C5 Aliphatic Hydrocarbon Resin: Properties and Applications
19/01/2024
C5 aliphatic hydrocarbon resin is a type of petroleum-derived resin that is widely used in the manufacturing of adhesives, coatings, and printing inks. It is a thermoplastic resin that is formed by the polymerization of aliphatic olefins, such as pentene and hexene. The resin has a low molecular weight and a narrow molecular weight distribution, which gives it excellent solubility and compatibility with other materials.
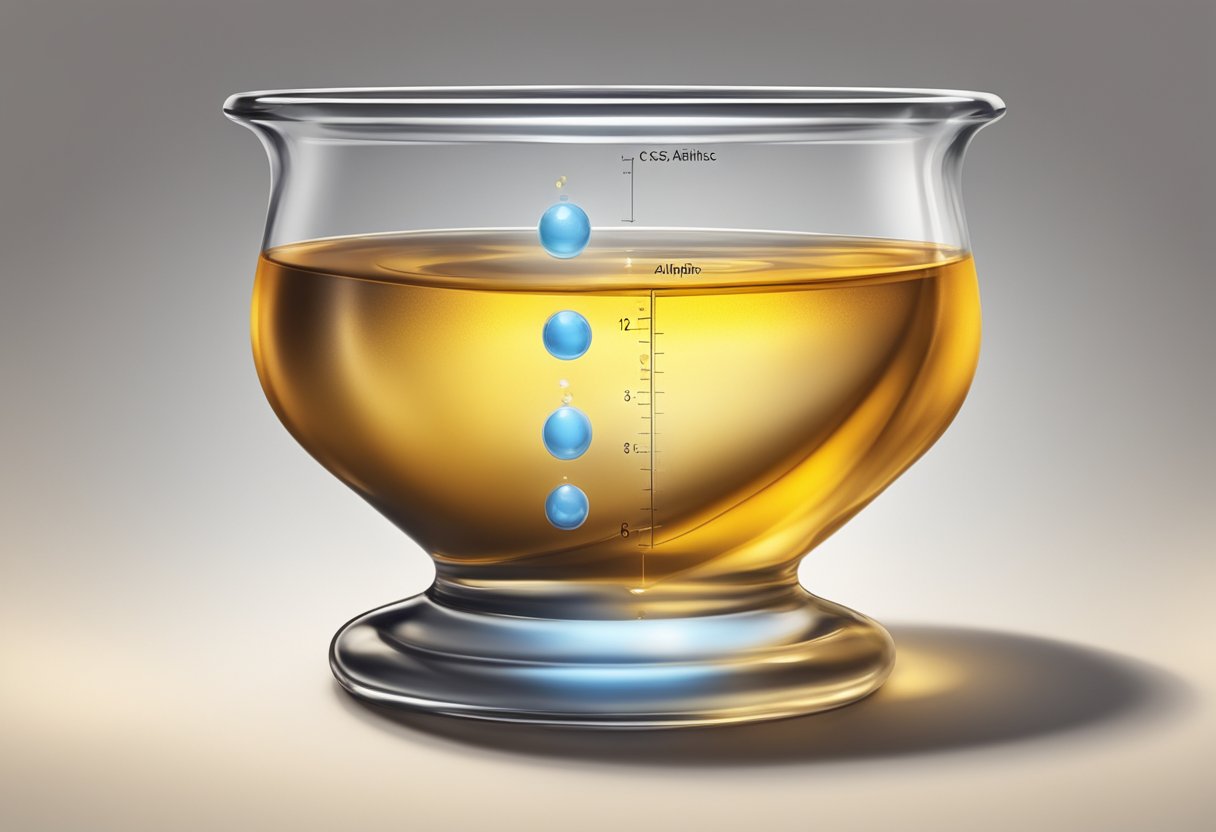
One of the primary benefits of chemborad C5 aliphatic hydrocarbon resin is its ability to improve the performance of adhesives and coatings. The resin can enhance the tackiness, adhesion, and cohesion of these materials, making them more effective in bonding and sealing applications. Additionally, C5 aliphatic hydrocarbon resin can improve the durability and weather resistance of coatings, making them suitable for use in harsh environments.
