and sustainability will find themselves well-positioned to thrive in this evolving market landscape. While the challenges ahead are substantial, the resin industry holds the potential to spearhead the development of more sustainable materials that meet the needs of both industry and the environment.
Conclusion
In conclusion, while alkyl phenol formaldehyde resin remains a critical material across a variety of industrial applications—from adhesives to coatings to rubber compounds—the environmental impact of its production and disposal cannot be ignored. Key issues such as formaldehyde emissions, waste management, and the consumption of natural resources have prompted the industry to seek out greener alternatives and adopt more sustainable production practices.
Companies like CHEMBROAD are at the forefront of this transition, striving to reduce the environmental footprint of their products by investing in cleaner technologies and exploring innovative solutions. Although the path to achieving complete environmental sustainability within the resin industry is complex and challenging, the future looks promising as the sector responds to growing regulatory pressures and the rising demand for more eco-friendly materials.