Impact Modifiers for Plastics: Enhanced Durability
20/01/2024
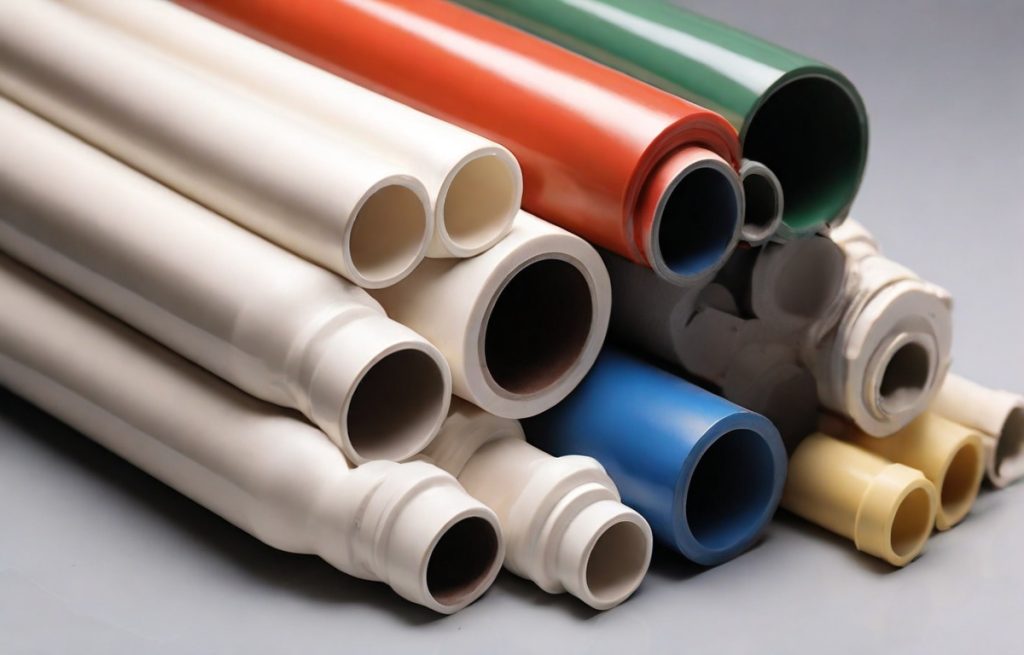
In today’s world, plastic plays a vital role in our daily lives. From packaging to construction, plastic materials are ubiquitous. However, plastic products often have low resistance to impact, which poses a significant challenge for manufacturers. Impact modifiers for plastics, also known as plastic modifying agents or polymer additives for impact resistance, have emerged as a viable solution to this problem. In this article, we will explore the role of impact modifiers in enhancing the durability of plastic products.
Understanding Impact Modification in Polymer Materials
Impact modification in polymer materials is a process of enhancing the impact resistance of plastics by adding specific plastic impact modifier technologies. The aim is to improve the durability of plastic materials and prevent failure caused by a sudden impact or shock.
The science behind impact modification involves altering the mechanical properties of polymers using different plastic impact modifier technologies. These technologies can be categorized into reactive, core-shell, and rubber modifiers.
The selection of an appropriate impact modifier for a specific application depends on several factors, such as the type of polymer, processing conditions, and the desired impact performance. These factors affect the compatibility between the impact modifier and the polymer as well as the effectiveness of the modification.
Understanding the different types of impact modifier technologies and the factors that influence their selection is crucial for the effective application of these additives. By choosing the appropriate plastic impact modifier technologies, manufacturers can enhance the performance and durability of their plastic products, reducing the risk of failure, and improving their overall quality.
Types of Impact Modifiers for Plastics
Impact modifiers are crucial additives that improve the impact resistance and durability of plastic products. Different types of impact modifiers are available, each with unique properties and benefits. This section explores some of the most popular impact modifier categories used in plastics and their benefits.
Rubber Modifiers
Rubber modifiers are rubber-based impact modifiers that enhance the flexibility and toughness of plastics, making them more resistant to impact and cracking. These modifiers are compatible with a wide range of plastic resins, including polypropylene, polyethylene, and polystyrene.