Another advantage of C5 aliphatic hydrocarbon resin is its versatility. It can be used in a wide range of applications, including hot melt adhesives, pressure-sensitive adhesives, solvent-based coatings, and printing inks. The resin is also compatible with a variety of other materials, such as waxes, oils, and polymers, which allows for the creation of customized formulations that meet specific performance requirements.
Chemical Structure of C5 Aliphatic Hydrocarbon Resin
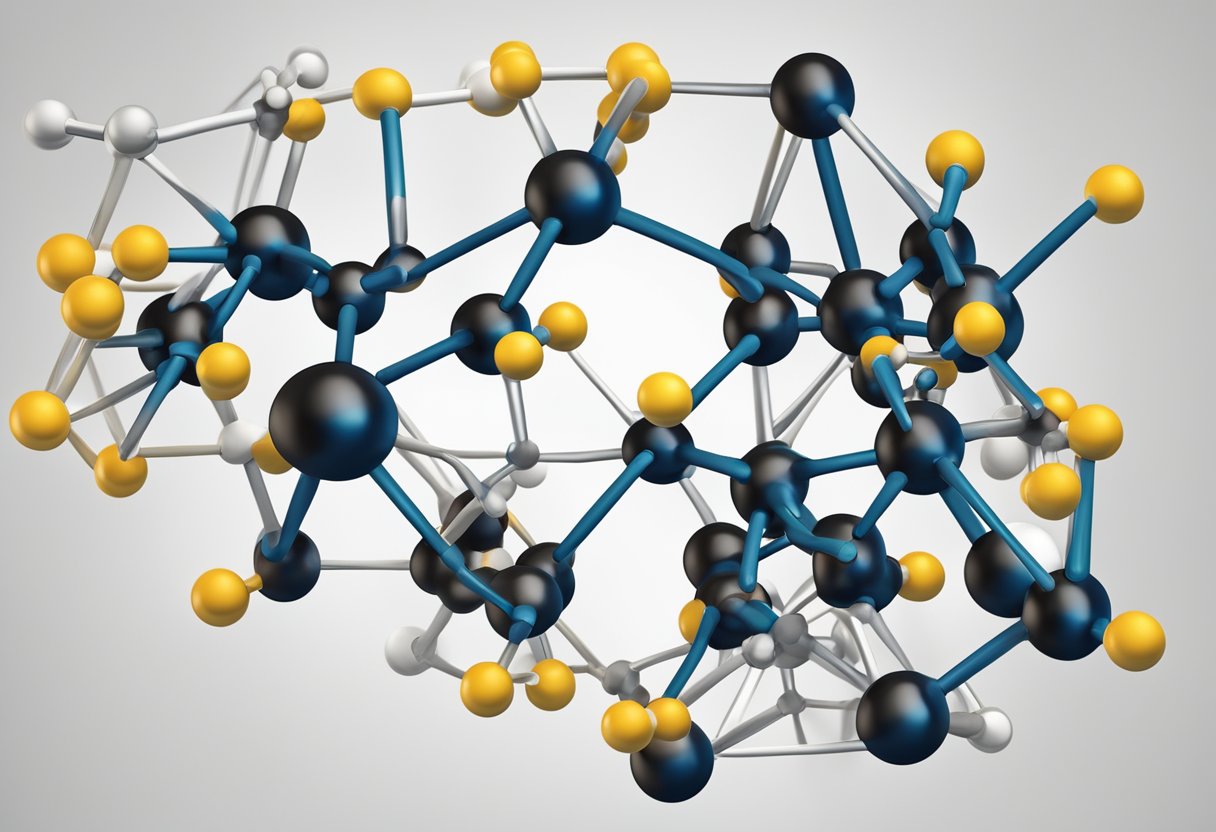
C5 aliphatic hydrocarbon resin is a type of hydrocarbon resin that is derived from the polymerization of aliphatic monomers. These monomers are typically derived from the distillation of crude oil, and they are characterized by their high levels of unsaturation. The resulting resin is a highly viscous liquid or solid that is used in a variety of applications, including adhesives, coatings, and printing inks.
