How to Maximize the Benefits of Resin C5 in Your Production Process
20/12/2024
If you’re involved in manufacturing or production, you’ve likely encountered the need for versatile, durable, and high-performing materials. Enter Resin C5 – a petroleum-based resin that’s transforming industries with its ability to enhance the quality, performance, and cost-efficiency of various products. Whether you’re working in the adhesives sector, coatings, rubber compounding, or beyond, Resin C5’s benefits are hard to ignore. But how can you maximize these advantages in your production process? And is it safe for use in consumer goods? Let’s explore.
What is Resin C5?
Resin C5 is a type of hydrocarbon resin derived from the polymerization of the C5 fraction obtained during the cracking of crude oil. It falls into the category of thermoplastic resins, and its versatility makes it a go-to material in industries such as adhesives, coatings, and sealants.
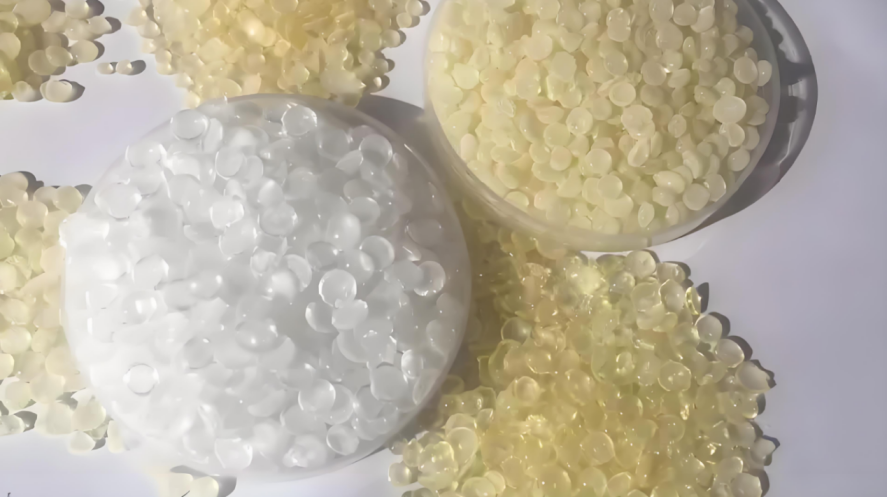
Key Properties That Make Resin C5 Effective
Resin C5’s distinct properties contribute to its broad range of applications. Here’s a quick overview:
Softening Point (95-110°C): This property indicates the temperature at which the resin becomes pliable, which is crucial for bonding applications in hot melt adhesives.
Color (#5 Light Yellow): A-100 Resin C5, for example, exhibits a light yellow color, making it visually appealing for applications where transparency and aesthetic value matter.
Iodine Absorption (135-175 gI/100g): This value reveals the resin’s molecular structure and reactivity, which is important for compatibility in various formulations.
Specific Gravity (0.93-0.98 g/cm³): The density of Resin C5 influences its mass and volume, which in turn affects how it interacts in different applications.
UV Absorbance (K254 2.40-3.97): This feature is particularly important in outdoor products, as it reflects the resin’s ability to absorb harmful ultraviolet light.
Low Ash Content (0.1% Max): The minimal ash content ensures that the resin remains pure and free from impurities, improving the final product’s performance.
These properties make Resin C5 an exceptional material for a wide array of applications. In fact, its versatility is one of the reasons why it’s heavily used in hot melt adhesives, pressure-sensitive adhesives, sealants, and adhesive tapes.
How to Maximize the Benefits of Resin C5 in Your Production Process
Understanding the key properties of Resin C5 is just the beginning. To fully benefit from this versatile material, here’s how you can integrate it effectively into your production line.