Core-Shell Modifiers
Core-shell modifiers are impact modifiers made from a blend of rubber and hard polymer, designed to provide a balance of strength, toughness, and stiffness. They have a hard outer shell that provides structural support while the elastic core absorbs and disperses impact energy.
Reactive Modifiers
Reactive modifiers are designed to chemically bond with the plastic matrix, improving compatibility and enhancing impact resistance. They often consist of maleic anhydride or acrylic acid functionality, which chemically reacts with the plastic resin to form stronger linkages.
Plastic Strengthening Additives
In addition to impact modifiers, there are also plastic strengthening additives that improve the mechanical properties of plastic materials. These can include fillers like glass beads or fibers, or reinforcing agents like carbon black or nanoclays. They improve strength, stiffness, and thermal stability, making the plastic material more resistant to deformation and failure.
Understanding the various impact modifier options available is crucial for selecting the appropriate additive for a specific plastic application. Each impact modifier category has unique benefits, making it important to carefully consider the desired impact performance, plastic resin, and other requirements when making a selection.
Benefits of Impact Modifiers in Plastics
Impact modifiers can greatly enhance the durability of plastic products by improving their resistance to impact and preventing cracking or breaking. These additives increase the toughness of plastics by absorbing energy during deformation, which helps the polymer to withstand the stress of impact. This makes plastic products more reliable and long-lasting, reducing the need for frequent replacements and repairs.
The use of impact modifiers also enhances the overall performance of plastic materials. By improving the resistance to impact, these additives can reduce the risk of damage during transportation, installation, and use. This makes plastic products more attractive to consumers, who are often seeking products that can withstand wear and tear over time.
The benefits of impact modifiers go beyond just enhancing the durability of plastic products. They can also improve the processability of plastics, making it easier to manufacture and shape these materials into complex components. Additionally, the use of impact modifiers can yield cost savings by reducing the need for expensive reinforcing fillers or thicker plastic walls to achieve the desired performance.
Overall, the use of impact modifiers provides additive solutions for enhancing plastic durability and furthering the advancement of impact-resistant plastic products for a wide range of industries.
Applications of Impact Modifiers in Different Industries
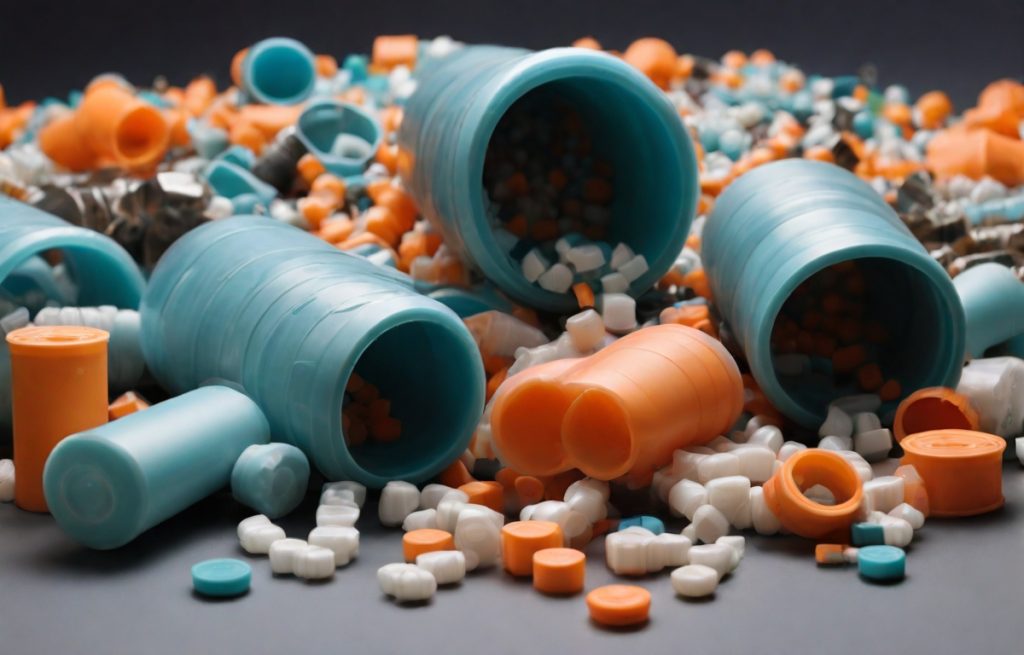
Impact modifiers offer additive solutions for enhancing the impact resistance of plastics. These modifying agents are being used widely across numerous industries to improve the performance and durability of plastic products.
