5 Key Factors Influencing Antiscorching Efficiency in Rubber
29/10/2024
What is Antiscorching?
Antiscorching agents play a crucial role in the rubber industry, preventing premature vulcanization during processing. This phenomenon, known as scorching, can lead to defects in rubber products, causing them to underperform or fail entirely. The need for effective antiscorching measures is underscored by the increasing demand for high-quality rubber across various sectors, from automotive to consumer goods.
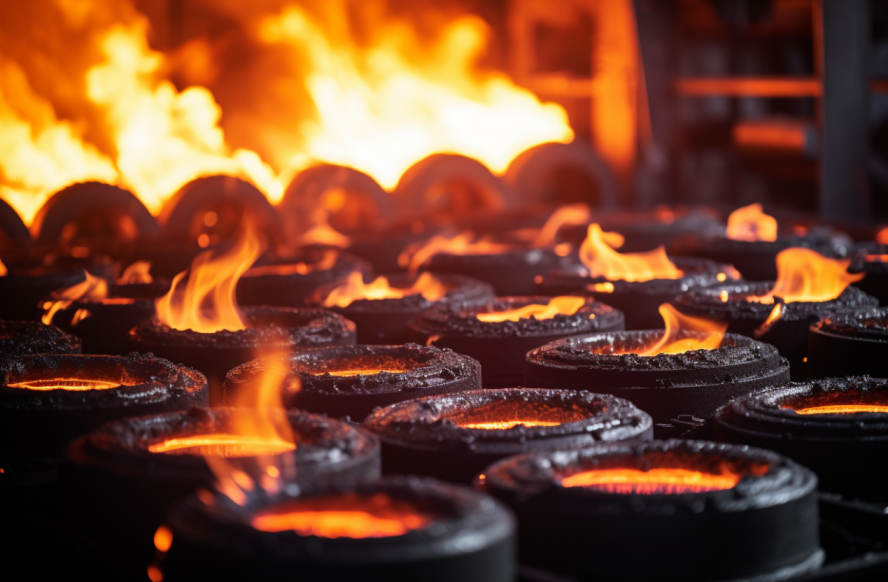
The Consequences of Scorching
When rubber compounds scorch, they become less pliable and more brittle, which adversely affects their durability and flexibility. A shocking statistic reveals that nearly 20% of rubber manufacturing defects stem from scorching issues. This not only incurs financial losses but also jeopardizes product reliability, which is paramount in industries like tire manufacturing and healthcare.
Key Factors Influencing Antiscorching Efficiency
1. Temperature Control
The Critical Role of Temperature
Temperature is perhaps the most significant factor affecting antiscorching efficiency. High temperatures accelerate the chemical reactions in rubber compounds, increasing the likelihood of scorching. Maintaining optimal processing temperatures is essential for ensuring the effectiveness of antiscorching agents.
Optimal Processing Conditions
Manufacturers must strike a balance between efficient processing times and temperature control. Implementing advanced monitoring systems can provide real-time data, allowing for immediate adjustments to temperature settings. This proactive approach significantly minimizes scorching risks.
The Impact of Equipment
The type of equipment used can also influence temperature regulation. High-quality mixers and extruders designed for specific rubber compounds can enhance temperature uniformity. This ultimately helps maintain the integrity of antiscorching agents during production.
2. Quality of Antiscorching Agents
Selecting the Right Ingredients
Not all antiscorching agents are created equal. The choice of ingredients can significantly affect the overall performance of rubber compounds. Effective antiscorching agents must be compatible with other additives to avoid adverse reactions that can lead to scorching.
Innovations in Antiscorching Solutions
Shanghai Chembroad New Materials Co., Ltd. is at the forefront of developing innovative antiscorching solutions. Their commitment to research and development enables them to offer high-performance agents that improve product quality and processing efficiency.
Tailoring Solutions for Specific Applications
Different applications require unique formulations. Understanding the specific needs of various sectors, such as tire manufacturing or waterproofing materials, allows suppliers to provide tailored antiscorching solutions that maximize efficiency.
3. Rubber Compound Composition
The Impact of Formulation
The composition of rubber compounds plays a pivotal role in antiscorching efficiency. Various fillers, elastomers, and additives can either enhance or hinder the effectiveness of antiscorching agents. A well-balanced formulation is essential for optimal performance.
Testing and Optimization
Continuous testing and optimization of compound formulations are vital. Conducting rheological tests can help manufacturers determine the best mix of ingredients to reduce scorching potential while maintaining desired physical properties.
