From Raw to Remarkable: The Rise of PTFE Semi-Finished Products
25/02/2025
PTFE has special properties. It works quietly in many industries. You can see it in planes and cooking tools. It is used because it performs well. CHEMBROAD helps make PTFE products. It supplies top-quality raw materials. It supports the process from start to finish. CHEMBROAD is a high-tech company. It does both manufacturing and trade. The company started with rubber accelerators. Now, it also offers synthetic rubber, elastomers, plastics, and additives.
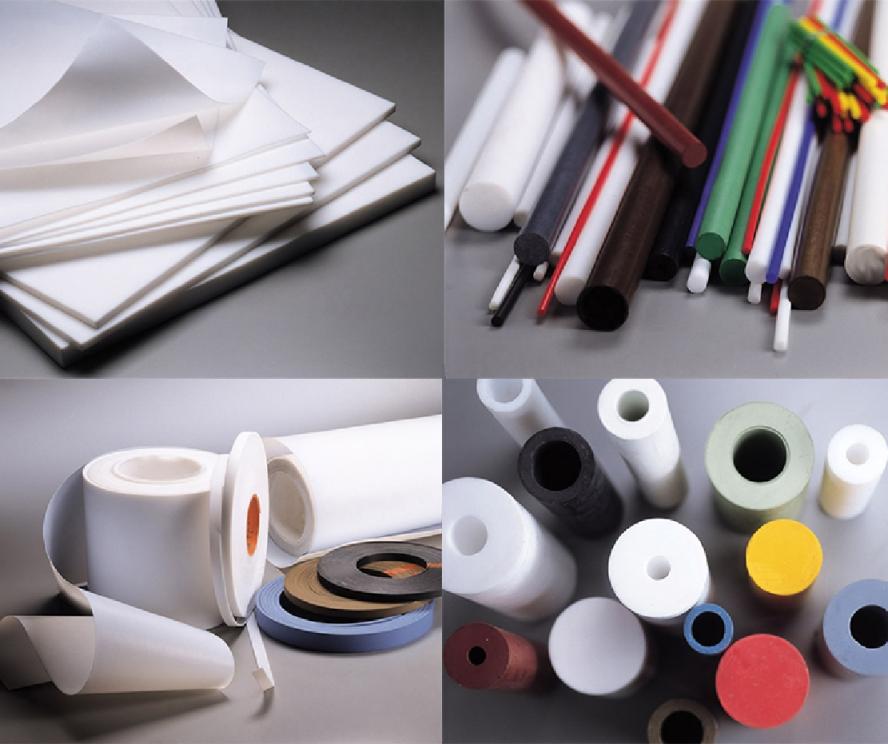
PTFE semi-finished products are strong and useful. But how are they made? Who supports this process behind the scenes? Let’s find out how PTFE goes from raw to remarkable – shall we?
What Are PTFE Semi-Finished Products?
Many Useful Forms
PTFE semi-finished products come in different shapes. These include sheets, rods, tubes, and films. Each shape has its own use. Sheets are often used for cutting gaskets. Rods are great for turning and milling. Tubes work well for insulation and fluid systems. Films are thin and flexible. They are used in electronics and packaging. These forms are easy to store and transport. They are also easy to cut or shape later.
The Middle Step
PTFE does not start as a ready-to-use part. It begins as a fine white powder. This powder is processed into semi-finished forms. These forms are not yet final products. They are the middle step. They help speed up production. Factories can buy semi-finished PTFE and shape it as needed. This saves time. It also helps reduce waste and cost. The middle step gives more control over the final product.
Easy to Work With
Semi-finished PTFE is very flexible in use. It is easy to machine, drill, or mold. It can handle heat and pressure. It also resists chemicals. These traits make it popular in many fields. Engineers and designers like how simple it is to shape. It is used for seals, valves, washers, and many custom parts. Some companies also use it for insulation, guides, or sliding parts. PTFE stays strong while being easy to work with.
Why PTFE? The Science Behind the Super Polymer
Strong Against Chemicals and Heat
PTFE does not break down easily. It can resist strong chemicals. It also stays stable under high heat. This makes it safe to use in labs and factories. Many people choose it for this reason.
Smooth and Non-Stick
PTFE has a very low friction surface. It feels smooth and does not stick to other things. That is why people use it in cookware and machines. It helps things move without damage.
Works in Tough Places
PTFE stays strong in harsh settings. It can work in cold or hot areas. It also works well where there is high pressure. Many engineers choose it for tough jobs. It lasts a long time.