Automotive Industry
The automotive industry is a leading adopter of impact modifiers for plastics. These modifiers are used extensively in a wide range of automotive applications, including dashboards, bumpers, door panels, and exterior moldings.
Construction Industry
Impact modifiers have various applications in the construction industry, where they are used to enhance durability in plastic pipes, window frames, floor tiles, and insulation materials.
Packaging Industry
Impact modifiers are used in packaging applications that require resistance to impact and tearing. These modifiers are used for food packaging, beverage bottles, and various consumer goods packaging.
Consumer Goods Industry
The consumer goods industry uses impact modifiers for plastics in a range of products, from household appliances to toys. These modifiers enable product designs with the required specifications for strength, toughness, and durability.
With such a wide range of practical applications, it is clear that impact modifiers for plastics play a significant role in enhancing the performance and longevity of plastic materials. Industries across the board will continue to depend on these additives for improved product quality and reliability.
Choosing the Right Impact Modifier for Your Application
When it comes to selecting the appropriate impact modifier for your application, there are several key factors to consider. Firstly, the type of plastic material being used plays a crucial role in determining the impact modifier that can be used. For example, polyvinyl chloride (PVC) and polyethylene (PE) require different types of impact modifiers to achieve optimum impact performance.
Secondly, the desired impact performance is another important consideration. The impact modifier selected should align with the specific impact resistance requirements for the intended application. This can vary greatly depending on the industry, for example, the automotive industry has a higher level of impact resistance requirements than the construction industry.
Processing conditions, such as the temperature and shear rate, can also impact the selection of impact modifiers. Some modifiers may not perform well under certain processing conditions, and it’s crucial to select an impact modifier that can withstand the processing parameters.
Regulatory requirements are also important in the selection process. The impact modifier chosen must comply with applicable industry regulations and standards.
Testing is an essential part of the selection process to determine the effectiveness of the chosen impact modifier. Standard testing methods such as Izod or Charpy impact tests can be used to evaluate impact performance. By considering these key factors and executing proper testing, you can choose the appropriate impact modifier to improve the impact performance of your plastic products.
Future Trends in Plastic Impact Modifier Technologies
The science of plastic impact modification is continually evolving, with new products and technologies being developed to meet the changing needs of manufacturers across different industries. Innovative approaches to impact resistance in polymers are constantly being explored to enhance the durability of plastic products.
One of the key trends in plastic impact modifier technologies is the development of eco-friendly and sustainable solutions. As the focus on environmental conservation and sustainability increases, manufacturers are looking for ways to reduce their environmental footprint and enhance the sustainability of their products. This has led to the development of biodegradable impact modifiers that can be used in a range of applications without contributing significantly to environmental degradation.
Another key trend is the development of multi-functional impact modifiers that not only enhance impact resistance but also offer additional benefits such as UV stabilization, flame retardancy, and antimicrobial properties. These multi-functional modifiers can help manufacturers save space, reduce costs, and simplify their production processes.
Advanced processing technologies are also being developed to improve the dispersion of impact modifiers in polymers, resulting in better impact resistance and overall performance. Emerging technologies such as reactive extrusion and nanocomposites are being explored to create high-performance polymer blends.
Overall, the future of plastic impact modifier technologies is focused on creating solutions that are not only effective but also sustainable, efficient, and cost-effective. This will require continued research and collaboration across different fields to develop the most innovative and effective products for different industries.
Case Studies: Real-World Impact Modifier Applications
This section provides an in-depth look at the practical applications of impact modifiers in enhancing plastic durability and improving impact performance. Through real-world case studies, we will showcase specific examples of successful outcomes achieved through the use of appropriate impact modifiers.
CASE STUDY 1: Automotive Industry
One of the biggest challenges in the automotive industry is to develop more lightweight and fuel-efficient vehicles without compromising safety and performance. In this case study, we examine how a leading car manufacturer improved the impact performance of a critical plastic component by incorporating an innovative core-shell impact modifier. The result: a 20% reduction in part weight, while maintaining the same level of impact resistance and durability, reducing costs and environmental impact.
