The Role of Rubber Accelerator DCBS in Industrial Rubber Goods Making
29/01/2025
The rubber industry is crucial to several manufacturing sectors, including automotive and construction. Rubber is used to create essential products like tires, seals, and more, which are part of everyday life. To enhance the quality and performance of these products, the industry continually seeks improvements. One such advancement involves using chemicals like Rubber Accelerator DCBS (N-Cyclohexyl-2-benzothiazole sulfenamide). DCBS speeds up the curing process, making rubber stronger and more durable. This helps manufacturers produce rubber products that not only last longer but also perform better under various conditions.
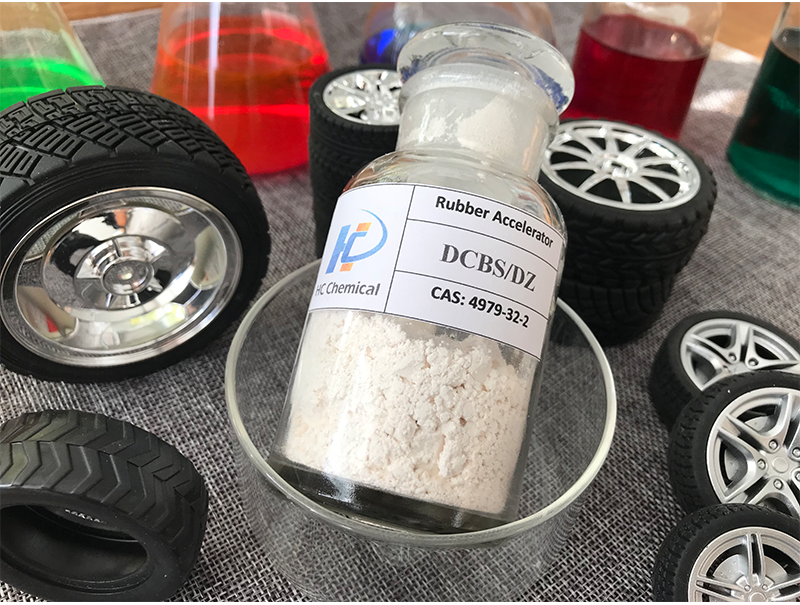
What is Rubber Accelerator DCBS?
Definition and Chemical Structure of DCBS
Rubber Accelerator DCBS stands for N-Cyclohexyl-2-benzothiazole sulfenamide. It is a chemical used in rubber manufacturing to speed up the vulcanization process. The chemical structure of DCBS consists of a benzothiazole ring, which is bonded to a cyclohexyl group. This structure makes it highly effective in reacting with sulfur, which is essential for vulcanization.
Function as a Sulfur Accelerator in the Vulcanization Process
In the rubber vulcanization process, sulfur is used to form cross-links between polymer chains. This makes the rubber stronger and more elastic. DCBS works by speeding up the sulfur’s ability to create these cross-links. It acts as an accelerator, which helps reduce the time and energy needed to vulcanize the rubber. Without accelerators like DCBS, vulcanization would take longer and require higher temperatures.
Why it is Preferred Over Other Accelerators
DCBS is often preferred over other accelerators because it provides several advantages. First, it is more cost-effective than some alternatives. It allows manufacturers to produce rubber goods at a lower cost without sacrificing quality. Additionally, DCBS has environmental benefits. It reduces the need for hazardous chemicals that are often used in other accelerators. This makes it a safer option for both workers and the environment.
Characteristics of Chembroad Rubber Accelerator DCBS
Chembroad Rubber Accelerator DCBS has several notable characteristics that make it a popular choice in the industry. It is a light yellow to pink powder. It has a melting point of about 97°C, which means it starts to break down at higher temperatures. The product also has a very low ash content (less than 0.3%) and minimal heating reduction (less than 0.4%). This ensures a consistent quality in the final rubber products.
Chembroad uses advanced German production technology and a DCS control system to monitor every stage of production. This includes careful monitoring of raw materials, the production process, testing, and storage to ensure that the quality of the accelerator is always high.
How DCBS Works in Rubber Vulcanization
Process of Rubber Vulcanization
Vulcanization is the process of heating rubber with sulfur to improve its properties. The process begins by mixing the rubber with sulfur and an accelerator, like DCBS. The mixture is then heated to a specific temperature, typically between 140°C and 160°C. As the rubber heats up, the sulfur forms cross-links between the polymer chains. The accelerators, such as DCBS, speed up this process by increasing the rate at which sulfur bonds with the rubber. This makes the rubber stronger, more elastic, and more durable.
Specific Impact of DCBS in Improving the Performance of the Vulcanization Process
DCBS improves both the efficiency and performance of the vulcanization process. By speeding up the reaction between sulfur and rubber, it reduces the time needed for curing. This not only increases productivity but also helps lower energy costs. In addition, DCBS ensures that the curing process is more consistent, resulting in uniform rubber properties. This improves the overall quality of the rubber, making it stronger and more resilient under various conditions.
Comparison of the Curing Time and Temperature Optimization with DCBS
One of the main benefits of using DCBS is its ability to optimize curing time and temperature. Compared to other accelerators, DCBS can shorten the curing time significantly. This means that rubber products can be produced more quickly and with less energy. Moreover, DCBS allows the curing process to occur at lower temperatures, which further reduces energy consumption and prevents overheating that could damage the rubber.
