Synthetic Polyisoprene Rubber: Properties and Applications
19/01/2024
Synthetic polyisoprene rubber is a type of elastomer that is widely used in various industrial applications. It is a synthetic version of natural rubber, which is derived from the sap of rubber trees. Synthetic polyisoprene rubber is made by polymerizing isoprene monomers, which are derived from petroleum. It has similar properties to natural rubber, but it is more consistent in quality and has better resistance to aging and weathering.
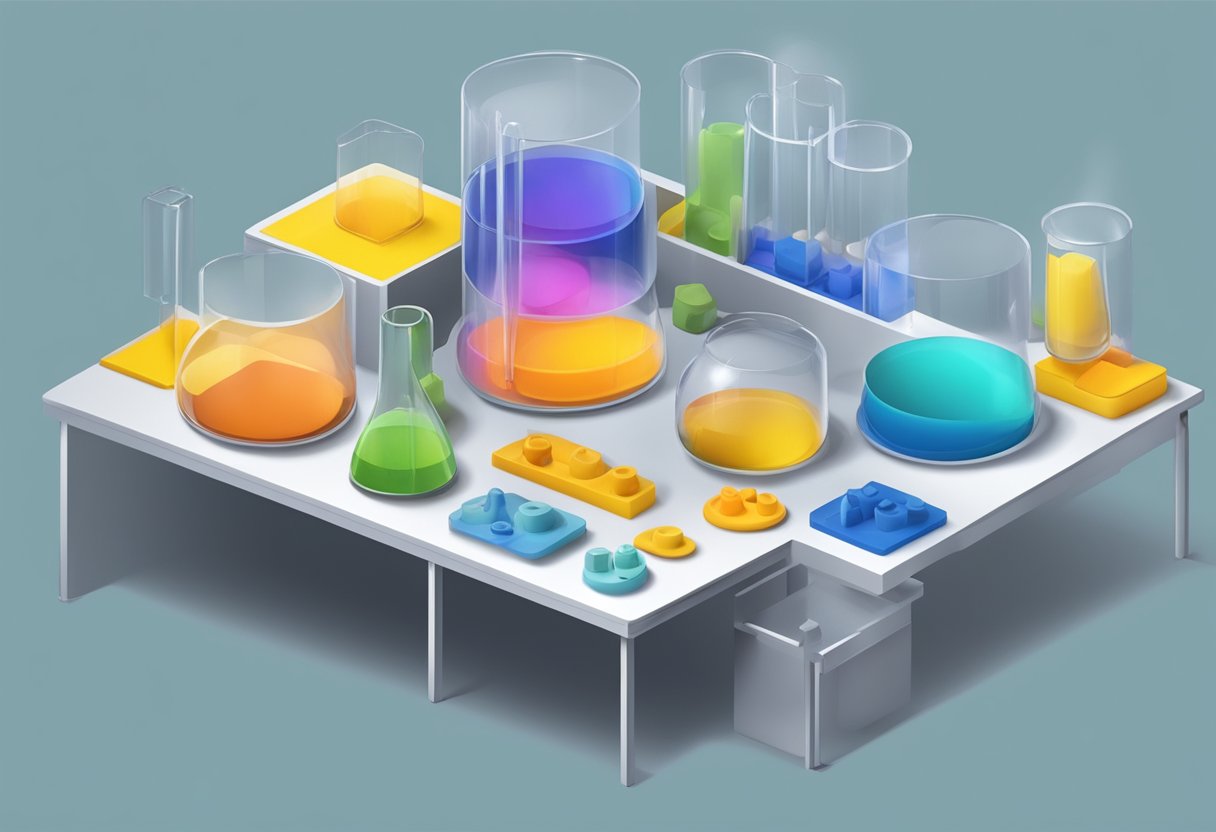
One of the main advantages of synthetic polyisoprene rubber is its high degree of purity and consistency. Unlike natural rubber, which can vary in quality depending on the source and processing method, synthetic polyisoprene rubber is manufactured under controlled conditions, resulting in a more uniform product. This makes it ideal for use in applications that require precise and consistent performance, such as medical devices, automotive parts, and consumer goods.