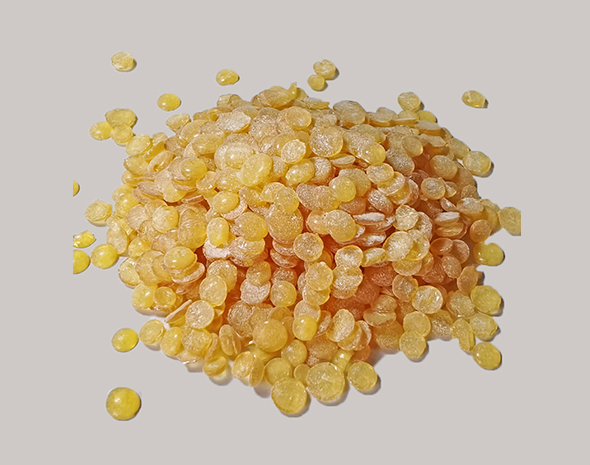
Optimize Resin C5 in Adhesive Formulations
When using Resin C5 in adhesives, whether hot melt or pressure-sensitive varieties, you must pay attention to its softening point. This will affect the bonding strength and the adhesive’s performance at various temperatures. For instance, in applications requiring high temperature resistance, the correct softening point ensures the adhesive stays intact under stress.
For hot melt adhesives, maintaining the proper softening temperature range (95-110°C) ensures the resin melts effectively during application, forming strong and durable bonds once cooled. Additionally, Resin C5’s solubility and compatibility with other materials make it an excellent choice for modifying adhesive formulations, improving tackiness and bonding strength.
Harness Resin C5’s Versatility in Sealants and Tapes
In applications such as sealants and adhesive tapes, Resin C5 can significantly improve the adhesion and durability of the products. For instance, in electrical tapes, where the resin’s chemical stability is critical, Resin C5’s resistance to acids and alkalies ensures that the tape remains functional even in harsh environments.
Furthermore, its UV absorbance properties make it ideal for outdoor sealing applications, protecting against the harmful effects of UV rays and extending the lifespan of the product.
Is Resin C5 Safe to Use in Consumer Goods and Packaging?
With the increasing demand for eco-friendly and non-toxic materials, many industries are turning to safer alternatives for consumer goods. So, is Resin C5 a safe choice for use in products like packaging and consumer goods?
Regulatory Compliance and Safety Considerations
Resin C5, like other hydrocarbon resins, adheres to stringent industry safety standards. It is important to note that different grades of Resin C5 may have varying levels of toxicity and chemical composition. For instance, the A-100 grade typically has low ash content and chemical stability, which means it is safer for applications such as food packaging and medical adhesives.
However, manufacturers must still ensure that the resin is compatible with the specific product and meet the relevant regulatory standards in the countries where they intend to sell their products. The low ash content and minimal impurity levels of A-100 Resin C5 make it particularly well-suited for these applications.
Consumer Safety and Environmental Impact
Another important consideration is the environmental impact of using petroleum-based products. While petroleum-derived resins do pose some challenges in terms of sustainability, Resin C5’s low toxicity and high-performance characteristics make it a viable option for manufacturers aiming to strike a balance between performance and safety.
Applications in Eco-Friendly Packaging
Resin C5 is increasingly being used in eco-friendly packaging solutions, where it helps improve the strength, flexibility, and adhesion of materials. Its light yellow color is also an asset in producing aesthetically pleasing, clear packaging that enhances the overall consumer experience.
Major Applications of Resin C5 in Industry
Now that we’ve explored the properties and safety of Resin C5, let’s take a closer look at the industries that benefit the most from this versatile material.
Paints and Coatings Industry
In the paints and coatings industry, C5 resins are used as binders and modifiers to improve the film-forming properties and adhesion of coatings. The resin enhances the durability of the finish, making it more resistant to abrasion, weathering, and other environmental stressors. Furthermore, Resin C5 is often used in architectural coatings where aesthetics and performance are key.
Rubber Compounding
In rubber compounding, Resin C5 serves as both a reinforcing agent and a tackifier. This contributes to improved adhesion and processing characteristics in rubber products such as tires, hoses, and belts. Resin C5 enhances the tackiness of rubber, ensuring better bonding between the rubber and other materials.
