Heat Stabilizers in Polymers: Balancing Performance and Environmental Impact
30/10/2024
Introduction: The Critical Role of Heat Stabilizers
Have you ever wondered how everyday plastic products maintain their strength and appearance despite constant exposure to heat? The answer often lies in heat stabilizers in polymers. These essential additives play a pivotal role in enhancing the thermal stability of polymers, ensuring their durability and longevity. As industries evolve, balancing performance with environmental impact becomes increasingly crucial. This blog delves into the complexities of heat stabilizers in polymers, their applications, and future trends.
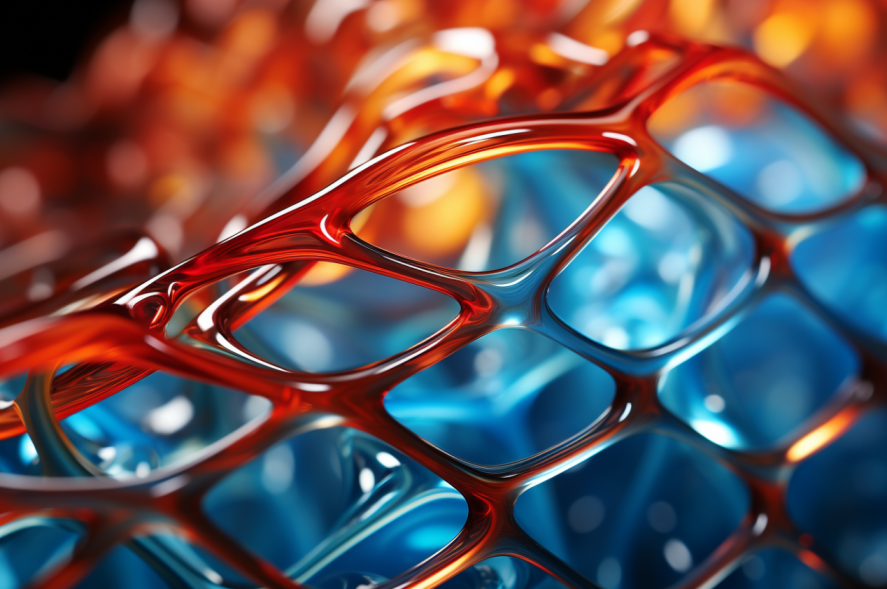
Understanding Heat Stabilizers in Polymers
What Are Heat Stabilizers?
Heat stabilizers are compounds added to polymers to prevent degradation caused by heat. They function by absorbing harmful thermal energy and inhibiting the breakdown of polymer chains. Without these stabilizers, materials like PVC and polyethylene would become brittle, discolored, and lose their mechanical properties over time.
Types of Heat Stabilizers
Various types of heat stabilizers are utilized in the industry, including organotin compounds, metal soaps, and phosphites. Each type serves a specific purpose and can be tailored to the needs of different polymers. For instance, organotin stabilizers are often used in rigid PVC applications due to their effectiveness and reliability.
Applications Across Industries
Heat stabilizers in polymers find applications in numerous sectors, including automotive, construction, and consumer goods. In the automotive industry, for example, they ensure that plastic components can withstand high temperatures without losing integrity. Similarly, in construction, they help maintain the performance of materials exposed to sunlight and heat over time.
Compatibility Issues with Heat Stabilizers in Polymers
The Importance of Compatibility
Compatibility between heat stabilizers and the base polymer is crucial for maximizing performance. Incompatible stabilizers can lead to phase separation, resulting in reduced effectiveness and potential product failure. Understanding the chemical properties of both the stabilizer and the polymer is essential for successful formulation.
Testing for Compatibility
To ensure compatibility, rigorous testing is performed during product development. Techniques such as differential scanning calorimetry (DSC) and rheological analysis help assess the interactions between heat stabilizers and polymers. This testing allows manufacturers to predict performance outcomes and make necessary adjustments.
Strategies for Improvement
When faced with compatibility issues, formulators can adopt several strategies. These include modifying the polymer structure, using compatibilizers, or selecting alternative stabilizers that align better with the polymer’s characteristics. Continuous research and development play a significant role in identifying optimal solutions.
How to Effectively Incorporate Heat Stabilizers in Polymers
Formulation Best Practices
Incorporating heat stabilizers in polymers requires careful consideration of formulation practices. Proper mixing techniques and processing conditions ensure a uniform distribution of stabilizers within the polymer matrix. This uniformity is vital for achieving consistent performance across batches.