Another advantage of synthetic polyisoprene rubber is its superior resistance to aging and weathering. Natural rubber tends to degrade over time when exposed to heat, light, and oxygen, which can affect its mechanical properties and lead to cracking and degradation. Synthetic polyisoprene rubber, on the other hand, is more resistant to these environmental factors, which makes it a more durable and long-lasting material.
Chemical Structure of Synthetic Polyisoprene
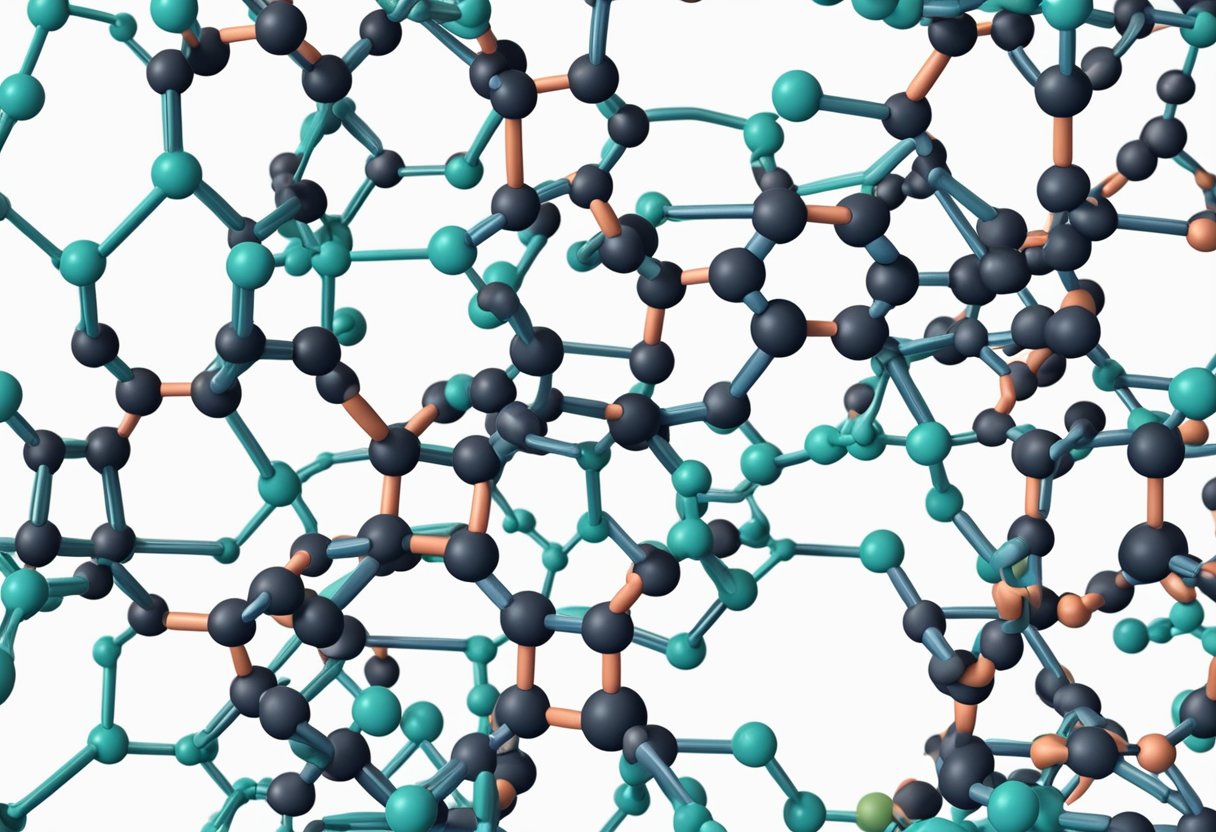
Synthetic polyisoprene rubber is a pbt polymer made from the monomer isoprene through polymerization. Isoprene is a five-carbon molecule with a double bond that allows it to polymerize into long chains. The chemical structure of synthetic polyisoprene is similar to that of natural rubber, which is also made from isoprene monomers.
