PBAT resin
PBAT, or polybutyrate adipate terephthalate, stands out as a biodegradable aliphatic-aromatic copolymer with exceptional versatility. Particularly effective in blown film processes, PBAT undergoes modification for various applications, offering a biodegradable alternative to traditional plastics.
This polymer exhibits mechanical performance on par with polypropylene (PP) and acrylonitrile butadiene styrene (ABS), showcasing its robust nature. Notably, PBAT boasts impressive heat resistance and exceptional processability, making it adaptable to conventional blown film plants. Its unrivaled processability positions PBAT as a leader in the market, allowing for diverse applications.
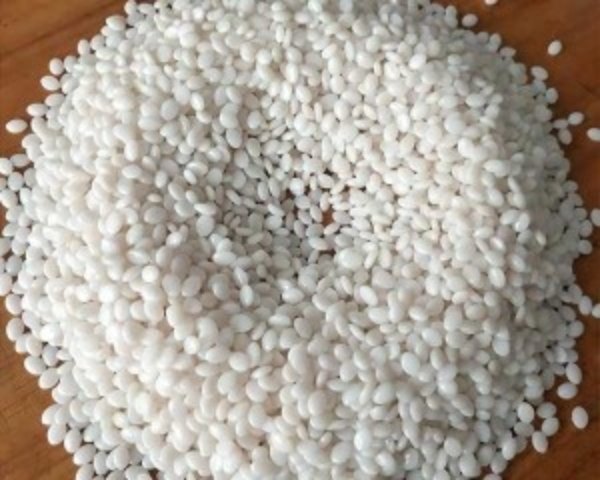
Description
- Heat Resistance: With good heat resistance, PBAT can withstand a range of temperatures, enhancing its suitability for various applications where thermal stability is essential.
- Outstanding Processability: PBAT is recognized for its outstanding processability, making it a preferred choice in blown film production. Its ability to be easily processed in conventional plants distinguishes it as a market leader.
- Compatibility with Additives: The polymer can be blended with a variety of additives, including calcium carbonate and starch. This versatility allows for the production of cost-effective products while maintaining biodegradability.
- Certifications: PBAT resins, including ours, are certified by reputable entities such as Ok Compost, BPI, ABAM, JBPA, FDA, and EU Food Contact regulations. These certifications ensure compliance with rigorous quality, safety, and environmental standards.
- Environmental Impact: PBAT’s biodegradable nature and adherence to international standards contribute significantly to reducing environmental impact. It provides a sustainable alternative to conventional plastics, particularly in single-use and disposable applications.
- Biodegradability: PBAT is a biodegradable polymer, adhering to international standards such as EN 13432 and ASTM 6400. When metabolized in the soil, it undergoes complete biodegradation into carbon dioxide, water, and biomass, contributing to environmental sustainability.
- Versatility: The copolymer’s versatility allows for modification to suit various applications, particularly in blown film processes. Its adaptability to conventional film plants underscores its flexibility in manufacturing.
- Mechanical Performance: PBAT exhibits excellent mechanical performance comparable to traditional plastics like polypropylene (PP) and acrylonitrile butadiene styrene (ABS). This feature ensures that products made from PBAT maintain robust and durable qualities.
Technical Index
Typical Property | Unit | Test Method | Result |
Density | g/cm3 | ISO 1183 | 1.21 |
MFR(190℃,2.1kg) | g/10min | ISO 1133 | 2.5~4.5 |
Melting Point | ℃ | ISO 11357 | 116~122 |
Vicat A/50 | ℃ | ISO 306 | ≥80 |
Tensile Strength | MPa | ISO 527 | ≥25 |
Elongation | % | ISO 527 | ≥400 |
Moisture | % | – | ≤0.06 |
Max Thickness of Film: 61μm
Major Applications
Toys and Leisure Products:
PBAT's versatility extends to the production of toys, leisure items, and recreational products. These items can be manufactured using biodegradable materials, aligning with environmentally conscious consumer preferences.
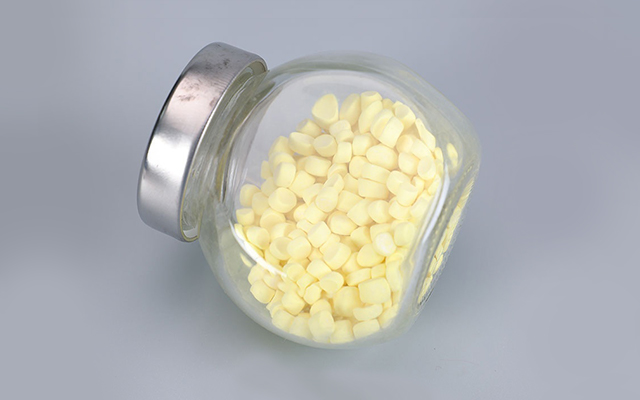
Medical Products:
In certain medical applications where disposable and biodegradable materials are preferred, PBAT can be employed in the production of items like single-use medical gloves and packaging for medical devices.
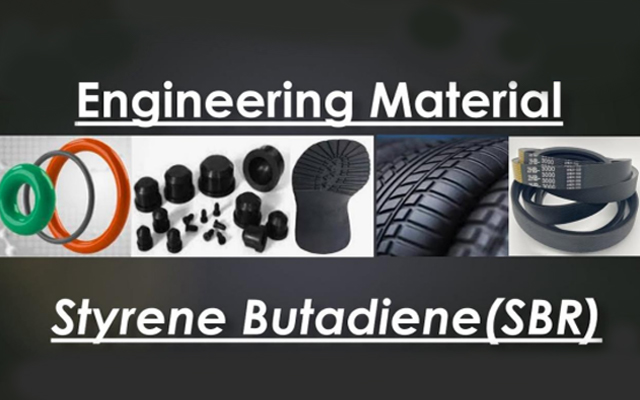
-
Package
25kg aluminum bag, each 20′ container can load 17mt
800kg aluminum big bag, each 20′ container can load 16mt -
Storage
Temperatures during transportation and storage should not exceed 70 ºC. Keep resin in dry and ventilated warehouse to prevent moisture. Avoid contacting with soil, water and sludge, and no exposure to direct sunlight and extreme temperature. The maximum shelf life is 2 years in ambient temperature of 23ºC if the package has been tightly sealed.
-
Processing guide
It is recommended to pre-dry the material prior to getting the best processing performance. If the moisture of the resin isless than 0.05% pre-drying may not be needed. Typical drying conditions: 2 hours at 80ºC (175ºF).
It is not suitable for direct film blowing, it is suggested to add slip additive like SiO2 or CaCO3, it can also be blended with starch, PLA, PHA, cellulous etc. Normally the extrusion temperature is 140ºC -170ºC which depends on formula and processing machine, it is important to make sure the blowing machine starts from the lowest temperature. If the blowing performance is not optimized it is recommended to increase the temperature by 5ºC.
In Needs of Rubber Vulcanization Accelerators Solution?
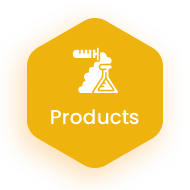
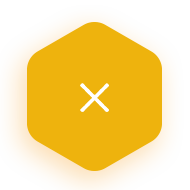