The chemical structure of C5 aliphatic hydrocarbon resin is primarily composed of branched and linear hydrocarbons that contain between 5 and 6 carbon atoms. The exact composition of the resin can vary depending on the source of the monomers and the manufacturing process used to produce the resin. However, in general, C5 aliphatic hydrocarbon resin is composed of a mixture of isoprene, piperylene, and other aliphatic monomers.
The resin is characterized by its high levels of unsaturation, which is due to the presence of double bonds in the hydrocarbon chains. These double bonds make the resin highly reactive, which is why it is often used in applications where adhesion and bonding properties are important. The unsaturated nature of the resin also makes it susceptible to oxidation, which can lead to changes in its physical and chemical properties over time.
In summary, C5 aliphatic hydrocarbon resin is a highly versatile material that is widely used in many different applications. Its chemical structure is primarily composed of branched and linear hydrocarbons that contain between 5 and 6 carbon atoms, and it is characterized by its high levels of unsaturation.
Manufacturing Process
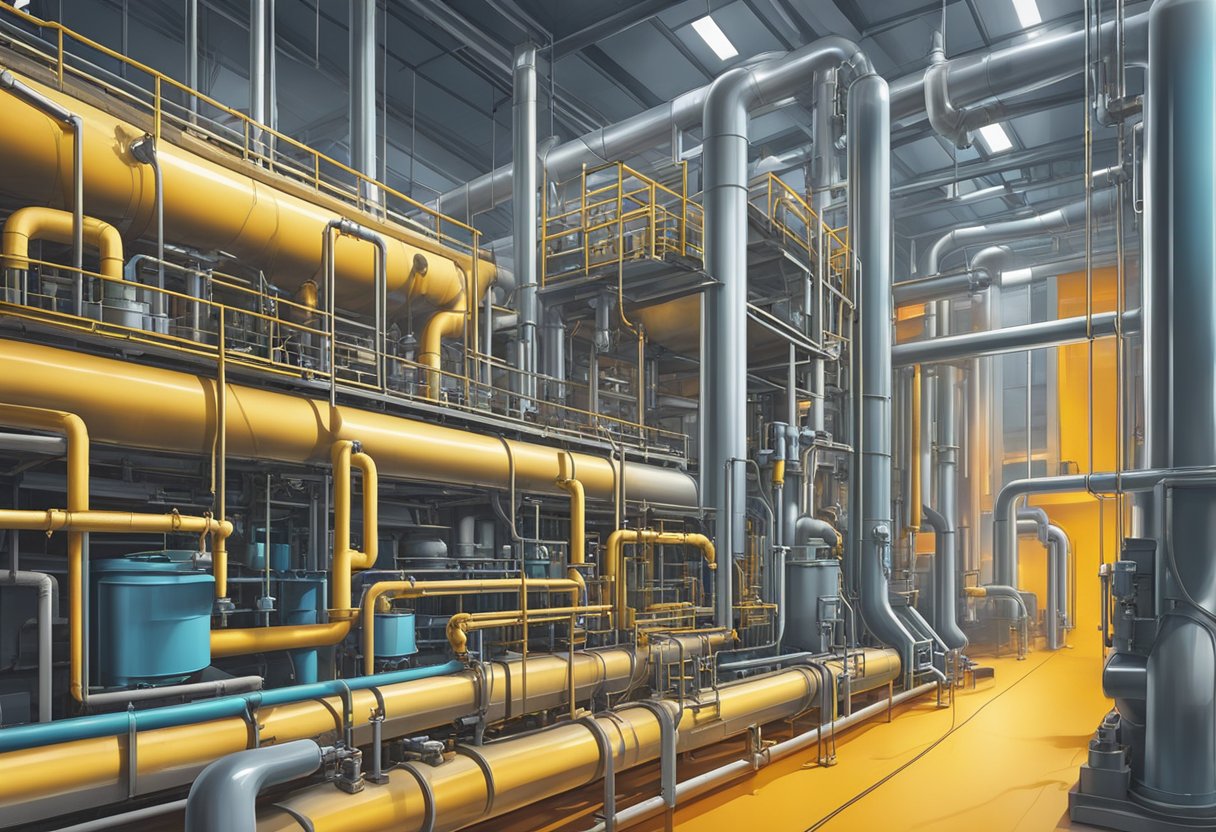
C5 aliphatic hydrocarbon resin is produced through the polymerization of C5 fraction derived from naphtha cracking. The process involves several steps, including distillation, polymerization, and finishing.