The repeating unit of synthetic polyisoprene is shown below:
As can be seen from the above image, synthetic polyisoprene has a linear structure with a double bond in each repeating unit. The double bonds in the polymer chain are responsible for the elastic properties of the material.
To improve the properties of synthetic polyisoprene, various modifications are made to the chemical structure. For example, the introduction of side chains or cross-linking can improve the strength and durability of the material. Additionally, modifications can be made to the molecular weight and distribution of the polymer to tailor its properties for specific applications.
Overall, the chemical structure of synthetic polyisoprene is similar to that of natural rubber, but with modifications to improve its properties for various applications.
Production Process
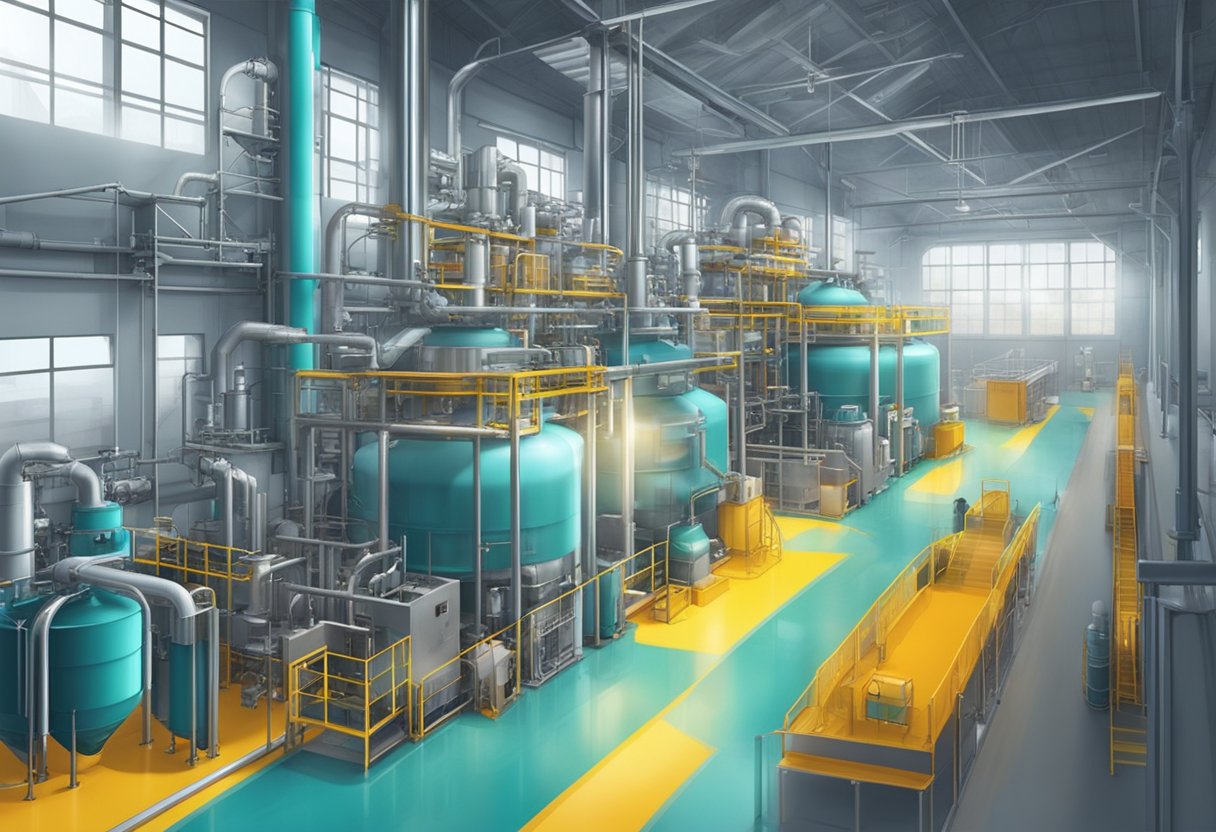
Raw Material Sourcing
The production of synthetic polyisoprene rubber begins with the sourcing of raw materials. The main raw material used in the production process is isoprene, which is derived from petroleum. Other additives such as catalysts, stabilizers, and antioxidants are also sourced during this stage. It is important to ensure that the raw materials used are of high quality to achieve a high-quality end product.
