How Rubber Accelerator MBS(NOBS) Benefits For Tire Manufacturing
29/01/2025
Why Are Rubber Accelerators Important?
Rubber accelerators are essential in the tire-making process. They help speed up the curing or vulcanization of rubber, making it stronger and more durable. Without accelerators, tires would not have the same flexibility or performance. One such widely used accelerator is MBS (also known as NOBS). It is popular in the tire industry because it helps produce high-quality rubber at a faster rate. As the demand for high-performance tires continues to grow, the role of MBS becomes even more important. Tires need to be more durable, flexible, and resistant to wear and tear. This makes MBS a key ingredient in meeting these higher performance standards.
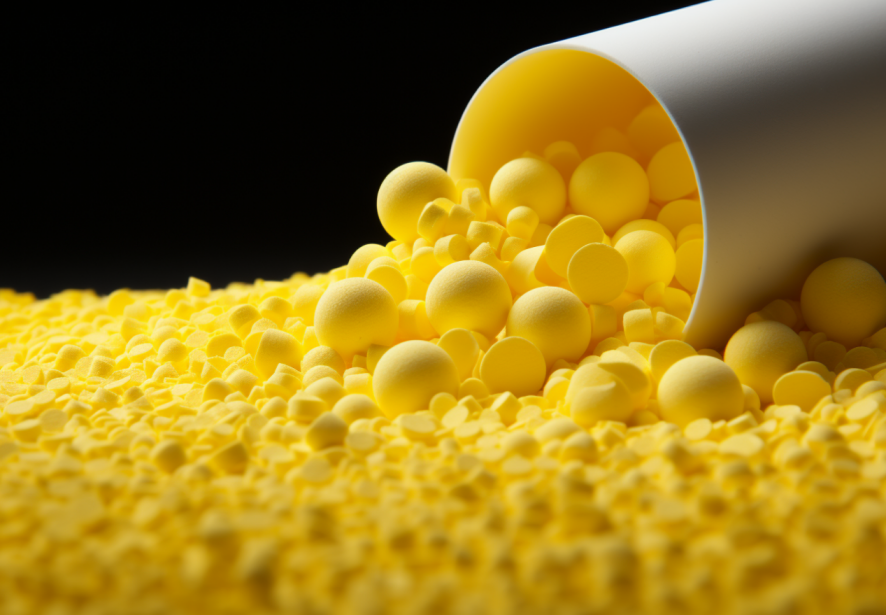
What is MBS (NOBS)?
Explanation of MBS (NOBS)
MBS, also known as NOBS, stands for N–(1,3-dimethylbutyl)-N‘-phenyl-p-phenylenediamine. This chemical compound appears as light yellow to orange-yellow granules. It has a faint ammonia smell but is non-toxic. The compound has a specific gravity between 1.34 and 1.40. It melts at a temperature higher than 78°C. MBS is soluble in several organic solvents such as benzene, ethyl acetate, and methyl alcohol. It dissolves easily in acetone, methyl benzene, and carbon tetrachloride. It is only slightly soluble in ethanol and does not dissolve in water, dilute acid, or dilute alkali. When exposed to heat, MBS slowly breaks down.
MBS is a delayed accelerator, meaning it has a slower activation time. It provides a high curing rate and excellent scorch resistance. These properties make it safer and more efficient for use in tire manufacturing. MBS disperses easily, avoids frosting, and undergoes minimal discoloration. It is mainly used in synthetic rubber mixtures, particularly those containing fine-grain furnace carbon black. This makes MBS especially suitable for the tire industry.
Overview of Its Chemical Properties and Role in Rubber Vulcanization
MBS is crucial in the vulcanization process of rubber. Vulcanization is when rubber is treated with heat and chemicals to improve its properties. MBS speeds up this curing process while ensuring that the rubber retains its strength and flexibility. This compound is a delayed accelerator, which means it works slowly over time. This is important because it provides better control over the curing process. It helps to avoid over-vulcanization and gives manufacturers more time to shape the rubber before it becomes too hard.