During the distillation process, C5 fraction is separated from other fractions obtained from naphtha cracking. This fraction is then subjected to polymerization, which involves the addition of a catalyst and a stabilizer. The polymerization process is carried out under controlled conditions of temperature and pressure.
After polymerization, the resulting resin is subjected to finishing, which involves the removal of unreacted monomers and other impurities. The finished resin is then tested for its physical and chemical properties to ensure that it meets the required specifications.
The manufacturing process of C5 aliphatic hydrocarbon resin is highly controlled and monitored to ensure consistent quality and properties of the final product. The use of advanced technology and equipment has enabled manufacturers to produce high-quality resins with excellent performance characteristics.
Overall, the manufacturing process of C5 aliphatic hydrocarbon resin is a complex and precise process that requires specialized knowledge and expertise. The resulting resin is a versatile and valuable material that finds applications in a wide range of industries, including adhesives, coatings, and printing inks.
Properties and Specifications

C5 aliphatic hydrocarbon resin is a type of thermoplastic resin that is widely used in various industries due to its unique properties and specifications. Here are some of the key characteristics of this resin:
- Color: C5 aliphatic hydrocarbon resin is typically light yellow to amber in color.
- Odor: It has a mild, resinous odor.
- Softening point: The softening point of C5 aliphatic hydrocarbon resin ranges from 90°C to 120°C, depending on the specific type and grade of the resin.
- Molecular weight: The molecular weight of C5 aliphatic hydrocarbon resin ranges from 500 to 3000 g/mol.
- Viscosity: The viscosity of this resin is relatively low, ranging from 100 to 1000 mPa·s at 25°C.
- Solubility: C5 aliphatic hydrocarbon resin is soluble in a wide range of solvents, including aliphatic and aromatic hydrocarbons, esters, ketones, and chlorinated solvents.
- Compatibility: This resin is compatible with a wide range of other polymers and resins, including polyethylene, polypropylene, styrene-butadiene rubber, and polyvinyl chloride.
C5 aliphatic hydrocarbon resin is known for its excellent tackifying and adhesion properties, which make it a popular choice for use in adhesives, coatings, and inks. It is also used as a modifier for other resins to improve their performance and properties. Due to its unique combination of properties, C5 aliphatic hydrocarbon resin is a versatile and valuable material for many different applications.
Applications in Industry
C5 aliphatic hydrocarbon resin is widely used in various industries due to its excellent properties such as good compatibility, low odor, and good thermal stability. Here are some common applications of C5 aliphatic hydrocarbon resin in industry:
Adhesives
C5 aliphatic hydrocarbon resin is widely used in the adhesive industry as a tackifier. It helps to improve the adhesion properties of the adhesive and provides excellent adhesion to various substrates such as wood, metal, and plastic. It also improves the cohesion of the adhesive, which results in better bonding strength.
Rubber
C5 aliphatic hydrocarbon resin is commonly used in the rubber industry as a processing aid and tackifier. It helps to improve the processing properties of rubber compounds and provides good tackiness to the rubber. It also improves the adhesion properties of the rubber to various substrates.
Paints and Coatings
C5 aliphatic hydrocarbon resin is also used in the paints and coatings industry as a binder and film former. It helps to improve the gloss and hardness of the coating and provides good adhesion to various substrates. It also improves the weatherability and chemical resistance of the coating.
Printing Inks
C5 aliphatic hydrocarbon resin is commonly used in the printing ink industry as a resin modifier and tackifier. It helps to improve the adhesion properties of the ink to various substrates and provides good tackiness to the ink. It also improves the gloss and printability of the ink.