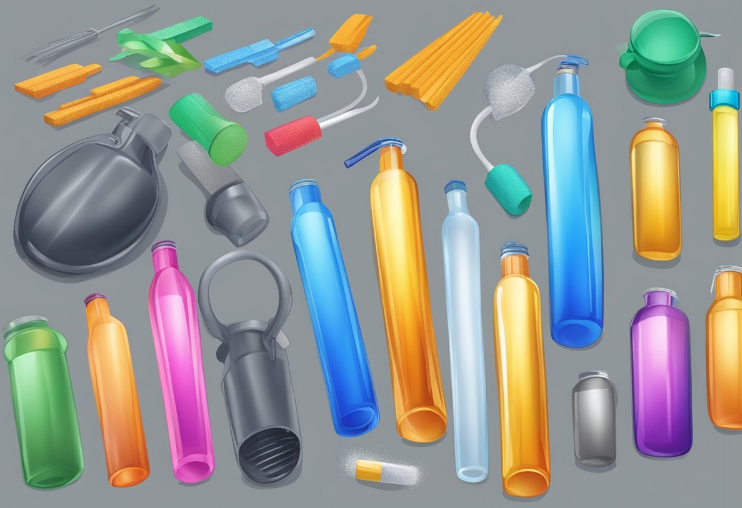
Dosage Considerations
Determining the right dosage of heat stabilizers is essential. Too little may result in insufficient protection against heat, while too much can adversely affect the polymer’s properties. Manufacturers often conduct trial runs to identify the optimal levels for specific applications.
Monitoring and Adjustments
Continuous monitoring during the manufacturing process allows for real-time adjustments to formulations. This adaptability is crucial for maintaining product quality and ensuring that the final product meets the required performance standards.
The Future of Heat Stabilizers in Polymers: Trends to Watch
Sustainability Focus
As environmental concerns grow, the demand for sustainable heat stabilizers is on the rise. Manufacturers are increasingly exploring bio-based and non-toxic alternatives that minimize environmental impact without compromising performance. This trend is reshaping product development strategies across the industry.
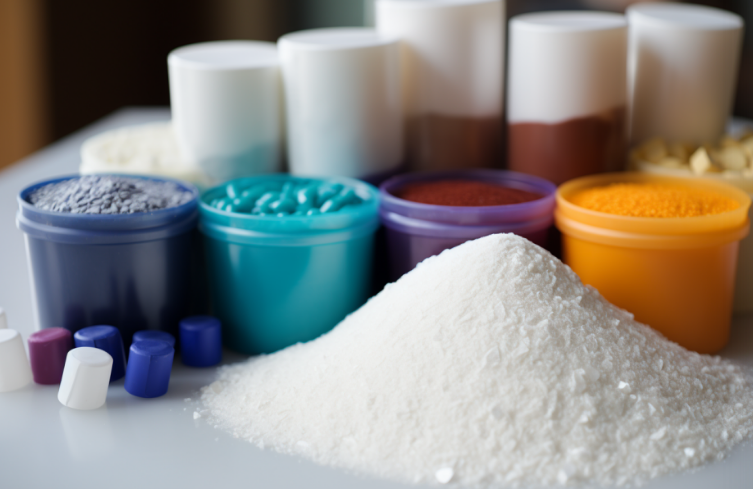
Innovations in R&D
Research and development are key drivers in the evolution of heat stabilizers in polymers. Companies like Shanghai Chembroad New Materials Co., Ltd. invest heavily in R&D to create innovative solutions that meet the changing needs of their customers. Their strong R&D team is dedicated to anticipating market trends and developing products that align with sustainability goals.
Regulatory Changes
As regulations surrounding polymer additives tighten, manufacturers must stay informed about compliance requirements. This includes understanding new guidelines for the use of heat stabilizers and ensuring that products meet safety and environmental standards. Companies that proactively adapt to these changes will maintain a competitive edge in the market.
Technical Support and Quality Control
Comprehensive Testing Facilities
Shanghai Chembroad New Materials Co., Ltd. boasts state-of-the-art testing equipment that ensures rigorous quality control throughout the production process. From raw material inspection to final product testing, every step is closely monitored to uphold the highest quality standards.
Commitment to Customer Service
With nearly 30 years of experience, Chembroad’s technical support team is dedicated to assisting customers in resolving application challenges. Their approach is customer-centric, ensuring that they respond promptly to inquiries and provide tailored solutions based on specific needs.
Long-Term Collaborations
Chembroad collaborates with independent laboratories, universities, and research institutions to foster innovation. This synergy enhances their R&D capabilities and allows for the continuous development of new product models that cater to diverse market demands.
Conclusion: The Path Forward
Heat stabilizers in polymers are vital for enhancing performance while addressing environmental concerns. As the industry evolves, staying ahead of compatibility issues, incorporating effective stabilizers, and embracing sustainable practices will be essential. Companies like Shanghai Chembroad New Materials Co., Ltd. lead the way in R&D and customer service, ensuring that they not only meet but exceed market expectations. By prioritizing innovation and sustainability, the future of heat stabilizers in polymers looks promising.