Electrical and Adhesive Tapes
As mentioned earlier, Resin C5 is widely used in adhesive tapes, particularly those with electrical or pressure-sensitive properties. It contributes to improved adhesion and flexibility in products such as electrical insulation tapes, sealing tapes, and adhesive labels.
Troubleshooting Common Issues with Resin C5 in Industrial Applications
While Resin C5 is a highly effective material, it’s not without its challenges in industrial applications. Here are some common issues and how to troubleshoot them:
1. Poor Adhesion
One of the most common issues when working with Resin C5 in adhesives is poor adhesion. This can occur due to improper formulation or incorrect resin selection. Ensure that the softening point and compatibility of the resin align with the application requirements. Additionally, using the correct solvent and additives can improve the bonding properties.
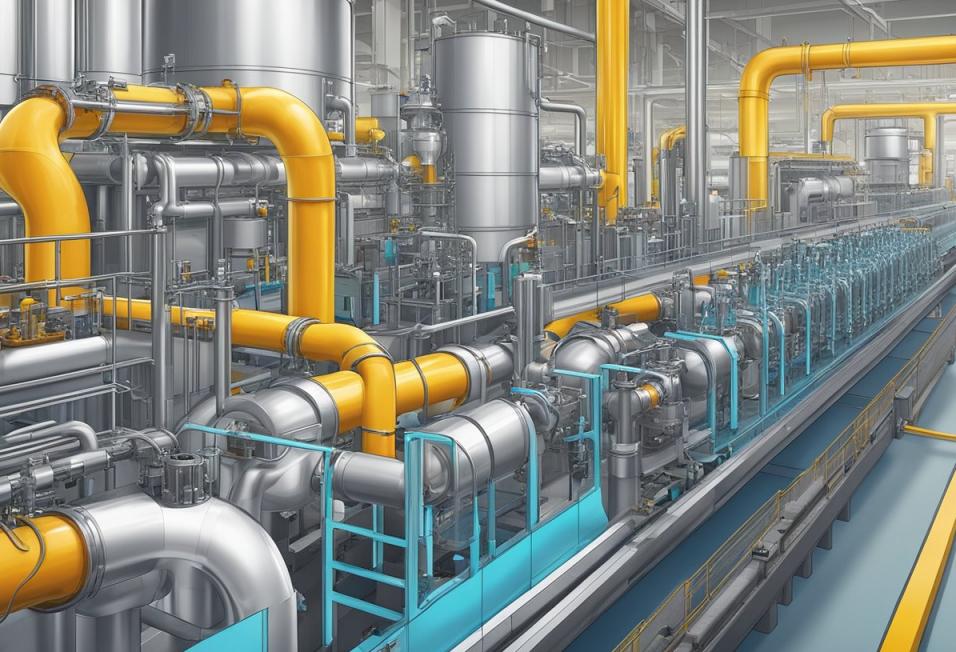
2. Inconsistent Viscosity
If the viscosity of Resin C5 is inconsistent during production, it can lead to problems with coating uniformity or adhesion strength. To solve this, check the temperature and mixing process. Maintaining the correct processing temperature and mixing speed will ensure the resin remains uniform and performs optimally.
3. Degradation Under UV Exposure
Although Resin C5 has good UV absorbance, prolonged exposure to intense UV radiation can still cause degradation. In outdoor applications, consider incorporating UV stabilizers to enhance the resin’s resistance to UV degradation and improve the longevity of the final product.
Conclusion: The Versatility and Benefits of Resin C5
Resin C5 is a powerhouse material in the world of industrial manufacturing. Its remarkable properties, such as chemical stability, compatibility, and excellent adhesion, make it indispensable in adhesives, sealants, coatings, and more. By understanding how to optimize Resin C5 for your production process and addressing common issues, you can unlock its full potential for high-performance, cost-effective solutions.
If you’re looking for a trusted Resin C5 supplier, CHEMBROAD offers high-quality products that can elevate your production standards. With its ability to improve durability, adhesion, and overall product performance, Resin C5 is a material you can rely on for a wide range of applications.