Overall, C5 aliphatic hydrocarbon resin is a versatile material that finds applications in various industries. Its excellent properties make it a preferred choice for many applications.
Market Overview
C5 aliphatic hydrocarbon resin is a type of resin that is widely used in various industries such as adhesives, coatings, and printing inks. The resin is derived from petroleum and is known for its excellent compatibility with a wide range of polymers.
The market for C5 aliphatic hydrocarbon resin is expected to grow steadily in the coming years, driven by the increasing demand for adhesives and coatings in various industries. The resin is known for its excellent properties such as good tack, high softening point, and excellent compatibility with other materials.
The demand for C5 aliphatic hydrocarbon resin is also expected to be driven by the growth of the packaging industry. The resin is widely used in the production of packaging materials such as tapes, labels, and laminates. The increasing demand for packaged goods in emerging economies is expected to drive the growth of the packaging industry, which in turn will boost the demand for C5 aliphatic hydrocarbon resin.
In addition, the increasing demand for environmentally friendly products is also expected to drive the growth of the C5 aliphatic hydrocarbon resin market. The resin is known for its low toxicity and low VOC emissions, making it an attractive alternative to other types of resins.
Overall, the market for C5 aliphatic hydrocarbon resin is expected to grow at a steady pace in the coming years, driven by the increasing demand for adhesives, coatings, and packaging materials.
Environmental Impact and Safety
C5 aliphatic hydrocarbon resin is a petroleum-derived product that is widely used in various industrial applications. While it provides excellent properties such as adhesion, flexibility, and thermal stability, its production and use can have some environmental and safety implications.
Environmental Impact
The production of C5 aliphatic hydrocarbon resin involves the use of crude oil, which is a non-renewable resource. The extraction, transportation, and processing of crude oil can result in significant greenhouse gas emissions, air pollution, and water pollution. However, some manufacturers have implemented sustainable practices to minimize their environmental impact and reduce their carbon footprint.
When C5 aliphatic hydrocarbon resin is used in products such as adhesives, coatings, and inks, it can potentially contribute to indoor and outdoor air pollution. This is because the resin can release volatile organic compounds (VOCs) during its application and curing process. However, some manufacturers have developed low-VOC or VOC-free formulations to address this issue.
Safety
C5 aliphatic hydrocarbon resin is generally considered safe when handled and used properly. However, it can pose some health and safety risks if not handled with care. The resin is flammable and can ignite if exposed to a spark or flame. Therefore, it should be stored and handled away from sources of ignition.
In addition, the resin can cause skin and eye irritation if it comes into contact with the skin or eyes. Therefore, it is recommended to wear appropriate personal protective equipment (PPE) such as gloves and goggles when handling the resin.
Overall, while C5 aliphatic hydrocarbon resin has some environmental and safety implications, its benefits and applications make it a valuable product in various industries. Manufacturers and users should take appropriate measures to minimize their environmental impact and ensure safe handling and use of the resin.
Quality Control and Standards
C5 aliphatic hydrocarbon resins are widely used in various industries, such as adhesives, coatings, and rubber. To ensure the quality of these resins, strict quality control measures and standards are implemented throughout the production process.
The raw materials used to produce C5 resins are carefully selected and tested to ensure their purity and consistency. The manufacturing process is closely monitored to ensure that the resin is produced according to the desired specifications. Quality control tests are conducted at various stages of the production process to ensure that the resin meets the required standards.
One of the most important quality control measures for C5 resins is the softening point test. This test determines the temperature at which the resin softens and becomes tacky. The softening point is a critical parameter that affects the performance of the resin in various applications. Other quality control tests include color, acid value, and ash content.
To ensure that C5 resins meet the required standards, various industry organizations have established standards and guidelines for the production and use of these resins. For example, the American Society for Testing and Materials (ASTM) has established standards for the softening point, color, and other properties of C5 resins.
In addition, manufacturers of C5 resins often have their own internal quality control standards and procedures to ensure that their products meet the highest quality standards. These standards and procedures may include regular testing of raw materials, monitoring of production processes, and testing of finished products.