MBS also helps improve the rubber’s durability. It enhances properties like wear resistance, aging resistance, and overall lifespan. As a result, tires made with MBS perform better and last longer, making them more reliable on the road. MBS is widely used in the production of tires for its consistent performance and ability to enhance the properties of rubber.
Key Differences Between MBS (NOBS) and Other Accelerators Like MBT or CBS
There are several rubber accelerators available, but MBS is known for its unique properties. Compared to other accelerators like MBT (mercaptobenzothiazole) or CBS (N-cyclohexyl-2-benzothiazole sulfenamide), MBS offers several advantages.
First, MBS has a lower risk of scorching. Scorching occurs when the rubber begins to harden too soon during the curing process. MBS provides better control over this, which ensures the rubber remains workable for a longer time. This is important for maintaining product quality and consistency.
Second, MBS has a slower activation time compared to MBT and CBS. While other accelerators may cause the rubber to cure too quickly, MBS provides a more gradual curing process. This allows manufacturers to have more control over the rubber’s properties, resulting in a better end product.
Lastly, MBS is better suited for certain types of rubber mixtures, especially those containing fine-grain furnace carbon black. This makes it a more specialized and effective choice for tire manufacturing, where such mixtures are common.
Key Benefits of MBS (NOBS) in Tire Manufacturing
Improved Cure Rate
MBS significantly reduces curing time. Curing is the process that strengthens and hardens rubber. With MBS, the curing process becomes faster, which speeds up tire production. This means that manufacturers can make tires more quickly, increasing overall production efficiency. Faster vulcanization also leads to cost savings, as manufacturers use less energy and time during production.
Enhanced Durability and Performance
MBS helps improve the durability of tires. Tires made with MBS are more resistant to wear and aging. This means they last longer, which is an important factor for consumers. Tires also become more resistant to heat, reducing the likelihood of damage over time. Additionally, MBS contributes to better tire performance by improving grip, stability, and handling. These qualities are critical for high-performance tires that require high traction and control, especially in demanding driving conditions.
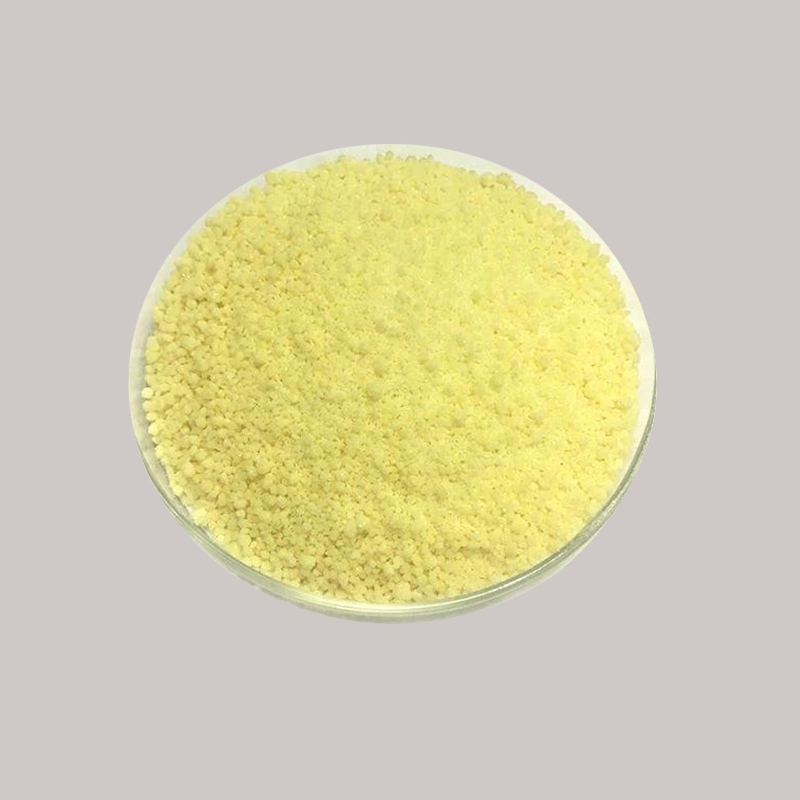
Reduced Scorching Risk
One of the key advantages of MBS is its lower risk of scorching. Scorching happens when the rubber starts to cure too soon, which can lead to uneven quality or defects in the final product. MBS minimizes this risk, giving manufacturers better control during the curing process. This feature ensures that the tires maintain consistent quality and performance, making them more reliable for consumers.