CASE STUDY 2: Construction Industry
In the construction industry, plastic pipes and fittings need to withstand various impacts and stresses. In this case study, we explore how a construction company solved the problem of brittle and failure-prone PVC pipes by incorporating a unique blend of plastic additives for improved impact performance. The result: an 80% reduction in pipe failure rates during installation and use, saving time and money for both the installer and the end-user.
CASE STUDY 3: Consumer Goods Industry
The consumer goods industry is always looking for ways to improve the performance and durability of household items. In this case study, we take a close look at how a major manufacturer of kitchen appliances used a specialized rubber impact modifier to improve the toughness and scratch resistance of its plastic parts. The result: a 30% improvement in the durability of the appliance, increased customer satisfaction and a competitive edge in the market.
These real-world examples demonstrate the significant impact that appropriate impact modifiers can have on enhancing plastic durability and improving impact performance across diverse applications and industries. By selecting the right materials and additives, manufacturers can achieve higher quality and performance in their plastic products, while reducing costs, enhancing sustainability, and meeting regulatory requirements.
Conclusion
Impact modifiers for plastics are highly beneficial in enhancing the durability and impact resistance of plastic products. The use of plastic strengthening additives can prevent cracking or breaking and improve overall performance, longevity, and customer satisfaction.
It is important to select the appropriate impact modifier based on specific requirements, such as the type of plastic, desired impact performance, processing conditions, and regulatory requirements. The effectiveness of impact modifiers can be evaluated through testing methods.
The future of impact modifier technologies is promising, with innovations and sustainability becoming significant factors in research and development. Real-world case studies demonstrate the practical applications of impact modifiers across various industries, such as automotive, construction, packaging, and consumer goods.
In conclusion, additive solutions for impact resistance in plastics, such as impact modifiers, are essential for the manufacturing of high-quality plastic products. With careful selection, application, and testing, the use of plastic additives for improved impact performance can lead to enhanced plastic durability, which benefits both manufacturers and consumers.
FAQ
What are impact modifiers for plastics?
Impact modifiers are additives that are incorporated into plastic formulations to enhance the impact resistance and durability of plastic materials. These modifiers help to prevent cracking, breaking, or deformation of plastic products when subjected to impact or stress.
How do impact modifiers improve the durability of plastics?
Impact modifiers improve the durability of plastics by increasing their resistance to impact and improving their ability to withstand external forces. These additives enhance the toughness of plastic materials, making them less prone to fractures, fractures, or failure under impact or stress conditions.
What types of impact modifiers are available for plastics?
There are various types of impact modifiers available for plastics. Some common types include rubber modifiers, core-shell modifiers, and reactive modifiers. Each type of impact modifier has different properties and is suitable for specific plastic applications.
What are the benefits of using impact modifiers in plastics?
Using impact modifiers in plastics offers several benefits. These additives enhance the impact resistance and toughness of plastic materials, preventing them from cracking or breaking under external forces. Impact modifiers also improve the overall performance and longevity of plastic products, making them suitable for demanding applications.
In which industries are impact modifiers used?
Impact modifiers are used in a wide range of industries. They are commonly used in the automotive industry for the production of impact-resistant bumpers and interior components. Impact modifiers are also used in the construction industry for durable plastic pipes, roofing materials, and siding. Additionally, they find applications in packaging, consumer goods, and many other sectors where impact resistance is crucial.
How do I choose the right impact modifier for my plastic application?
Choosing the right impact modifier for your plastic application requires considering several factors. These include the type of plastic, desired impact performance, processing conditions, and regulatory requirements. It is advisable to consult with experts or manufacturers to determine the most suitable impact modifier for your specific needs.
What are the future trends in impact modifier technologies?
The future of impact modifier technologies is focused on developing more advanced and sustainable solutions. This includes the development of new additives and innovative approaches to enhance impact resistance in plastics. There is also an increasing emphasis on eco-friendly solutions and the use of renewable materials in impact modifier research and development.
Can you provide examples of real-world impact modifier applications?
Certainly! Real-world impact modifier applications include the use of these additives in automotive bumpers to improve impact resistance, in packaging materials to prevent damage to fragile contents, and in outdoor furniture to enhance durability. These examples demonstrate the practical applications of impact modifiers in enhancing plastic durability and improving impact performance.