Overall, the quality control measures and standards for C5 aliphatic hydrocarbon resins ensure that these products meet the required specifications and perform optimally in various applications.
Storage and Handling
C5 aliphatic hydrocarbon resin is a valuable ingredient in various industrial applications. Proper storage and handling of this resin are crucial to maintain its quality and extend its shelf life. Here are some guidelines for storing and handling aliphatic hydrocarbon resin:
Storage
- Store aliphatic hydrocarbon resin in a cool, dry, and well-ventilated place. The ideal temperature range for storage is between 0°C and 30°C.
- Keep the resin away from direct sunlight, heat sources, and open flames.
- Store the resin in its original packaging or in airtight containers to prevent contamination and moisture absorption.
- Avoid stacking heavy objects on top of the resin to prevent deformation or damage to the packaging.
Handling
- Wear appropriate personal protective equipment, such as gloves and safety glasses, when handling aliphatic hydrocarbon resin.
- Avoid inhaling or ingesting the resin, as it may cause irritation or health hazards.
- Use clean and dry tools and equipment when handling the resin to prevent contamination.
- Do not mix different types of resins or additives unless specified by the manufacturer.
- Follow the recommended dosage and mixing instructions to achieve the desired performance and avoid waste.
By following these storage and handling guidelines, users can ensure that aliphatic hydrocarbon resin remains in optimal condition and performs consistently in their applications.
Future Trends and Developments
The global demand for c5 aliphatics hydrocarbon resin is expected to grow significantly in the coming years. The resin is widely used in the adhesive, coatings, and printing ink industries. The market is expected to witness growth due to the increasing demand for adhesives and coatings in the construction, automotive, and packaging industries.
Manufacturers are investing in research and development to improve the properties of c5 aliphatic hydrocarbon resins. They are focusing on developing resins with better thermal stability, compatibility, and adhesion properties. The development of bio-based c5 aliphatics hydrocarbon resin is also gaining traction due to the increasing demand for sustainable products.
The growing demand for low VOC (volatile organic compound) products is expected to drive the demand for c5 aliphatic hydrocarbon resins in the future. The resin is known for its low VOC emissions and is a preferred choice for environmentally conscious consumers.
In addition, the Asia-Pacific region is expected to witness significant growth in the c5 aliphatic hydrocarbon resins market due to the increasing demand for adhesives and coatings in the construction and automotive industries. The region is also witnessing rapid industrialization, which is expected to further boost the demand for aliphatic hydrocarbon resin.
Overall, the future of the aliphatic hydrocarbon resins market looks promising, with increasing demand from various industries and ongoing research and development efforts to improve the properties of the resin.
Challenges and Opportunities
C5 aliphatic hydrocarbon resin is a versatile material that finds application in various industries. However, there are some challenges that need to be addressed to fully realize the potential of this resin.
One of the major challenges is the fluctuating prices of raw materials. The prices of crude oil, which is the primary raw material used in the production of C5 aliphatic hydrocarbon resins, are highly volatile. This makes it difficult for manufacturers to predict the cost of production, which in turn affects the pricing of the final product.
Another challenge is the increasing competition from substitutes such as C9 resins and rosin esters. These materials offer similar properties and are available at a lower cost, which makes them a preferred choice for some applications.
Despite these challenges, there are several opportunities for the growth of the C5 aliphatic hydrocarbon resins market. The increasing demand for adhesives and sealants in the construction and automotive industries is expected to drive the demand for C5 resins. Additionally, the growing demand for printing inks, coatings, and paints is expected to boost the demand for C5 resins in the coming years.
Moreover, the development of bio-based C5 aliphatics hydrocarbon resin is expected to open up new opportunities for the market. Bio-based resins are eco-friendly and sustainable, which makes them a preferred choice for environmentally conscious consumers.
In conclusion, while there are challenges that need to be addressed, the C5 aliphatics hydrocarbon resin market offers several opportunities for growth. Manufacturers need to focus on developing sustainable and cost-effective solutions to meet the growing demand for this versatile material.