What Is Rubber Accelerator DTDM-80 Used For?
28/01/2025
Rubber accelerators play a crucial role in the manufacturing process by speeding up the curing of rubber, making production more efficient and resulting in stronger rubber. One commonly used accelerator is DTDM (Diphenylguanidine), and a specific version of this, DTDM-80, is widely employed across various industries to enhance the quality of rubber products. This article will dive into what DTDM-80 is and explore its applications in different industries.
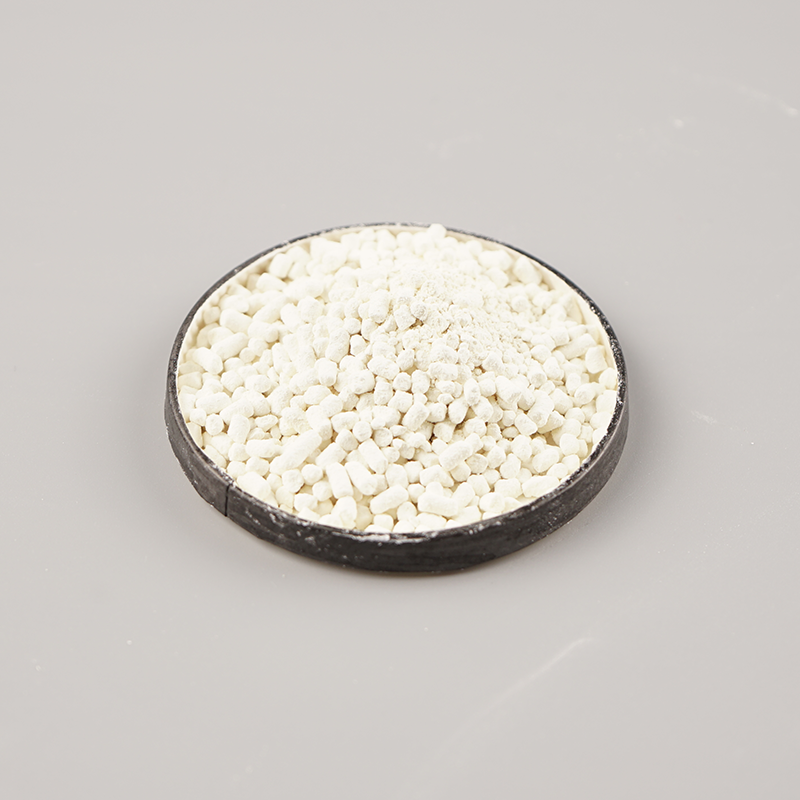
What Is Rubber Accelerator DTDM-80?
Definition of DTDM-80
DTDM-80 is a special additive used in the rubber industry. It helps improve the vulcanization process in both natural and synthetic rubber. The compound contains 80% active material. It appears as white granules. The granules have a minimum melting point of 120ºC. The formula is made with a carrier of SBR (styrene-butadiene rubber) and a binder that consists of 80% 4,4-dithiodimorpholine and 20% polymer. There is also a dispersing agent in the mix. DTDM-80 can be customized to include other binders like EPDM (ethylene propylene diene monomer) and NBR (nitrile rubber). This makes it flexible and adaptable to various rubber formulations.
Chemical Composition and Characteristics of DTDM-80
DTDM-80 serves as both a vulcanizing agent and an accelerator in rubber systems. It has good heat resistance and is resistant to aging. This makes it effective in vulcanization processes. The compound contains 27% sulfur, which is crucial in vulcanization. It releases sulfur at the right temperature for curing rubber. This ensures the rubber becomes stronger and more durable.
Brief Comparison with Other Rubber Accelerators
Compared to other accelerators like CBS (N-cyclohexyl-2-benzothiazole sulfonamide), MBTS (dibenzothiazole disulfide), and TMTD (tetramethylthiuram disulfide), DTDM-80 offers some distinct advantages. While CBS and MBTS are commonly used, DTDM-80 provides better heat resistance. It also has superior aging resistance, which helps maintain the rubber’s performance over time. TMTD is a powerful accelerator, but DTDM-80’s lower active content can provide a more controlled curing process.
Overview of Its Role in the Vulcanization Process
DTDM-80 plays a key role in the vulcanization of rubber. It speeds up the curing process by releasing sulfur. This sulfur bonds with the rubber molecules, creating cross-links. These cross-links strengthen the rubber and improve its durability. Without accelerators like DTDM-80, the vulcanization process would take longer, and the rubber would not be as strong or durable.
How Does DTDM-80 Work in Rubber Vulcanization?
Explanation of Vulcanization and Its Significance in Rubber Production
Vulcanization is the process of turning raw rubber into a stronger, more durable material. It involves heating the rubber with sulfur and other chemicals. This creates cross-links between the rubber molecules, making the material harder and more elastic. Vulcanization is important because it improves the rubber’s properties, such as heat resistance and flexibility. It is used in the production of a wide variety of rubber products, from tires to industrial parts.
How DTDM Accelerates the Vulcanization Process
DTDM-80 speeds up the vulcanization process. When heated, it releases sulfur at the right temperature. This sulfur forms cross-links between the rubber molecules. These cross-links help the rubber become stronger and more elastic. By using DTDM-80, manufacturers can shorten the curing time and improve the efficiency of production. This makes the entire process faster and more cost-effective.