Polymerization Techniques
Polymerization is the process by which isoprene molecules are linked together to form long chains of polyisoprene. There are two primary polymerization techniques used in the production of synthetic polyisoprene rubber: solution polymerization and emulsion polymerization.
In solution polymerization, isoprene is dissolved in a solvent and a catalyst is added to initiate the polymerization process. The resulting polyisoprene is then precipitated out of the solution and washed to remove any impurities.
In emulsion polymerization, isoprene is dispersed in an aqueous solution along with a surfactant to form tiny droplets. A catalyst is then added to initiate the polymerization process, resulting in the formation of polyisoprene particles suspended in the aqueous solution. The particles are then coagulated and washed to remove any impurities.
Post-Polymerization Treatments
After the polymerization process, the polyisoprene rubber is subjected to post-polymerization treatments to improve its physical and chemical properties. These treatments include drying, milling, and vulcanization.
During the drying process, the polyisoprene rubber is dried to remove any residual solvent or water. The milling process involves grinding the polyisoprene rubber into a fine powder, which is then used as a raw material in the production of various rubber products.
Vulcanization is the final step in the production process, during which the polyisoprene rubber is heated with sulfur to cross-link the polymer chains and improve its strength, durability, and elasticity. The resulting product is a high-quality synthetic polyisoprene rubber that can be used in a wide range of applications.
Properties and Characteristics
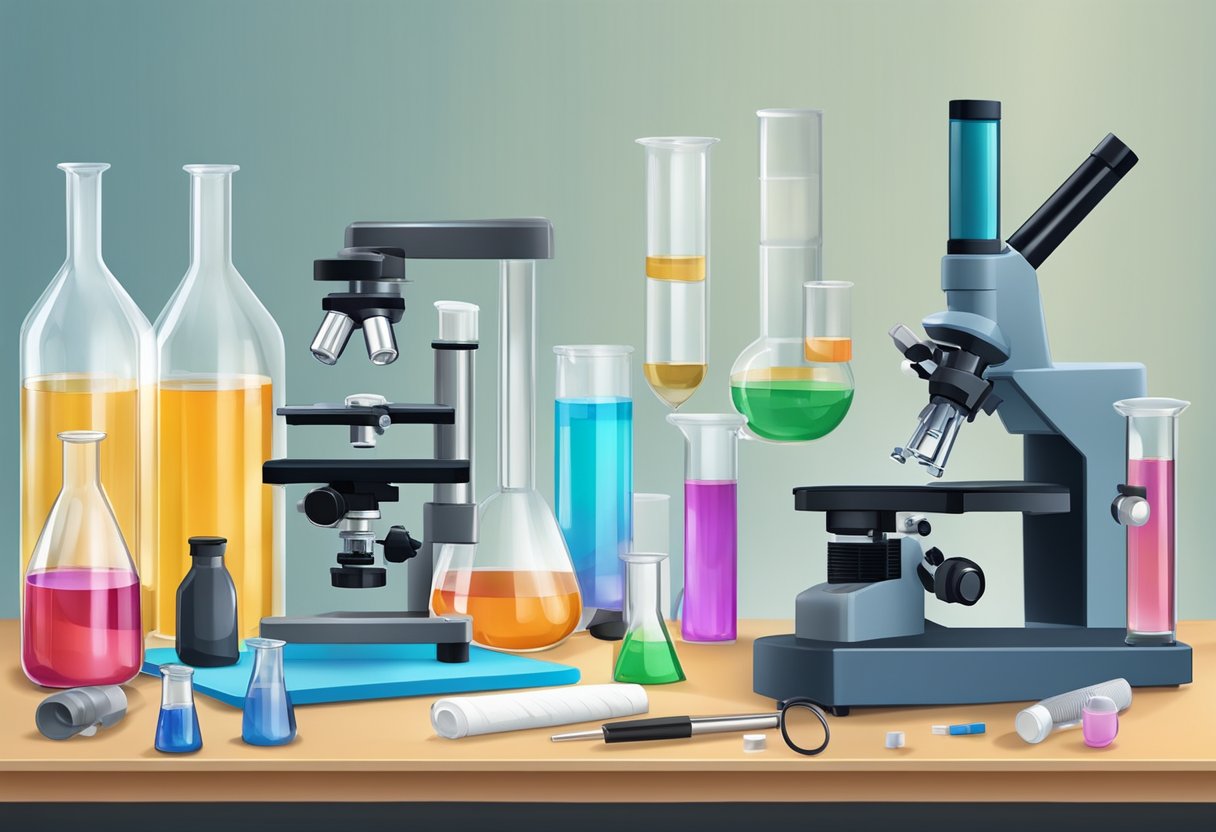
Mechanical Properties
Synthetic polyisoprene rubber is a highly elastic and durable material, with excellent tensile strength and elongation properties. It can withstand repeated stretching and compression without losing its shape or breaking down. Additionally, it has good tear resistance and abrasion resistance, making it ideal for use in applications that require high levels of durability and resilience.