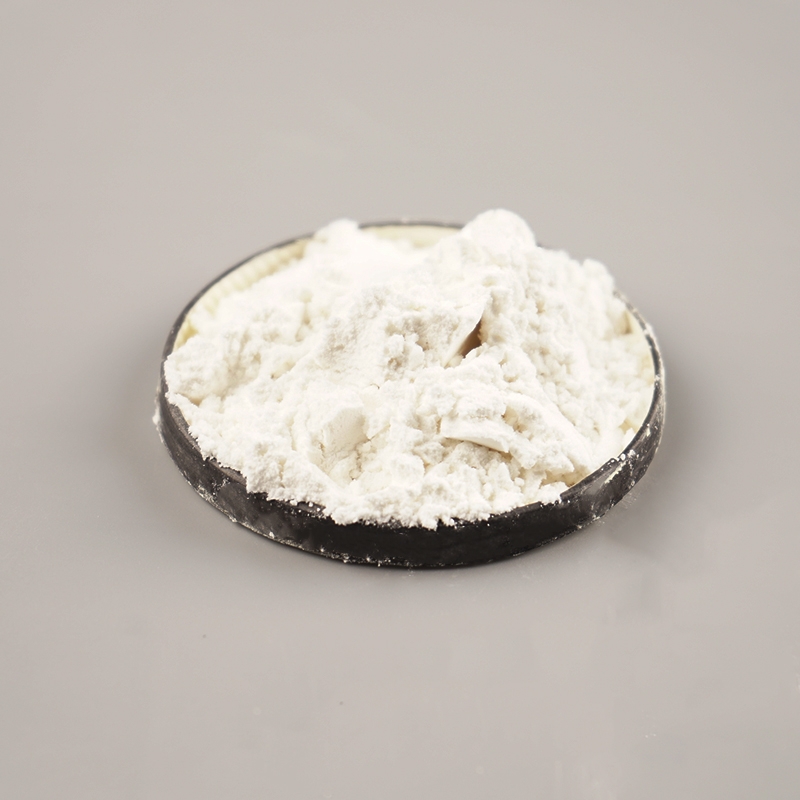
Key Benefits of DCBS in Industrial Rubber Goods
Enhanced Curing Speed and Consistency
One of the key advantages of using DCBS in rubber production is its ability to enhance curing speed. This means that rubber goods can be manufactured more quickly, increasing efficiency in production. Additionally, DCBS helps ensure that the curing process is consistent, leading to rubber products with more uniform quality. This consistency is particularly important in industries where precise material properties are essential.
Improved Mechanical Properties
DCBS contributes significantly to the mechanical properties of rubber. It helps improve the tensile strength, elasticity, and wear resistance of the final product. Tensile strength refers to the rubber’s ability to stretch without breaking, while elasticity measures how well it returns to its original shape after stretching. Wear resistance ensures that the rubber holds up over time, especially under conditions of friction or pressure. By improving these properties, DCBS helps create durable and high-performance rubber products.
Contribution to Durability, Heat Resistance, and Overall Product Lifespan
In addition to improving mechanical properties, DCBS also enhances the rubber’s durability and heat resistance. It allows the rubber to perform well under high temperatures and extreme conditions. This makes it ideal for use in applications where the rubber is exposed to heat, such as automotive parts and industrial machinery. As a result, rubber products treated with DCBS tend to have a longer lifespan, reducing the need for replacements and improving the overall value of the product.
Potential Environmental Benefits
DCBS also offers environmental benefits. Unlike some other rubber accelerators, which may contain harmful chemicals, DCBS has a lower environmental impact. It reduces the need for hazardous materials that can be dangerous to workers and the environment. By using DCBS, manufacturers can produce rubber products that are safer and more sustainable, helping to reduce the overall ecological footprint of the rubber industry.
Applications of DCBS in Industrial Rubber Goods
Automotive Parts
One of the primary applications of DCBS is in the production of automotive parts. Rubber components like tires, seals, and gaskets require high durability and performance. DCBS helps achieve this by improving the rubber’s mechanical properties and ensuring consistent curing. As a result, automotive parts made with DCBS-treated rubber tend to be more reliable and last longer.
Consumer Goods
DCBS is also widely used in the production of consumer goods such as rubber hoses, belts, and shoe soles. These products benefit from the enhanced elasticity, wear resistance, and durability that DCBS provides. For example, rubber hoses used in machinery or automotive systems need to withstand constant bending and pressure. DCBS-treated rubber helps ensure that these hoses last longer and perform more reliably.
Industrial Applications
In industrial settings, DCBS is used to produce rubber goods like conveyor belts, industrial seals, and electrical insulation. These products are essential for many manufacturing processes, and they need to be resistant to heat, pressure, and wear. DCBS helps improve the performance of these products by ensuring consistent curing and enhancing their mechanical properties.
Focus on Emerging Uses and Innovations with DCBS in Specialty Rubber Products
Beyond traditional applications, there is growing interest in using DCBS in specialty rubber products. As new technologies and industries develop, the demand for rubber materials with unique properties is increasing. DCBS is being explored for use in these emerging applications, such as high-performance gaskets, medical rubber products, and advanced coatings. Its ability to enhance rubber’s durability, heat resistance, and overall performance makes it a promising ingredient for new rubber innovations.
Take Your Rubber Products to the Next Level with Our DCBS!
If you’re looking to improve the quality and efficiency of your rubber goods, DCBS is the solution. It speeds up the curing process, boosts the strength and durability of your products, and reduces energy costs. Plus, it’s environmentally friendly and cost-effective. Don’t miss out on these benefits – upgrade your rubber manufacturing with DCBS today! Contact us for more information and to get started.