Optimal Balance of Hardness and Elasticity
MBS allows for an ideal balance between tire hardness and elasticity. This balance is crucial for improving tire performance. A tire that is too hard may have a rough ride and poor grip, while a tire that is too soft may wear out quickly and lack stability. MBS helps achieve the right amount of hardness and elasticity, which results in tires that perform better and last longer. This balance also helps improve fuel efficiency, as the tires have less rolling resistance, which in turn saves fuel. Moreover, the improved performance enhances safety by providing better control and stability.
What Makes Supplier Chembroad Stand Out?
Product Specification
Chembroad offers high-quality MBS (NOBS) with excellent specifications. The product comes as light yellow or orange-yellow granules. It has a melting point of 78°C and contains less than 0.5% reduction when heated. The ash content is also minimal, not exceeding 0.3%. These features make Chembroad’s MBS reliable and efficient for tire manufacturing.
Stability and Reliability
Chembroad is known for its stability and reliability in production. The company uses advanced German technology and a DCS control system to monitor every step of the production process. From raw materials to the final product, each stage is carefully controlled. This ensures that the MBS produced is of high quality and consistent in performance.
Products Homogenization
Chembroad ensures product homogenization by mixing semi-finished products in a large mixing bin before packaging. This process minimizes batch variations and ensures the stability of the final product. This approach helps in maintaining consistent quality across all batches, ensuring that customers get the same high-quality MBS every time.
Scientific Management
Chembroad follows scientific management practices to ensure product quality. The company holds certifications like ISO9001, ISO14001, and OHSAS18001, which demonstrate its commitment to quality, environmental standards, and safety. These certifications show that Chembroad follows standardized procedures and practices, ensuring traceability for every product batch. This provides customers with confidence in the reliability and consistency of their MBS.
Partners Testimonial
“Working with Chembroad has been a game-changer for our tire production. Their MBS (NOBS) accelerator has consistently delivered high-quality results, improving both our cure rate and product durability. We’ve noticed significant improvements in production efficiency, allowing us to meet higher demand without compromising quality. The reliability of their products has made a real difference in our day-to-day operations.” – John Miller, Production Manager, Global Tire Corp.
“We’ve been using Chembroad’s MBS for over two years, and it has truly transformed our manufacturing process. The product is easy to work with and provides excellent scorch resistance. Our tires are performing better than ever in terms of wear resistance and overall lifespan. Chembroad’s consistency and technical support have been outstanding, and we value our ongoing partnership.” – Sara Lee, Operations Director, Prime Rubber Inc.
“Chembroad’s attention to detail and the quality of their MBS (NOBS) has exceeded our expectations. The product’s quick dispersion and steady curing time have allowed us to produce superior tires. We’re grateful for their reliable service and look forward to continuing our successful collaboration.” – Michael Reed, Chief Engineer, AutoTech Manufacturing
Get Started with Chembroad’s MBS Today!
Ready to improve your tire manufacturing process? Chembroad’s MBS (NOBS) accelerator offers faster curing, better durability, and enhanced performance. With our reliable product and expert support, you can boost efficiency and product quality. Don’t wait—contact us now to learn more about how our MBS can help you achieve better results in less time. Let’s work together to take your tire production to the next level!