Thermal Stability
Polyisoprene rubber has good thermal stability, with a high melting point and resistance to heat aging. It can withstand temperatures up to 150°C without significant degradation, making it suitable for use in high-temperature applications such as automotive parts, electrical insulation, and industrial seals.
Chemical Resistance
Polyisoprene rubber has excellent chemical resistance, with the ability to resist a wide range of chemicals, including oils, solvents, and acids. It is also resistant to ozone and weathering, making it ideal for use in outdoor applications. However, it is not recommended for use with strong oxidizing agents or concentrated acids.
In summary, synthetic polyisoprene rubber is a versatile material with a range of properties that make it suitable for use in a variety of applications. Its excellent mechanical properties, thermal stability, and chemical resistance make it a popular choice for use in automotive, industrial, and electrical applications.
Applications
Medical Products
Synthetic polyisoprene rubber has become an essential material in the medical industry. Its properties, such as high purity, low protein content, and biocompatibility, make it ideal for medical applications. It is commonly used in manufacturing surgical gloves, medical tubing, and other medical devices. The use of synthetic polyisoprene rubber in medical products has significantly reduced the risk of allergic reactions in patients, as it does not contain natural latex proteins.
Automotive Industry
The automotive industry is another sector that has benefited from the use of synthetic polyisoprene rubber. Its excellent mechanical properties, such as high tensile strength, good elasticity, and resistance to abrasion, make it suitable for manufacturing various automotive components. It is commonly used in the production of tires, belts, hoses, and other parts that require high-performance rubber.
Consumer Goods
Synthetic polyisoprene rubber is also used in the production of various consumer goods. It is commonly found in household items such as rubber bands, balloons, and erasers. Its properties, such as high elasticity and resistance to tearing, make it an ideal material for these applications. Additionally, it is used in the production of condoms, as it provides a natural feel and is less likely to cause allergic reactions than natural latex.
In conclusion, synthetic polyisoprene rubber has a wide range of applications due to its unique properties. Its use in medical products, automotive components, and consumer goods has significantly improved the quality and performance of these products.
Comparison with Natural Rubber
Synthetic polyisoprene rubber is often compared to natural rubber due to their similar chemical structures. However, there are some notable differences between the two materials.
Physical Properties
One major difference between synthetic polyisoprene rubber and natural rubber is their physical properties. Synthetic polyisoprene rubber is more uniform in its molecular structure, resulting in a more consistent and predictable material. Natural rubber, on the other hand, can vary in its molecular structure depending on the source and processing methods. This can lead to variations in physical properties such as tensile strength, elongation, and tear resistance.
Chemical Properties
Another difference between synthetic polyisoprene rubber and natural rubber is their chemical properties. Synthetic polyisoprene rubber is made from petrochemicals, while natural rubber is derived from the sap of rubber trees. This difference in origin can result in differences in chemical properties such as resistance to heat, ozone, and chemicals.
Cost
Synthetic polyisoprene rubber is generally less expensive than natural rubber. This is because it can be produced in a more controlled and efficient manner, without the need for labor-intensive harvesting and processing of rubber trees.
