NBR Synthetic Rubber: The Game-Changer in Durability and Performance
28/02/2025
The Rising Demand for Nitrile Butadiene Rubber (NBR)
Nitrile Butadiene Rubber (NBR) is a highly durable and flexible material, widely used across various industries. Its exceptional resistance to oil, chemicals, and heat makes it ideal for demanding applications. As industries seek longer-lasting and high-performance materials, NBR is becoming an increasingly popular choice.
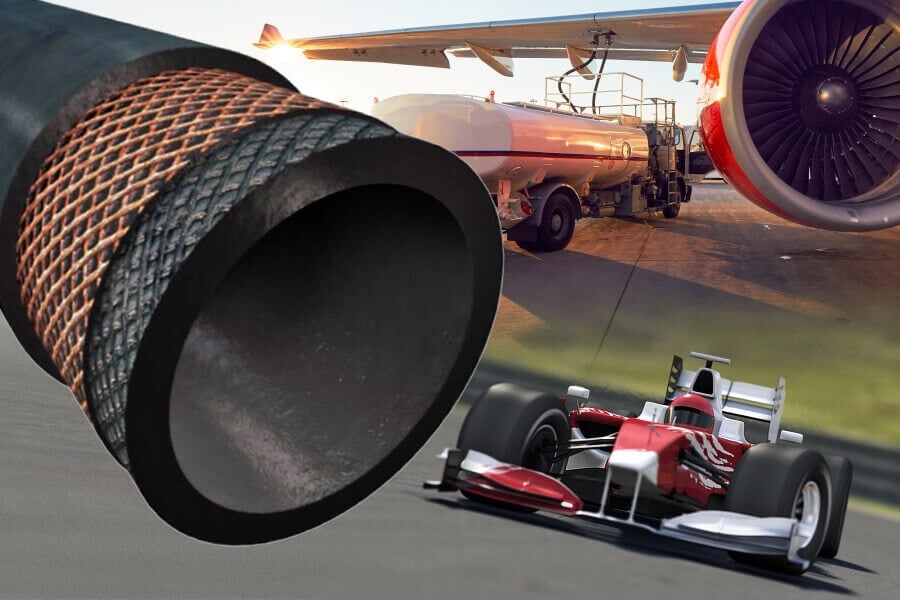
So, why is NBR gaining so much attention? Its superior durability and reliability make it a go-to solution in the automotive, medical, and industrial sectors. From seals and gloves to hoses and gaskets, NBR excels in tough environments. As technology advances, NBR’s role in manufacturing continues to expand-how will it shape the future of industrial innovation?
What is NBR? Understanding the Science
Chemical Composition and Unique Properties
Nitrile Butadiene Rubber (NBR) is a synthetic rubber. It is made from acrylonitrile and butadiene. The mix of these chemicals gives NBR its strength. Acrylonitrile increases resistance to oil and fuel. Butadiene adds flexibility and durability. NBR is tough and long-lasting. It works well in demanding environments.
Comparison with Other Synthetic Rubbers
NBR is different from other synthetic rubbers. Natural rubber is soft but wears out quickly. Silicone rubber resists heat but is not strong against oils. Neoprene handles weather well but does not resist fuel as much as NBR. NBR is the best choice for industries needing oil and chemical resistance.
Key Factors Contributing to Its Durability
NBR lasts longer than many other rubbers. It does not break down easily in oil or fuel. It stays flexible even under pressure. It resists tearing and cracking. This makes it a good material for seals, gaskets, and hoses. It is strong, reliable, and built to last.
Unmatched Performance: Strength and Resilience
High Resistance to Oils, Fuels, and Chemicals
NBR does not absorb oil or fuel. It stays strong even when exposed to harsh chemicals. Many rubbers weaken in these conditions, but NBR remains stable. This makes it useful in industries where exposure to fuels and oils is common.
Exceptional Wear-and-Tear Resistance
NBR resists wear and tear better than many other materials. It does not break down easily under stress. It holds up well in machines and moving parts. This makes it a good choice for long-lasting seals and gaskets.
Temperature Tolerance and Flexibility
NBR performs well in extreme temperatures. It stays flexible in the cold. It does not melt or lose shape in heat. This makes it a good material for industries working in tough environments. It can handle high and low temperatures without losing its strength.
Industries Driving the Demand for NBR
Automotive: Fuel Hoses, Seals, and Gaskets
The automotive industry uses NBR in many parts. It is found in fuel hoses, seals, and gaskets. These parts need to resist fuel and oil. NBR helps keep vehicles running safely and efficiently. It prevents leaks and extends the life of engine parts.
Aerospace: High-Performance Applications
NBR is used in aircraft components. Planes operate in extreme conditions. They need materials that can handle high pressure, oil exposure, and temperature changes. NBR is used in seals, gaskets, and fuel system parts. It helps keep aircraft safe and efficient.