Collaborating with Suppliers
Working closely with suppliers like Shanghai Chembroad can provide valuable insights into the best formulations for specific applications. Their expertise in rubber chemistry ensures that manufacturers can achieve the highest quality in their products.
4. Processing Techniques
Advanced Manufacturing Methods
Modern processing techniques, such as continuous mixing and advanced extrusion methods, can significantly influence the efficiency of antiscorching agents. These methods allow for better dispersion of additives and improved control over processing conditions.
Importance of Mixing Time
The duration of mixing also impacts the effectiveness of antiscorching agents. Overmixing can lead to excessive heat generation, increasing the risk of scorching. Careful monitoring of mixing times is crucial to prevent these issues.
Training and Expertise
Having skilled personnel who understand the nuances of rubber processing can make a considerable difference. Training programs focusing on best practices can enhance the overall efficiency of antiscorching measures within manufacturing facilities.
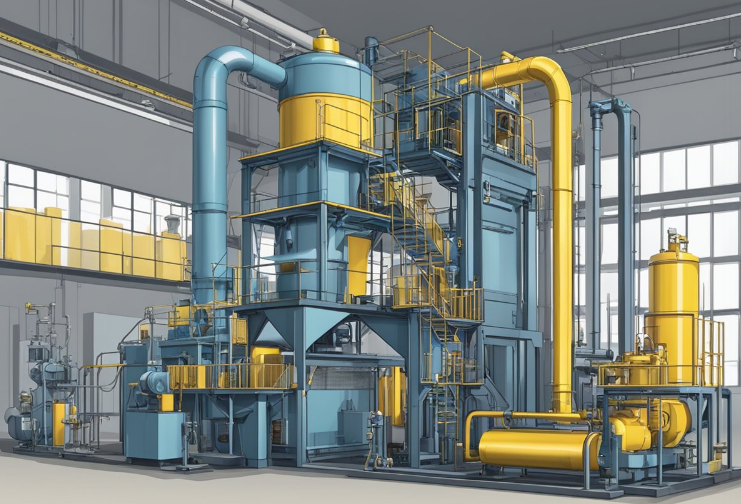
5. Environmental Factors
Humidity and Its Effects
Environmental conditions, particularly humidity, can also influence antiscorching efficiency. High humidity levels can affect the absorption and dispersion of antiscorching agents, potentially leading to less effective performance.
Adapting to Local Conditions
Manufacturers must consider local environmental factors when selecting and applying antiscorching agents. Tailoring formulations to suit specific climatic conditions can enhance their effectiveness and reduce the risk of scorching.
Commitment to Sustainability
As an ISO9001 certified company, Shanghai Chembroad prioritizes environmental harmony in its operations. By developing eco-friendly antiscorching agents, they not only enhance product performance but also align with global sustainability goals.
Why Choose Shanghai Chembroad New Materials Co., Ltd. for Antiscorching Solutions?
Comprehensive Product Range and Industry Expertise
Expertise Across Multiple Sectors
Starting as a manufacturer of rubber accelerators, Shanghai Chembroad has expanded its business scope to include synthetic rubber, thermoplastic elastomers, plastics, and various plastic additives. Their comprehensive product range allows them to serve multiple sectors, including tire manufacturing, rubber tubing, cables, waterproofing materials, and more. This extensive industry expertise ensures that the company understands the unique requirements of each sector, making them a valuable partner for businesses seeking high-quality antiscorching solutions.
Application Versatility
The company’s antiscorching products are widely used across diverse industries, such as petrochemical, automotive, and consumer goods. By catering to a broad spectrum of applications, Shanghai Chembroad can offer customized solutions that enhance the performance and durability of rubber compounds, making their offerings ideal for clients with specific performance criteria.
International Reach and Collaboration
With a presence in over 30 countries across Asia, Europe, and America, Shanghai Chembroad has established itself as a global player in the rubber and plastic chemical industry. The company works closely with leading global companies, many of which are key market players in their respective fields. These long-term partnerships are a testament to Chembroad’s reliability, consistency, and commitment to customer satisfaction.
Advanced Technology and Quality Control
Cutting-Edge Production Technology
Shanghai Chembroad employs advanced equipment, production technology, and DCS process control systems to ensure the highest levels of product quality and stability. The use of these technologies enables precise control over manufacturing processes, reducing variability and ensuring consistent product performance. This technological edge is critical for producing reliable antiscorching agents that meet the demanding requirements of modern rubber processing.