Key Benefits of Using DTDM in Rubber Compounding
DTDM-80 offers several benefits when used in rubber compounding. First, it improves the efficiency of the vulcanization process, reducing curing time. This helps lower production costs. Second, it enhances the rubber’s performance by improving its heat resistance, tensile strength, and wear resistance. As a result, the final product is more durable and performs better over time. Third, DTDM-80 is cost-effective. When used in the right formulations, it can provide good results without significantly increasing the cost of production.
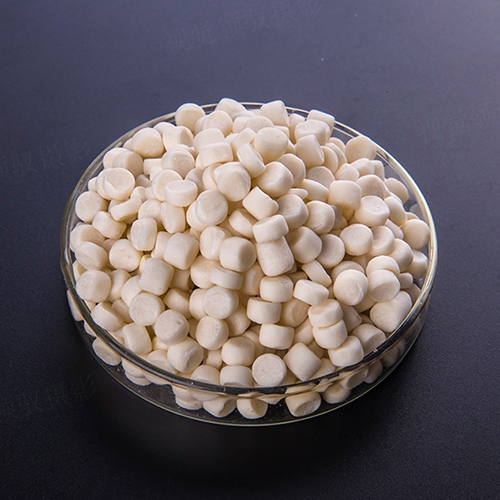
Primary Applications of DTDM-80 in the Rubber Industry
Tires
DTDM-80 is commonly used in tire manufacturing. It improves the durability and performance of tires. By accelerating the vulcanization process, it ensures that tires are stronger and more resistant to wear and tear. It also helps tires perform better under high temperatures.
DTDM-80 is also used in butyl inner tubes, adhesive tapes, and heat-resistant rubber products. In addition, it is used as an asphalt stabilizer for highways, helping to improve the quality and lifespan of road surfaces.
Industrial Rubber Products
DTDM-80 has many applications in industrial rubber products. It is used in seals, gaskets, hoses, and belts. These products are crucial in the automotive and machinery industries. The use of DTDM-80 ensures that these rubber components are strong, durable, and perform well under pressure.
Footwear
DTDM-80 is also used in the production of rubber soles and other footwear components. It helps make the rubber more durable and resistant to wear, which is essential for footwear products. By using DTDM-80, manufacturers can produce shoes with better quality and longer-lasting soles.
Sports Equipment
DTDM-80 plays a role in the production of sports equipment. It is used to make durable and high-performance rubber products for sports gear. Whether it’s rubber mats, grips, or other items, DTDM-80 helps improve the strength and flexibility of these products. This ensures that they last longer and perform better during use.
Benefits of Using DTDM-80
Enhanced Processing Speed and Reduced Curing Time
One of the main benefits of using DTDM-80 is its ability to speed up the processing time. It reduces the curing time, which helps make the manufacturing process more efficient. This is important for companies that need to produce large quantities of rubber products quickly.
Improved Heat Resistance, Tensile Strength, and Wear Resistance
DTDM-80 also improves the properties of rubber. It enhances the rubber’s heat resistance, making it more suitable for high-temperature environments. It also increases tensile strength, meaning the rubber can withstand more force before breaking. In addition, DTDM-80 improves wear resistance, helping rubber products last longer.
Increased Product Longevity and Performance
Using DTDM-80 results in products that are more durable. The cross-links formed during vulcanization make the rubber stronger. This leads to longer-lasting products that maintain their performance over time. Whether it’s tires, industrial parts, or sports equipment, the rubber remains effective and reliable for a longer period.
Cost-Effectiveness in Rubber Compounding
DTDM-80 is cost-effective when used in the right formulations. It improves the efficiency of the vulcanization process, reducing production costs. At the same time, it enhances the quality and performance of the rubber, making it a good value for manufacturers.
Why Choose Chembroad As the DTDM-80 Supplier
Specification Features
The specifications of DTDM-80 make it a standout product in rubber compounding. With an active content of 80%, it delivers high efficiency in vulcanization. The use of SBR (Styrene-Butadiene Rubber) as the carrier ensures excellent dispersion and stability. The white granules have a melting point of at least 120°C, ensuring reliability in high-temperature processes. The 100 mesh size ensures uniform blending, while the low ash content of 0.3% max maintains product purity. Mooney viscosity is kept under 50, allowing for easy processing. The heating loss content is also limited to 0.3%, which ensures minimal loss during curing. With a sulfur content of 21.6%, it provides effective vulcanization, and its density of 1.17 g/cm³ ensures the right balance of material strength and flexibility. These specifications together make DTDM-80 an efficient, durable, and cost-effective choice for rubber manufacturers.
Customizable Binder
Chembroad offers flexibility with its DTDM-80. The binder composition is made up of 80% 4,4-dithiodimorpholine and 20% polymer with a dispersing agent. This allows customization to suit specific rubber formulations. Other binders like EPDM and NBR can be used, depending on the needs of the customer. This ensures that the product can be tailored to meet various requirements.
Strong Research and Development Support
Chembroad is committed to innovation and product development. The company has a strong research and development (R&D) team that includes experts with years of experience. This team works closely with customers to develop new products and improve existing ones. Chembroad has also built long-term partnerships with independent laboratories, universities, and research institutes. These collaborations help the company stay ahead of market trends and continuously improve its products.
Choose DTDM-80 for Superior Rubber Performance
DTDM-80 is the perfect choice for improving your rubber products. With 80% active content and excellent heat resistance, it speeds up the curing process and boosts durability. Whether you’re making tires, seals, or industrial parts, DTDM-80 helps ensure better performance and longer-lasting results. Its easy processing and low ash content make it a reliable and cost-effective solution. Ready to enhance your rubber products? Contact us today to learn more about how DTDM-80 can improve your production.