Medical & Healthcare: Gloves, Tubing, and Protective Gear
The medical industry relies on NBR for safety. It is used in gloves, tubing, and protective equipment. NBR gloves resist chemicals and punctures. Medical tubing made from NBR is flexible and durable. It is a trusted material in hospitals and healthcare settings.
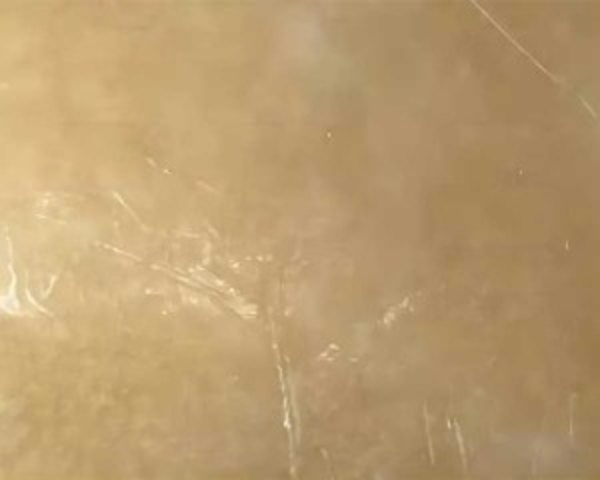
Eco-Friendly Advances in NBR Production
Sustainable Production Techniques
NBR production is becoming more sustainable. New methods use less energy and fewer harmful chemicals. Factories focus on reducing waste during production. Cleaner processes lower pollution and improve efficiency. Companies invest in new ways to make NBR safer for the environment.
Recycling and Biodegradability Considerations
Recycling NBR helps reduce waste. Old NBR products can be processed into new materials. Some industries reuse NBR in different applications. Research is also looking into making NBR more biodegradable. This will help reduce environmental impact in the future.
Efforts to Reduce Carbon Footprint
Manufacturers work to lower carbon emissions. They improve energy efficiency in production. Some use renewable energy sources to power factories. Reducing transportation costs also helps. These steps make NBR production more eco-friendly.
Why Choose NBR Synthetic Rubber in CHEMBROAD
Meeting Customer Needs with Expert Solutions
CHEMBROAD understands industry needs. We help with product development and testing. We also assist in choosing the right packaging. Our global shipping ensures timely delivery. We provide solutions that meet specific customer demands.
High Acrylonitrile Grades for Better Oil and Abrasion Resistance
NBR with more acrylonitrile resists oil and wear better. It works well in harsh conditions. It is ideal for industries that need strong and durable rubber. These grades help improve product lifespan and reliability.
Hydrocarbon Resistance and Acrylonitrile Content
NBR resists hydrocarbons. This resistance increases with more acrylonitrile. Higher acrylonitrile content makes it better for use with oils and fuel. This property is important for automotive and industrial applications.
Temperature Range of Different NBR Grades
Standard NBR works between -25°C and 100°C. Some grades handle colder temperatures, down to -50°C. Others can withstand heat up to 150°C. Choosing the right grade ensures better performance.
Custom Solutions for Unique Requirements
CHEMBROAD offers flexible solutions. We understand that standard specifications may not fit all needs. We customize products based on customer requests. Our research team works to develop the best solution. Contact us to find the right NBR for your application.
Challenges and Market Competition
Cost Factors and Supply Chain Concerns
NBR prices change based on raw material costs. Global supply chain issues affect availability. Manufacturers work to keep costs stable. Companies focus on improving efficiency to reduce expenses.
Rival Materials: Silicone, EPDM, and Natural Rubber
NBR competes with other rubber types. Silicone resists heat better but costs more. EPDM is good for weather resistance but does not handle oil well. Natural rubber is flexible but wears out faster. NBR stands out for oil resistance and durability.
Future Innovations to Improve NBR‘s Appeal
Research focuses on making NBR better. Scientists develop stronger and more flexible formulas. New processing methods reduce waste. Future improvements will help NBR stay competitive in the market.
Future Outlook: Where is NBR Headed?
Emerging Technologies and Research
New technologies improve NBR properties. Researchers work on stronger, more heat-resistant formulas. Eco-friendly production methods are a priority. Innovations help make NBR more versatile.
Expanding Applications in Next-Gen Industries
NBR is finding new uses. It is being used in electric vehicles and advanced medical devices. Aerospace companies explore new ways to use it. Growth in these sectors will drive demand for NBR.
Market Projections and Growth Trends
The demand for NBR is increasing. More industries rely on its durability and resistance. Market experts predict steady growth. Companies investing in better production will lead the industry.
Select CHEMBROAD for Premium NBR Rubber
NBR rubber is known for its strength, durability, and resistance to oils and chemicals. It is widely used across automotive, aerospace, and medical sectors. At CHEMBROAD, we offer top-grade NBR rubber for all your applications. Our products comply with the highest industry standards, and we provide tailored solutions to meet your specific requirements. From product selection to testing and delivery, our expert team is here to support you. We guarantee reliable, fast worldwide shipping. Reach out today to secure the finest NBR rubber for your business.