CHEMBROAD: The Raw Material Powerhouse Behind the Process
Trusted Supplier with Deep Experience
CHEMBROAD is a trusted supplier of high-purity PTFE powders and compounds. The company has many years of experience in the chemical industry. It understands the needs of different clients. It can help with product development and testing. It also helps choose the right packaging. It supports clients with global shipping and delivery. Many businesses choose CHEMBROAD because it provides real help and fast solutions.
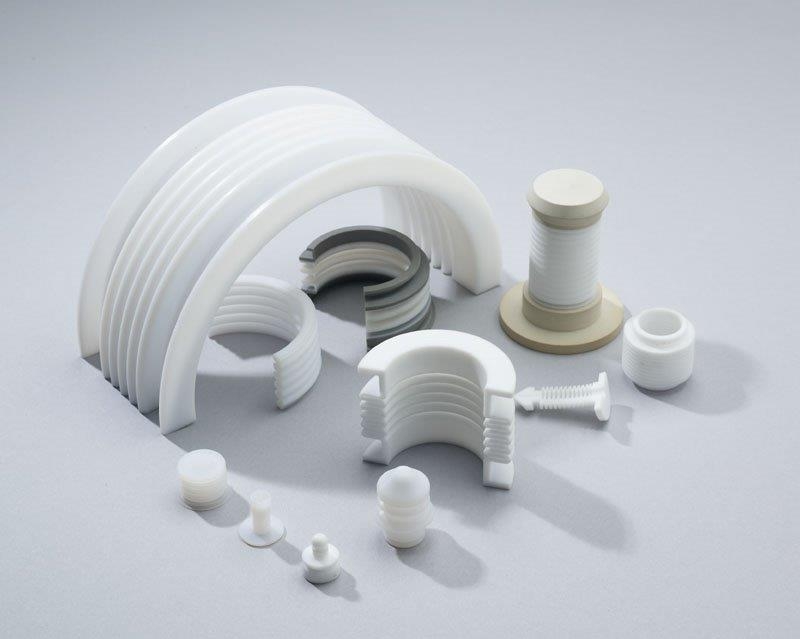
Quality in Every Step
CHEMBROAD focuses on quality, consistency, and new ideas. Every granule it makes meets strict standards. The company is certified with ISO9001. This shows it follows strong rules for quality and safety. It works to improve its process all the time. The company also cares about the environment. It makes choices that protect nature. Through many years of growth, CHEMBROAD has become a top supplier in China’s rubber and plastic chemical market.
Strong Global Partnerships
CHEMBROAD works with many global manufacturers. It helps them improve their final products. It offers high-quality raw materials and fast delivery. The company uses German technology for better production. This allows it to offer steady products at good prices. Many companies choose CHEMBROAD because they can trust its service and results.
Applications Across Industries: Where PTFE Shines
Uses in Automotive and Aerospace
PTFE is used in many car and airplane parts. It helps make seals, bearings, and insulation materials. These parts must handle heat and movement. PTFE works well in these settings. It does not wear out quickly. This makes it perfect for long-lasting use.
Role in Electronics and Semiconductors
PTFE is important in electronic products. It is used in parts that carry signals. These parts need strong and clean materials. PTFE does not react with other things. It also keeps its shape under pressure. That is why it is used in high-level electronics and chip-making.
Support for Food and Medical Safety
PTFE is safe to use with food and medicine. It meets FDA rules and does not mix with other substances. It is used to make clean surfaces in machines. It helps keep products pure and safe. Hospitals and food factories use PTFE tools for hygiene.
Sustainability & Innovation in PTFE Production
Greener Production Methods
PTFE waste used to be hard to manage. Now, new ways help reduce and reuse waste. These changes make PTFE production better for the earth. More companies are looking for cleaner methods. CHEMBROAD supports this change with smart ideas.
A Company That Cares About the Planet
CHEMBROAD works hard to protect nature. It chooses better materials and safe methods. The company also trains its team to follow green steps. It looks at every part of the process. It wants to reduce harm to the environment in each area.
Building for the Future
CHEMBROAD wants to keep growing in a smart way. It looks at future needs and plans ahead. It studies new ideas to make PTFE better. It also looks for ways to support cleaner energy and safer products. It believes in building a strong future with smart choices.
Ready to See What PTFE Semi-finished Products Can Do for You?
PTFE semi-finished products are strong, safe, and useful. They works in many industries. They helps finished products last longer. They makes machines run smoother. CHEMBROAD gives you the best raw materials. It offers support from start to finish. You get quality, speed, and trust. Many companies already choose CHEMBROAD. You can too.
Need better performance? Want clean and safe materials? Looking for a partner you can trust? Let’s talk. Let CHEMBROAD help you move forward – step by step. Contact us now. See the difference today.