Overall, synthetic polyisoprene rubber and natural rubber have their own unique properties and applications. While synthetic polyisoprene rubber may be more consistent and cost-effective, natural rubber may be preferred for certain applications due to its unique properties and sustainability as a renewable resource.
Market Analysis
Demand Trends
The demand for synthetic polyisoprene rubber has been increasing steadily over the past few years owing to its excellent properties such as high elasticity, resistance to abrasion, and good tensile strength. The growth in demand can be attributed to its wide application in various industries such as automotive, healthcare, and construction. The increasing demand for eco-friendly and sustainable products is also driving the growth of the synthetic polyisoprene rubber market.
Supply Chain Dynamics
The synthetic polyisoprene rubbers market is highly consolidated with a few key players dominating the market. The raw material required for the production of synthetic polyisoprene rubber is isoprene, which is derived from petroleum. The availability and price of petroleum are major factors affecting the supply chain dynamics of the synthetic polyisoprene rubbers market.
Regulatory Impact
The synthetic polyisoprene rubbers market is subject to various regulations and standards set by regulatory authorities such as the Environmental Protection Agency (EPA) and the European Chemicals Agency (ECHA). The manufacturers are required to comply with these regulations and standards to ensure the safety and quality of the product. The increasing focus on sustainability and environmental concerns is expected to result in stricter regulations in the future.
Overall, the synthetic polyisoprene rubbers market is expected to grow at a moderate pace in the coming years due to the growing demand from various industries and increasing awareness about eco-friendly products. The supply chain dynamics and regulatory impact will continue to play a significant role in shaping the market.
Environmental Impact and Sustainability
Synthetic polyisoprene rubbers has a relatively low environmental impact compared to other synthetic rubbers. It is produced through a process that involves the polymerization of isoprene, a naturally occurring hydrocarbon, which makes it less harmful to the environment. However, the production of synthetic polyisoprene rubber still requires the use of petrochemicals, which are non-renewable resources.
The sustainability of synthetic polyisoprene rubbers depends on the disposal methods used. If it is disposed of in landfills, it will not decompose and may cause harm to the environment. However, synthetic polyisoprene rubbers can be recycled and reused in various applications, such as road construction and playground surfaces, which can extend its lifespan and reduce waste.
In terms of energy consumption, the production of synthetic polyisoprene rubbers requires significant amounts of energy, particularly during the refining process. However, efforts have been made to reduce energy consumption and increase efficiency through the use of renewable energy sources and process optimization.
Overall, while synthetic polyisoprene rubbers has a lower environmental impact compared to other synthetic rubbers, its sustainability depends on responsible disposal methods and the implementation of energy-efficient production processes.
Innovation and Technological Advancements
Research and Development
The synthetic polyisoprene rubbers industry has seen significant advancements in technology and innovation in recent years. Manufacturers are investing heavily in research and development to improve the quality and properties of synthetic polyisoprene rubbers.
One of the key areas of research has been in developing new formulations of synthetic polyisoprene rubbers that offer improved performance characteristics, such as improved tensile strength, tear resistance, and elasticity. This has been achieved through the use of new additives and fillers, as well as through modifications to the polymerization process.
Another area of research has been in developing more sustainable and eco-friendly production methods for synthetic polyisoprene rubbers. This has involved the use of renewable raw materials and the development of more efficient manufacturing processes that reduce waste and energy consumption.
Emerging Applications
The technological advancements in synthetic polyisoprene rubbers have opened up new opportunities for its use in a wide range of applications. One of the most promising areas is in the medical industry, where synthetic polyisoprene rubber is being used to produce high-quality surgical gloves that offer superior performance and protection.
Other emerging applications include the use of synthetic polyisoprene rubbers in the production of sports equipment, such as golf balls and tennis balls, as well as in the automotive industry, where it is being used to produce high-performance tires that offer improved grip and durability.
Overall, the continued investment in research and development in the synthetic polyisoprene rubbers industry is expected to lead to further advancements in technology and the development of new applications, making it an exciting area of innovation for the future.