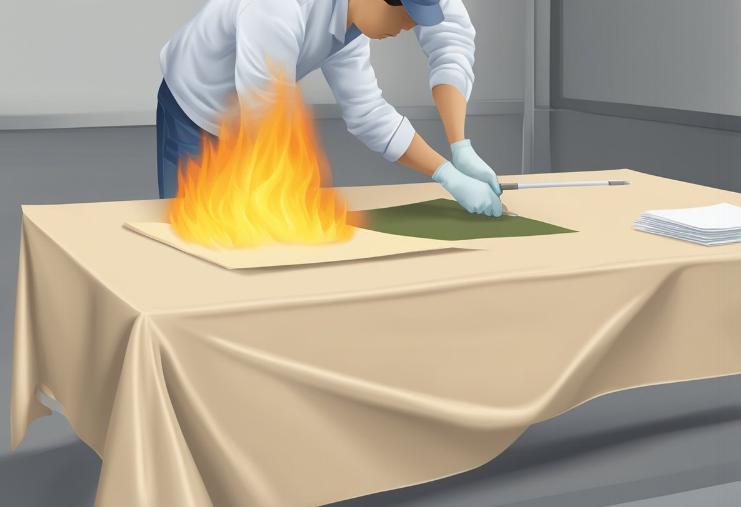
Rigorous Testing and Quality Assurance
The company is equipped with a comprehensive range of testing equipment that ensures all products meet strict quality standards. From raw material inspections to finished product testing, every stage of production undergoes rigorous scrutiny. This level of quality assurance guarantees that Chembroad’s products maintain their performance across different batches and applications, providing customers with peace of mind regarding product reliability.
Homogenization for Stability
One of the key features of Chembroad’s quality control is their focus on product homogenization. During the production process, semi-finished products are mixed and homogenized in large bins before packaging. This minimizes batch variations and ensures that each container of product maintains consistent properties, which is crucial for applications requiring precise performance characteristics.
Strong Research & Development Capabilities
Innovative Product Development
Shanghai Chembroad’s strong research and development (R&D) capabilities set them apart in the competitive chemical industry. The company’s core R&D team comprises doctors, masters, and senior professional technicians who drive innovation and product development. This expertise allows Chembroad to anticipate market trends, stay ahead of customer needs, and continuously introduce new products and models for sustainable growth.
Custom Solutions for Specific Needs
With extensive experience in project initiation, development trials, and product application, Chembroad has customized nearly 100 product models for different users. Their ability to create tailored solutions for specific customer requirements makes them an ideal partner for businesses seeking specialized antiscorching agents that align with their production processes and end-use applications.
Collaboration with Research Institutions
To support its innovation efforts, Shanghai Chembroad maintains long-term collaborations with independent laboratories, universities, and research institutes. These partnerships enhance the company’s research capabilities, enabling them to develop advanced formulations and applications that address the evolving needs of the rubber and plastic industries.
Commitment to Environmental Sustainability
Sustainable Practices and Certifications
Shanghai Chembroad is committed to environmental sustainability and operates in line with international standards. As an ISO9001 and ISO14001 certified company, Chembroad prioritizes sustainable practices in all its operations, from raw material sourcing to product manufacturing. This dedication to environmental harmony is reflected in their product offerings, which are designed to minimize ecological impact while maintaining high performance.
Eco-Friendly Product Development
Chembroad’s commitment to sustainability is evident in their product development strategy. By focusing on eco-friendly formulations and production methods, the company ensures that its antiscorching agents meet global environmental standards. This approach not only supports their customers’ sustainability goals but also contributes to the industry’s overall shift toward greener practices.
Supporting Corporate Social Responsibility
The company’s sustainable strategies are aligned with national policies and global corporate social responsibility (CSR) initiatives. By developing new processes and products that reduce environmental impact, Shanghai Chembroad demonstrates its role as a responsible corporate citizen and a leader in sustainable innovation.
Conclusion
Antiscorching is a vital aspect of rubber manufacturing that directly impacts product quality and performance. By understanding the key factors influencing antiscorching efficiency, manufacturers can take proactive steps to minimize scorching risks. Companies like Shanghai Chembroad New Materials Co., Ltd. are leading the way in providing innovative solutions that meet the evolving needs of the rubber industry. With a commitment to quality and sustainability, they are poised to continue their role as a premier supplier in this essential field.